Mention the term “power quality” when troubleshooting in an electrical setting, and fear/intimidation almost inevitably set in — even amongst the most seasoned engineers and electricians. By their very nature, electrical professionals enjoy the study of technology. And because power quality issues can create some of the most mysterious problems out there, they’re constantly looking to better understand what power quality is, the specific disturbances that fall under its umbrella, the effect of interferences on equipment, and how to correct such problems.
Despite advances in technology, power quality is no small issue in today’s electrical environment. On the plant floor, VFDs trip and shut down processes, PLCs give false temperature alarms, and circuit breakers mysteriously trip. In office areas, lights flicker, computers lock up, and an annoying hum is heard in telephone lines. In data centers, chillers supplying vital cooling shut down, resulting in server high-temperature alarms and server shutdown. Because power quality problems can easily run into billions of dollars annually, it’s essential that electrical technicians troubleshooting such situations first understand the practical definition of power quality.
In a word
There are textbook and standards definitions for the term “power quality.” However, in the field, a practical, working knowledge of the term is still needed. For example, IEEE Std 1159-2009, IEEE Recommended Practice for Monitoring Electric Power Quality, defines power quality as “the concept of powering and grounding electronic equipment in a manner that is suitable to the operation of that equipment and compatible with the premise wiring system and other connected equipment.” While this is certainly true, it does little to help you explain to upper management why the conveyor motor just tripped!
From a practical standpoint, think of power quality as a measure of how well the electrical distribution system supports proper operation of its loads. If you have no problems with your electrical loads, you have no obvious power quality issue. If you suffer utility blackouts, overheating transformers, circuit breaker trips, neutral conductors overheating, computer lockups, or unexplained equipment downtime, you most likely have power quality-related culprits at work in your facility. Whether or not these issues turn into significant problems depends upon their severity and your plant operation.
Helpful resources
Because the effects of the same power quality problem vary so widely between facilities and equipment, the Information Technology Industry Council developed the ITI (CBEMA) Curve to help predict solid-state equipment reaction to voltage disturbances (click here to see Fig. 1). While the curve does not apply to all electronic equipment, it does help describe an AC input voltage envelope that typically can be tolerated by most information technology equipment. Understanding and using the curve can help in power quality troubleshooting.
Another important standard is the IEC 61000-4-30, Testing and Measurement Techniques - Power Quality Measurement Methods, which is the international standard for measurement and interpretation of power quality parameters. Of practical use for those wishing to learn more about power quality is NFPA 70B, Recommended Practice for Electrical Equipment. The current 2010 edition Chapter 10 begins with an explanation of power quality terminology and then details various power quality problems, including their causes and recommended solutions.
PQ culprits
Electrical disturbances occur constantly in electrical distribution systems. When a disturbance exceeds a specified value, it’s said to create a power quality event. Because power quality is the study of the voltage and current in your distribution system, you can measure and monitor many events by looking at the 60-Hz sine wave.
Ideally, we think of the power in our facilities as a pure 60-Hz, 3-phase sine wave. Realistically, however, this isn’t the case. Some voltage sine waves will be at a greater or smaller magnitude than their previous counterparts. Nonlinear loads do not draw current for the complete cycle of the sine wave, resulting in distortion of the original or fundamental 60-Hz sine wave (Fig. 2). As equipment is switched on and off, transients (or so called “spikes”) may occur along the sine wave. Depending upon the magnitude and longevity of these occurrences, some electrical equipment will be affected — some won’t. It’s the electrical professional’s job to determine the disturbance and its severity, its source, and a resolution. Power quality disturbances are categorized by their effects in relation to sine waves (see Table available on the EC&M website at http://www.ecmweb.com/images/012ecmIPQtable.pdf.
Handling harmonics
Harmonics are currents that are integer multiples of the fundamental frequency. For example, the third harmonic is current that flows in the system at three times 60 Hz or 180 Hz. The fifth harmonic is made up of currents that flow at five times 60 Hz or 300 Hz. Overall, harmonic currents distort the fundamental 60-Hz sine wave, causing problems from computer lockups to PLC misoperation and VFD trips. Total harmonic distortion (THD) is a measure of this created distortion. While there are engineering calculations to determine the amount of sine wave distortion created, power quality analyzers read out this THD value.
