A solution in search of a problem usually isn’t a good idea. But there are exceptions.
For example, consider a smoke detector in your home. It isn’t there because you have fires all the time and would like to know about them. You probably will never have a fire, but if you do, that smoke detector may save your life.
Electrical test equipment is another exception, but in a way that differs from the smoke detector example.
Consider the insulation resistance tester. Why do you buy these? It’s not because you have cable failures (a problem) and want to verify that after the fact. It’s because you want to be able to replace deteriorating cables before they become failed cables. You want to solve the problem before it exists.
If you have a cable testing program that trends results, you can identify cables that are heading down the road to failure. This is a form of predictive maintenance. You predict the failure, then intervene to prevent it.
It’s much more cost-effective to schedule time to replace cables than to deal with a large failure — especially ones that occur at the worst possible time (as they typically do).
But how do you justify the expense of several insulation resistance testers, training, scheduled shutdown for testing, and the time for analyzing and trending the results? If the cost is X, can you tie X directly to a unit of revenue? You haven’t yet identified potential cable failures to know which cables will probably fail and (consequently) stop which areas of production, so the answer is no.
In most facilities, there’s a fixed budget for maintenance, and there’s often pressure to reduce that budget. Skimping on test equipment is one way to stay within the budget, but ultimately that approach makes the maintenance organization less able to protect the revenue stream that keeps your facility open. You need to get the equipment.
You might put in a capital request for additional funds beyond to buy new test equipment, but because you can’t tie the investment directly to revenue, how do you convince the bean counters it’s in the company’s best interests to obtain that equipment?
In other words, what problem is this solution searching out? And how much does it cost?
You won’t see the problem without the test equipment, so how can you answer these questions?
Let’s reframe that. You won’t see the specific problems at your facility without this test equipment, which means you won’t be able to discover the costs that are lurking in your facility’s physical assets. But you can find examples of specific problems at other facilities, and relate those to potential problems and costs in your facility.
One way to do this is to hire a qualified testing firm to conduct the tests you would conduct if only you had that equipment. But how do you get approval to hire this firm? They have other clients, and they have photos. They also have hard data. They have what it takes to make the case to do in your facility what they’ve done in other facilities.
If you really want to shock the socks off those bean counters, use the images from a thermographic survey of a problem facility. You can show what the testing firm found at a similar plant, and also show (non-infrared) photo after photo of your own panels with thousands of connections and components. Each of these has the potential to go bad, and some might already be on the verge of failing.
By showing “comparables” visually, you move the discussion from being abstract to being about the physical assets in your facility. This is our switchgear that supplies power to these production lines that provide $325,000 an hour of revenue. How many of those hours do you want to give up by not making this investment?
The discussion is also about specific problems. For example, you want insulation resistance testing so you can stop cable failures from ever happening. You can’t tie your specific cables to any specific revenue just yet, but you can certainly tie someone else’s failed cables to photos of the catastrophic consequences at their facility; ask the testing firm.
Another example: You want thermographic surveys and analysis so you can identify and repair energy-losing, heat-producing, maybe even arc blast-risking bad connections. But what else can thermography identify for you? Make that list (it’s long and it can go way past electrical connections), and put it in your capital request.
Once the testing firm has the (possibly depressing) test results for you, it should be easy to justify having it come back for the next shutdown. This also should open the door to purchasing your own equipment for conducting ongoing maintenance between shutdowns and maybe even hiring extra people. This way, you can keep those problems solved before they ever happen.
About the Author
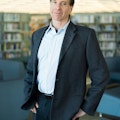
Mark Lamendola
Mark is an expert in maintenance management, having racked up an impressive track record during his time working in the field. He also has extensive knowledge of, and practical expertise with, the National Electrical Code (NEC). Through his consulting business, he provides articles and training materials on electrical topics, specializing in making difficult subjects easy to understand and focusing on the practical aspects of electrical work.
Prior to starting his own business, Mark served as the Technical Editor on EC&M for six years, worked three years in nuclear maintenance, six years as a contract project engineer/project manager, three years as a systems engineer, and three years in plant maintenance management.
Mark earned an AAS degree from Rock Valley College, a BSEET from Columbia Pacific University, and an MBA from Lake Erie College. He’s also completed several related certifications over the years and even was formerly licensed as a Master Electrician. He is a Senior Member of the IEEE and past Chairman of the Kansas City Chapters of both the IEEE and the IEEE Computer Society. Mark also served as the program director for, a board member of, and webmaster of, the Midwest Chapter of the 7x24 Exchange. He has also held memberships with the following organizations: NETA, NFPA, International Association of Webmasters, and Institute of Certified Professional Managers.