Full Coverage of Combustible Coating Equipment
Article 516 of the NEC applies to things you use every day. Walk into your kitchen for example. The metal panels of your range, dishwasher, and refrigerator all underwent finish application operations using equipment compliant with this area of the NEC. The cores of the motors in these appliances were dipped in Art. 516-compliant systems, as were the cores of the motors used in the assembly of these appliances (Photo 1 and Photo 2).
Service trucks, buses, planes, trains, and automobiles all are made with components in their manufacture or finishing subject to Art. 516 requirements. Examples are everywhere, making this part of the Code a pretty important part of the NEC. But what does it say?
That’s an especially important question with the 2014 NEC, because if you’re looking at it, you’ll notice nearly all the text in the first half of it is highlighted — which means there’s been a whole lot of revising going on.
So if you’ve been applying the requirements of this Article for many years, be warned that what you used to know about it isn’t what you need to know about it now.
Scoping it out
First, understand that Art. 516 applies only when the application of combustibles (in liquid or powder form) is both:
1. Above the flashpoint of the materials being applied.
2. Regular or frequent.
The method of application isn’t relevant to the question of Art. 516’s applicability. Spraying, dipping, and printing are just some common examples. Because these installations pose so many potential problems, the informational note in 516.1 mentions several applicable standards. You may need to consult these as well.
It’s not an explicit NEC requirement, but routing conductors with operations and maintenance in mind is a good design practice, so scope out the actual usage of the equipment. For example, suppose it’s a varnish dipping machine that, once the part emerges from the vat, gives the part a quick spin. This machine will accumulate dried varnish on the dipping arm, and someone will have to remove it. When planning your raceway installation, allow room for a person on a ladder to do this maintenance without having to squeeze between raceway and the machine.
Because you’re dealing with combustibles, you also must know the Hazardous Location classification of each little area you’re working in. Article 516 takes up about nine and a half pages; four and a half are devoted to describing and illustrating rules related to classification (see The Arrangement of Article 516).
Location classification
Even though Art. 500 through Art. 507 cover hazardous locations, about 45% of Art. 516 is devoted to how you classify a location. If you’re at this point in Art. 516, stop. Read through Art. 500 before proceeding further so that you have a foundation for understanding what comes next. Focus your attention on Sec. 500.5 “Classifications of Locations,” which sounds remarkably like 516.3 “Classification of Locations”. Only one letter differs between the two titles.
These tips will help you wade through, decipher, and correctly apply the requirements of 516.3:
• Only a qualified person can make the official classification. Find out from the owner (existing installation) or architect (new installation) what the classification is for each specific area. Note that, for electrical purposes, Art. 516 provides some override of this.
• Go to the appropriate subsection (A, B, C, or D) for the location, based on its classification.
• It is possible for an area to have overlapping classification between the Zone and Division systems. However, don’t intermix Zone and Division for any given source of release, regardless of how an area is classified [516.3(A)(2) and (3)]. In the event of an actual overlap, use the Zone system [516.3(A)(1)].
• For electrical purposes, some equipment or locations will have a mandated classification, regardless of what the owner or architect says. Examples include the inside of vessels (Class I, Zone 0) [516.3(A)(1)], the interior of any dip tank (Class I, Div.1 or Zone 0) [516.3(B)(3), and open-front spray booths (Class I, Div. 2 or Zone 2; or Class II, Div. 2 or Zone r2) [516.3(D)(2).
• Pay close attention to seemingly minor things such as Class I, Div. 2 and Zone 2 versus Class II, Div. 2 and Zone 22. Remember that a Class II or Class III area has two digits in its zone number. See Art. 506 for a full explanation.
If your location is any of the following:
• Class I, Div. 2
• Class I, Zone 2
• Class II, Div. 2
• Zone 22 (no Class designation needed, here)
...you need to apply 516.3(D). This is dense material to wade through, but two things will help you:
1. Each of its eight subheadings is application-specific. Pick the one that describes your location.
2. The 10 figures (up from seven in the 2011 NEC) are also application-specific, and they will help you see how the classifications are laid out or defined for a given application. Study these carefully to avoid misinterpretation.
The final two subsections of 516.3 address unclassified locations.
Wiring methods
Now that you’ve figured out which classifications you’re working with, you’re ready to apply the wiring method requirements. If the location is:
• Class II. Apply Art. 502 (Division system) or Art. 506 (Zone system).