In addition to distortion of the 60-Hz fundamental sine waves, each harmonic creates its own problems. For example, the third harmonic creates overheating of neutral conductors and transformers. The fifth harmonic tends to create reverse torque in motors, resulting in motor overheating, inefficiency, and premature motor failure. Other problems created by harmonics range from nuisance operation of protective devices to audible noise in electrical switchgear, interference on telephone circuits, loss of computer data, and improper operation of facility distribution control systems, such as lights, clocks, and load shedding.
Once the source of harmonics is identified, filters may be added to reduce the harmonic currents reflected back into the system. Other fixes might include oversizing neutral conductors, isolating harmonic sensitive loads, replacing transformers with K-factor-rated transformers designed to carry harmonic currents, and the use of inverter duty-rated motors on VFDs.
Interference identification
Transients are very short-duration, high-amplitude increases along the voltage sine wave, sometimes referred to as voltage “spikes.” The most severe transients are caused by lightning strikes. The operation of a large load, such as a plant chiller, or the switching of capacitor banks by a utility can cause transients. Depending on the severity, transients can cause a VFD to trip on overvoltage, break down insulation over time in distribution systems, or completely destroy equipment. Luckily, you can monitor and measure transients (click here to see Fig. 3). Proper grounding and bonding and surge protection are important in protecting against transients.
Sags and swells are the most common types of power quality disturbances, resulting in downtime losses totaling millions of dollars each year. Sags (known as dips in the international standards) are a decrease to between 10% and 90% of the normal voltage. Swells are an increase to between 110% and 180% of normal voltage. Both sags and swells, which can cause misoperation of equipment, can last for a duration of 0.5 cycles to 1 min. Sags may cause equipment to drop off line. Swells can damage insulation over time. Changing transformer tap settings, soft starts on large loads, and isolating equipment are just a few solutions for sags and swells.
A long-duration undervoltage creates more severe effects than sags. Sustained voltage interruptions occur when the supply voltage drops to less than 10% on one or more phases for a period greater than 1 min. — a situation that often creates an entire plant or process shutdown.
Single-phasing, the loss of one phase in the distribution system, can result in almost immediate destruction of motors, in addition to the loss of single-phase loads operating on the lost phase. Under these circumstances, shutdown of equipment to a complete trip of the entire distribution system can occur.
Unbalanced voltage between phases can overheat motors, transformers, generators, and associated wiring. Unbalanced loading across the three phases results in this unbalanced voltage and is corrected by balancing loads.
Noise is undesirable electrical signals in an electrical or electronic circuit and can cause data loss or corruption, hum in telephone systems, and the often unexplained malfunction of electronic equipment. Proper grounding and bonding is often the key to minimizing such noise.
Interharmonics are harmonic currents that occur at less than the fundamental frequency and can cause lights and CRTs to flicker and communication circuit noise. Filtering and isolation of affected equipment are possible solutions.
Flicker is the change in light output from a lamp caused by the fluctuation of the supply voltage. Flicker is uncomfortable to the human eye and must be minimized. Arc furnaces and welders, medical imaging machines, and lamp dimmers can be responsible for flicker. Isolating lighting circuits often helps to reduce flicker.
Electrical professionals must be able to recognize power quality disturbances, know their causes/effects, monitor their distribution systems for power quality events, and solve these issues. While the engineering side of power quality can be intimidating, a practical understanding of power quality allows for the detection and elimination of many mysterious electrical troubleshooting problems.
Barnett is an energy auditor/trainer with American Trainco, Englewood, Colo. He can be reached at [email protected].
About the Author
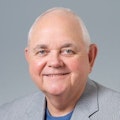
Randy Barnett
CESCP
Randy Barnett is an NFPA Certified Electrical Safety Professional, a long-time journeyman electrician, instructor and author with expertise in industrial electrical construction and maintenance. He is Electrical Codes & Safety Manager for NTT Training. Because of his ability to develop and deliver quality programs, Randy has trained more than 10,000 students in all 50 states, including Canada, Singapore, Afghanistan, Dubai, Trinidad, and Saudi Arabi. His articles appear in numerous trade publications and, his book on "Commercial and Industrial Wiring" is used as an entry-level text in many electrician training programs. Randy also appears at various corporate and trade association speaking engagements and consults on training program design and implementation. Randy is a graduate of the U.S. Navy Nuclear Power School, served as a nuclear electrician in submarines and holds a B.S. in business.