In the beginning, there was DOS. And with DOS came a transition from paper work order systems to electronic ones-the early Computerized Maintenance Management System (CMMS). Fast forward to the CMMS of today. It outclasses yesterday's star at every turn. Today's Open DataBase Compliance (ODBC) is one of the features that allow quantum leaps in maintenance management and performance. To understand the full effect of OBDC, we must first cover three other features-file standardization, advanced analysis, and graphical interfaces.
File standardization Many of the first CMMS programs used proprietary databases. Thus, to move from one CMMS to a newer, more powerful one, you had to ditch all that information you so tediously keyed in. Fortunately, most vendors attacked this problem early on, by adopting dBase III and ASCII file standards (which also allowed interface with larger systems and mainframes).
File standardization paved the way for other developments, such as advanced analysis, because developers could write a single program to a standard file type rather than diluting their resources by trying to cover all the separately reinvented wheels.
Advanced analysis In CMMS's infancy, you could tally up a few figures for a rough idea of where your maintenance resources went. But you had few tools with which to sort and filter the information; reports from the system were often meaningless. CMMS companies realized end users wanted more than just the number of hours each craft spent on a work order. They responded by endowing their programs with a wide array of measurement and analysis features.
These features include accounting, trending, and predicting functions. Their real power came in the ability to tailor data collection to what the end user needs. Thus, if you want to know how many minutes of downtime your plant air motors suffer each month due to clogged air filters, you can set your system up to tell you that. If you want to compare that information to what happened last month, you can. Such functionality paved the way for advanced trending and prediction, based on real data. It also paved the way for making custom reports for upline management.
Graphical interfaces User interfaces were a major hurdle in using early CMMSs. Their text-only orientation forced the user to know complicated procedures and a long list of codes. Training costs were high, and errors were common. With the graphical interface, both training costs and error frequency plummeted. A quandary for CMMS developers was the platform problem. UNIX computers were, and still are, rare in maintenance shops. The same goes for Apple. Just a few years ago, nearly every maintenance department ran on Windows 3.0/311, which meant they could run only 16-bit applications. With Windows 95, and then the following year, Windows NT 4.0, maintenance departments gained the ability to run 32-bit programs. And most of these programs are ODBC-compliant. This ushered in a world of possibilities.
Reporting features Before we discuss what you can do with ODBC, let's discuss what some CMMS vendors did prior to its emergence. In the 16-bit world, you had the Object Linking and Embedding (OLE) standard, which allowed you to paste information from one application into another application. This alone was very powerful, because you could use a spreadsheet to create customized charts based on the data your CMMS collected.
Some vendors created crude reporting functions to satisfy the needs internal to the maintenance department. Some reporting functions allowed you to make a decent-looking chart. But until the advent of ODBC, it was difficult to make a good PowerPoint, Excel, or Intranet presentation based on your CMMS, which was often what you needed to give maintenance clout at the corporate level. Enter, ODBC.
The next generation: beyond work orders Your CMMS can show where you need to improve in training, testing, procedures, staffing, and other areas. That takes you beyond work order administration. Let's rise to the next level: using the CMMS to improve the power and stature of maintenance within the larger organization.
Most corporate managers view maintenance as an expense they'd rather not incur. Thus, corporate and plant gatekeepers try to reduce the money you get for test equipment, training and personnel. They are also tight on giving up any floor space or granting maintenance downtime.
Unfortunately, most companies accord lower status to maintenance groups than to production groups. This is partly because it's been so easy for so long to use "maintenance failure" as a cover for quality or quantity shortfalls. Production people made an art out of this. Doing so is not easy, however, when they face a maintenance manager armed to the eyeteeth with hard data presented in a visually striking format. Let's see how you can use a CMMS to create such armament.
Justify test equipment How do you justify test equipment purchases? Often, you base justification on trade experience, projected savings, manufacturer's literature, someone else's case histories, and other information you hope will sway the gatekeepers. Sometimes, you must be more compelling than this will allow.