• Class III. Apply Art. 503 (Division system) or Art. 506 (Zone system).
If the location is unclassified and the:
• Wiring is above a Class I or II area, use only wiring methods permitted by 516.7(A).
• Equipment could produce ignition, use totally enclosed versions or equipment constructed to prevent the escape of sparks or hot metal particles [516.7(B)].
So what about Class I locations? You’re going to apply Art. 501 (Division system) or Art. 505 (Zone system), except as modified by 516.4.
Something very noticeable about this Section is all of Subsection C (Illumination) is highlighted. The 2011 NEC had three lines of text followed by five short, enumerated requirements. The 2014 NEC doesn’t have the paragraph and has a completely different, much more detailed, list of four requirements.
The first three requirements are meant to be used with the three accompanying Figures. The fourth requirement is about glass panels.
As with the 2011 NEC, portable equipment, including lights, can’t be used in a spray area during spray operations [516.7(D)]. The same exceptions apply; Subsection D is identical to the 2011 version.
Subsection F, dealing with electrostatic discharge, is new with the 2014 NEC. Basically, it says that all persons and electrically conductive objects must be bonded to eliminate differences of potential. It also requires a means of dissipating static charges from nonconductive substrates in printing processes.
Special equipment
The next Section is 516.10, “Special Equipment”. For the purposes of this Section, the equipment will fall into one of three categories:
1. Fixed. Attached to a mechanical support or manipulator [516.10(A)].
2. Hand-held. Manipulated by hand during the spraying operation [516.10(B)] (Photo 3).
3. Powder coating. Where combustible powders are applied [516.10(C)]. You’ll still apply 516.10(A) or (B), depending on fixed or hand-held. But if it’s a power application additional requirements apply. Mostly, these requirements mean (yet again) to bond equipment to eliminate differences of potential.
Grounding and bonding
At the end of Art. 516, you find a requirement that all fixed or portable equipment be “grounded and bonded” [516.6]. This really means bonded; refer to the Art. 100 definitions of bonding and grounding.
If you “ground” two pieces of equipment, you aren’t going to put them at the same electrical potential. There will be a voltage between them, and if you know the impedance of the soil between their respective ground rods, you can calculate that voltage.
One way to simplify a project that falls under Art. 516 is to just ensure there’s a bonding jumper to each metallic object and the bonding path maintains integrity. This not only eliminates “deciphering time” during the design, but it also eliminates
work-stopping questions in the field. This requirement is repeated for so many permutations and situations throughout Art. 500 through Art. 505 and Art. 516 that it’s a challenge to find where unbonded metallic objects are permitted, if at all, in those Articles.
Lamendola is an electrical consultant located in Merriam, Kan. He can be reached at [email protected].
SIDEBAR: The Arrangement of Article 516
This is a fairly long Article of the NEC, but once you get past the scope and definitions, you’ll see it has only four subsections:
• 516.3 Classification of Locations. Most of this is new with the 2014 NEC.
• 516.4 Wiring and Equipment in Class I Locations. Much of this is new with the 2014 NEC.
• 516.7 Wiring and Equipment in Class I Locations. Almost unchanged from the 2011 NEC and only two paragraphs in length.
• 516.10 Special Equipment. Some of this is new with the 2014 NEC.
About the Author
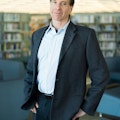
Mark Lamendola
Mark is an expert in maintenance management, having racked up an impressive track record during his time working in the field. He also has extensive knowledge of, and practical expertise with, the National Electrical Code (NEC). Through his consulting business, he provides articles and training materials on electrical topics, specializing in making difficult subjects easy to understand and focusing on the practical aspects of electrical work.
Prior to starting his own business, Mark served as the Technical Editor on EC&M for six years, worked three years in nuclear maintenance, six years as a contract project engineer/project manager, three years as a systems engineer, and three years in plant maintenance management.
Mark earned an AAS degree from Rock Valley College, a BSEET from Columbia Pacific University, and an MBA from Lake Erie College. He’s also completed several related certifications over the years and even was formerly licensed as a Master Electrician. He is a Senior Member of the IEEE and past Chairman of the Kansas City Chapters of both the IEEE and the IEEE Computer Society. Mark also served as the program director for, a board member of, and webmaster of, the Midwest Chapter of the 7x24 Exchange. He has also held memberships with the following organizations: NETA, NFPA, International Association of Webmasters, and Institute of Certified Professional Managers.