Critical Code Requirements for Class III Hazardous Locations
Of the three types of Hazardous Locations, Class III has the least stringent requirements. Fibers (and flyings) have a much larger particle size than dust (Class II) or gases (Class I). That makes fibers easier to contain and control. But that doesn’t mean they aren’t dangerous or pose less of a threat than the other two types of hazards. People killed in Class III incidents aren’t any less dead than those killed in Class II or Class I.
While explosions can happen in Class III Hazardous Locations (depending on the material and the accumulation of it), the more typical threat in such places (generally) is fire. Depending upon the dispersion pattern/density of the ignitable materials, fire could spread rapidly and suck the oxygen out of the air before people can escape.
The point here is that you not discount the need for compliance just because the requirements aren’t as strict. Also note that they are still minimum requirements, and there may be factors that make it prudent to exceed those requirements. Always analyze the installation to see what’s really needed.
Carbonization and such
Almost right away, we get into a confusion factor with Art. 503. The surface temperature requirements in 503.2 can be a bit of a mind-bender.
How are you supposed to know, for example, what the operating temperature of the equipment will be when blanketed with the maximum amount of dust (simulating fibers/flyings) that can accumulate on the equipment? Or how much dust simulates the fibers/flyings to the maximum extent?
The solution is to get the operating condition information (how much dust) from the owner/operator and the operating temperature information (under those conditions) from the manufacturer.
Article 503 doesn’t have express listing requirements. Gee, what a relief! You don’t need to worry about whether the equipment is listed for Class III. Or do you? That mystery is cleared up with a careful reading of 500.8(A), which discusses equipment suitability.
Equipment can be rendered unsuitable if you don’t know what the limitations and cautions are for installing it. Note that 503.5 has a temperature limit requirement of 329°F for equipment that is not subject to overloading and a temperature limit requirement of 248°F for equipment that is. To ensure you’ll meet this requirement, you first need to determine whether the equipment is subject to overloading. That’s an assessment based on its function. Then you’ll need to verify with the manufacturer whether it meets those temperature limits.
Zone equipment
This is another area where confusion can lead to violations. With Class I and Class II locations, you want to keep a clear distinction between Zone and Division to prevent an à la carte situation. But with Class III, it’s OK to blur that distinction in a couple of specific ways:
- In Class III, Div. 1 locations, you can use equipment that’s listed and marked for Zone 20 locations [per 506.9(C)(2)].
- In Class III, Div. 2 locations, you can use equipment that’s listed and marked for Zone 20, 21, or 22 locations [per 506.9(C)(2)].
- In both cases, if the equipment is:
- Subject to overloading, its temperature class can’t be more than T120°C.
- Not subject to overloading, its temperature class can’t be more than T165°C.
Grounding and bonding
The first requirement presented for grounding and bonding is that all Class III location equipment be grounded and bonded as specified in Art. 250 [503.30]. But it’s a big Article, and arguably the least understood.
So someone working in a Class III location duly drives a ground rod next to a motor, connects it to the equipment grounding lug, and considers the motor to be grounded. Well, yes, it is grounded (connected to the dirt; see Art. 100 definition). What purpose does this serve? The motor is still at a different potential from the transformer sitting four feet away from it.
When we speak of “equipment grounding,” we really mean equipment bonding (Part V of Art. 250). That “equipment grounding conductor” is really a bonding conductor, though ultimately that bonding system connects to the grounding system.
The language of 503.30 is ahead of much of the rest of the NEC in reflecting the aforementioned facts. The title of 503.30(B) changed from “Types of Equipment Grounding Conductors” in the 2011 NEC to “Types of Equipment Bonding Conductors” in the 2014 NEC.
Always bond on the load side; that’s how you put all the equipment at the same potential. Grounding things instead of bonding them can still leave a lethal shock hazard.
Section 503.30 also says not to rely on locknut-bushings or double locknuts for bonding purposes. Use bonding jumpers with proper fittings (or other approved means) wherever you connect a metallic raceway. From a reliability standpoint, this is a good engineering practice whether a location is classified or not. That’s why data centers typically use these bonding jumpers.
Transformers in Class III locations
The requirements for a transformer in a Class III location are the same as for one in a Class II, Div. 2 location [503.100]. So what are those requirements?
If the transformer:
- Contains liquid that will burn, then it must be installed in a vault that complies with 450.41 through 450.48 [502.100(B)(1)].
- Contains askarel and is rated in excess of 25kVA, then it must be provided with a pressure relief vent and with a means of absorbing any gases generated by arcing inside the case (or, alternatively to absorption, the pressure relief valves must be connected to a chimney or flue that will carry the gases outside). Not only that, it must have an airspace of at least 6 in. between the transformer case and any combustible material [502.100(B)(2)].
- Is a dry-type, then it must be installed in a vault or have its windings and terminal connections enclosed in tight metal housings without vents or other openings. Not only that, but the transformer can’t operate at over 600V nominal [502.100(B)(3)].
Motors in Class III locations
Regardless of Division, motors, generators, and other rotating machinery in Class III locations must be totally enclosed non-ventilated, totally enclosed pipe ventilated, or totally enclosed fan cooled [503.125].
Exceptions can be made with the approval of the Authority Having Jurisdiction, but only for:
1. Self-cleaning motors of the textile type.
2. Standard open-type machines without sliding contacts or other types of switching mechanisms.
3. Standard open-type machines with the aforementioned contacts, but enclosed within tight, unventilated housings.
The goal of these restrictions is to keep fibers out of motors. Failure to do that is an NEC concern because of combustion risks. For the designer, it’s a reliability concern regardless of what the NEC says. Fibers/flyings can accumulate in the vents and choke off the air supply, causing the motor to shut down and production to stop.
The vent-clogging problem from using an unsuitable (and Code-violating) motor occurred in a paper plant. Rather than replace the motor, they installed a bottom-vented sheet metal guard around it. This was relatively inexpensive, but still not Code-compliant. And fibers still got in.
Luminaires in Class III locations
The requirements for luminaires in Class III locations address three types of lighting: pendant, portable, and fixed.
When suspending a pendant luminaire, the stem must be threaded. You can use rigid metal conduit, intermediate metal conduit, or tubing (yes, you can thread tubing). Alternatively, you can use chains with approved fittings [503.130(C)].
Lamendola is an electrical consultant located in Merriam, Kan. He can be reached at [email protected].
About the Author
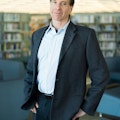
Mark Lamendola
Mark is an expert in maintenance management, having racked up an impressive track record during his time working in the field. He also has extensive knowledge of, and practical expertise with, the National Electrical Code (NEC). Through his consulting business, he provides articles and training materials on electrical topics, specializing in making difficult subjects easy to understand and focusing on the practical aspects of electrical work.
Prior to starting his own business, Mark served as the Technical Editor on EC&M for six years, worked three years in nuclear maintenance, six years as a contract project engineer/project manager, three years as a systems engineer, and three years in plant maintenance management.
Mark earned an AAS degree from Rock Valley College, a BSEET from Columbia Pacific University, and an MBA from Lake Erie College. He’s also completed several related certifications over the years and even was formerly licensed as a Master Electrician. He is a Senior Member of the IEEE and past Chairman of the Kansas City Chapters of both the IEEE and the IEEE Computer Society. Mark also served as the program director for, a board member of, and webmaster of, the Midwest Chapter of the 7x24 Exchange. He has also held memberships with the following organizations: NETA, NFPA, International Association of Webmasters, and Institute of Certified Professional Managers.