Tip of the Week: Optimizing Your Motor Maintenance Program
Unless you’re analyzing motor failure causes and planning your maintenance accordingly, your motor maintenance program isn’t optimally allocating resources to motor failure prevention. When upper management sees the maintenance budget and also sees many production interruptions because of motor failures, what conclusions can they draw? Probably none that are healthy for your long-term employment prospects in that company.
Often, maintenance is designed around perceptions and myths rather than the reality of hard data. Worse, excuses are made to avoid taking blame and making the necessary changes. Here’s an example of this situation.
Typically, the motors in a given area are of the same brand. When they start failing, it’s nearly always because of maintenance deficiencies. But how convenient that they are the same brand! Instead of solving the problem, you can blame that particular manufacturer.
Yet, it’s simply not true that an established brand has been getting by for decades with producing junk and your failure rates would be hugely different if only the idiot specifier who bought these had picked a different brand.
What makes failure rates hugely different isn’t the brand. It’s essential that you have the right motor for the application and that it’s properly installed. But after that, the difference arises because of how well maintenance is correlated to, and planned against, the known failure causes. In other words, work from your data.
About the Author
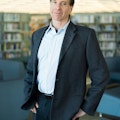
Mark Lamendola
Mark is an expert in maintenance management, having racked up an impressive track record during his time working in the field. He also has extensive knowledge of, and practical expertise with, the National Electrical Code (NEC). Through his consulting business, he provides articles and training materials on electrical topics, specializing in making difficult subjects easy to understand and focusing on the practical aspects of electrical work.
Prior to starting his own business, Mark served as the Technical Editor on EC&M for six years, worked three years in nuclear maintenance, six years as a contract project engineer/project manager, three years as a systems engineer, and three years in plant maintenance management.
Mark earned an AAS degree from Rock Valley College, a BSEET from Columbia Pacific University, and an MBA from Lake Erie College. He’s also completed several related certifications over the years and even was formerly licensed as a Master Electrician. He is a Senior Member of the IEEE and past Chairman of the Kansas City Chapters of both the IEEE and the IEEE Computer Society. Mark also served as the program director for, a board member of, and webmaster of, the Midwest Chapter of the 7x24 Exchange. He has also held memberships with the following organizations: NETA, NFPA, International Association of Webmasters, and Institute of Certified Professional Managers.