Today’s 3-phase motors are more energy-efficient than their counterparts of only a couple of decades ago. Much of this is because of more precision in design, which allows for tighter tolerances and overall better construction. The newer motors use less energy and last longer.
Yet in many facilities, the improvement is wasted. The motors still are energy hogs and don’t last nearly as long as they should. Why is this?
The most common problem is voltage imbalance (at the stator terminals). This imbalance causes a disproportionately large phase current imbalance, which means the motor is using less of the input energy to generate torque and more of it to generate waste heat. The excess heat reduces motor life.
But that’s only part of the story. If the phases aren’t “pulling” equally, the motor isn’t rotating smoothly. It’s being jarred harder by one phase or two phases than another. This herky-jerky motion produces excess vibration. You actually get torque pulses, and those are felt by the load. If you want to tear up a gearbox, high-voltage imbalance is a great way to do it!
Other mechanical stresses also are generated. For example, some of that that torque-pulsing may cause hysteresis in the motor base (usually made of metal) or cause crumbling in the motor pedestal (often made of concrete).
As you can see, phase imbalance wastes more than just energy lost to less efficient operation. It leads to premature failure of various components of the motor system and even the load. All of which means higher total cost of ownership and less uninterrupted production time.
A general guideline for 3-phase motors is that the highest voltage should not exceed 2% of the lowest voltage. NEMA MG-1 defines voltage imbalance as the deviation from the average of the three voltages.
So add up the voltage measured on each phase and divide by three. Let’s say your average voltage is 478. If you take 2 percent of that, you have 9.56. This gives you a range of about 487V on the high end and about 469V on the low end, allowing for some minor variance in actual voltage throughout the day.
Keep in mind that any imbalance is bad, it’s just a matter of magnitude. If you’re within that 2%, you probably won’t see the worst effects, but you still will have energy losses.
For a very large motor, these losses may be significant enough to merit correcting the imbalance. For a critical motor, maximizing its reliability may dictate eliminating the imbalance to the extent feasible.
Lighting loads are single-phase loads, but often are connected to a 3-phase system (e.g., 277V). If you have imbalance, look to the lighting loads as the likely source. You may need to move a few luminaires around on the existing circuits to balance things back out or move entire circuits.
One way to address voltage imbalance is to put 3-phase motors on their own supply (transformer and panel). This may seem expensive because it means you’ve got to set more transformers and panels in a given area. But this practice is nearly always more cost-effective than paying for voltage imbalance.
About the Author
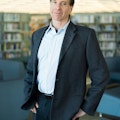
Mark Lamendola
Mark is an expert in maintenance management, having racked up an impressive track record during his time working in the field. He also has extensive knowledge of, and practical expertise with, the National Electrical Code (NEC). Through his consulting business, he provides articles and training materials on electrical topics, specializing in making difficult subjects easy to understand and focusing on the practical aspects of electrical work.
Prior to starting his own business, Mark served as the Technical Editor on EC&M for six years, worked three years in nuclear maintenance, six years as a contract project engineer/project manager, three years as a systems engineer, and three years in plant maintenance management.
Mark earned an AAS degree from Rock Valley College, a BSEET from Columbia Pacific University, and an MBA from Lake Erie College. He’s also completed several related certifications over the years and even was formerly licensed as a Master Electrician. He is a Senior Member of the IEEE and past Chairman of the Kansas City Chapters of both the IEEE and the IEEE Computer Society. Mark also served as the program director for, a board member of, and webmaster of, the Midwest Chapter of the 7x24 Exchange. He has also held memberships with the following organizations: NETA, NFPA, International Association of Webmasters, and Institute of Certified Professional Managers.