Suppose you already own a hand-held oscilloscope and want to purchase another. Your purchase request comes back with a request for financial justification. You need numbers. So, you go to your CMMS and list completed work orders that involved motor drive repairs. You then pull up your test equipment data: you purchased your scope on June 15, 1996. Now you divide up your work orders: those done before the June 15 and those done after. Let's assume you kept track of which repairs used the scope and which didn't.
Suppose the numbers aren't as good as you'd hoped. You need to go into your CMMS again and view failure causes. Aha! Three drives "failed" because an operator "cleaned" them with a firehose (don't laugh-this actually happened!). Your CMMS says only Roger and Betty have drive training, but others attempted repairs. You filter things down to eliminate variables and come up with a typical drive repair time. Make sure you can explain which items you excluded and why. You can use the results to create a graph like that in Fig. 1. List the various production lines separately, so the manager of each line can see the hit that line takes on its bottom line.
Explaining training You can use the same approach you used for test equipment, but you can add a twist. Use your CMMS to correlate downtime codes with training completion codes by worker, and come up with a profile of downtime excess due to training deficit by production line. This takes quite a few steps, but it can be worth the effort. Fig. 2 shows what such a chart might look like. You may want to focus on, say, PLC training and PLC-related downtime.
Costs lost in space Don't you wish you could show how an increase in maintenance-reserved floor space reduces, say, breaker maintenance costs? Maybe with a before-and-after chart? This is a hard one to pull off. The battle for floor space is intense, and you need scientific purity to be convincing. For before/after comparisons, don't send a crew of two newbies the first time and a crew of six experienced people the next. Consider asking an operations manager to watch at least the setup portion of some of the tests.
Perhaps the best way to attack this is to track non-value-added activities. After all, moving things out of the way just to get at equipment adds no value but does cost you. You'll need to have someone jot down the types of non-value-added activities taking place under constricted space (e.g., moving carts and equipment). Make a code for non-value-added activities, and track them collectively as in Fig. 3.
Don't leave home without it Fig. 4 is one tool no maintenance department should be without. When fingers start pointing toward maintenance, whipping out a chart like this does wonders. Even better: if an operations manager wants to know where the training and supervision weaknesses are, you can chart the downtime by shift. You can use charts like this for political self-defense or, better, to build helpful relationships with under-the-gun production people.
Breaking breaker maintenance barriers When breakers need maintenance, you often get nuisance trips. Worse, breakers may not operate when they should. The bad news: if you have the second problem, you might not realize it until catastrophe hits. The good news: we can use the CMMS to track the first problem. Just report all breaker trips to the CMMS, then make a chart like that in Fig. 5.
I can see clearly now, the rain is gone.. This is just a hint of the power you can unleash from your CMMS. Consider making a list of the top three problems facing maintenance, three facing each production manager (offer your help, personally), and three facing the quality assurance department. Think about the kinds of information you collect or can collect in your maintenance and repair efforts. Then look for ways to use that information in charts that will help everyone see what's really there. Doing so makes your maintenance department a necessary team member, not a necessary evil.
About the Author
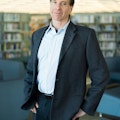
Mark Lamendola
Mark is an expert in maintenance management, having racked up an impressive track record during his time working in the field. He also has extensive knowledge of, and practical expertise with, the National Electrical Code (NEC). Through his consulting business, he provides articles and training materials on electrical topics, specializing in making difficult subjects easy to understand and focusing on the practical aspects of electrical work.
Prior to starting his own business, Mark served as the Technical Editor on EC&M for six years, worked three years in nuclear maintenance, six years as a contract project engineer/project manager, three years as a systems engineer, and three years in plant maintenance management.
Mark earned an AAS degree from Rock Valley College, a BSEET from Columbia Pacific University, and an MBA from Lake Erie College. He’s also completed several related certifications over the years and even was formerly licensed as a Master Electrician. He is a Senior Member of the IEEE and past Chairman of the Kansas City Chapters of both the IEEE and the IEEE Computer Society. Mark also served as the program director for, a board member of, and webmaster of, the Midwest Chapter of the 7x24 Exchange. He has also held memberships with the following organizations: NETA, NFPA, International Association of Webmasters, and Institute of Certified Professional Managers.