Contractors face unique challenges at every phase of a project — whether in planning, executing, or ongoing operations. Projects often encounter unexpected issues that require rapid problem solving. Large projects add another layer of complexity because they require several types of contracting companies to work together, which creates a mixture of best practices being utilized on the project site. To ensure all workers are on the same page and avoid confusion, inefficiencies, and even safety hazards, electrical contractors have the option to leverage the wealth of knowledge available from consultants or materials manufacturers. In increasing fashion, these upstream stakeholders are offering to provide best practices in training, equipment, and processes in the areas of standardization, safety, efficiency, training, quality control, and code compliance.
Safety
Standardized safety practices are essential to maintaining safe working conditions for everyone. Many contractors simply rely on OSHA safety training; however, regulatory safety requirements only focus on the minimum safety protocol standards. According to Associated Builders and Contractors, a comprehensive onboarding process focused on a company’s specific safety culture, systems, and processes can lower incident rates by up to 45%, compared to companies that only cover basic compliance. These findings indicate that basic regulatory standards are insufficient on their own and should be supplemented with more proactive safety protocols.
One example of advanced safety practices can be found in the area of feeder and medium-voltage cable installations. Contractors can enhance worker protection and enhance their customers’ investment with a few simple changes.
Preplan cable pulls
Pulling devices and conductors have high allowable tension ratings; however, structural support limitations and maximum sidewall bearing pressure can often reduce the allowable tension on these pulls. Cable-pulling software can help contractors account for those tension limitations and plan accordingly. Though not required by regulation, software tools like this add a critical layer to worksite safety.
Use manufacturer-installed pulling heads
Most cables do not come with pulling heads attached, requiring workers to add them on site. This involves the use of a knife, which could result in injury. Another drawback is that the field-made wire head may not fit in the conduit or around a tight turn. In addition, approximately 3 feet of cable is wasted on every phase of an install. Using cut-to-length cables with manufacturer-installed pulling heads, contractors are assured that the cable will always fit, safety risks are minimized, and waste and cleanup labor are minimized.
Use low-friction pulling ropes and foot triggers
Low-friction ropes reduce the risk of snapping due to excessive force or friction, and using low-absorbency ropes helps prevent water absorption and rot. Implementing these safety standards across all projects ensures that crews are not operating with a false sense of security, enhancing overall job-site safety.
Efficiency
Consistent, standardized practices can also streamline workflows, leading to enhanced productivity and reduced downtime. Efficiencies are particularly beneficial due to the baby boomer retirement wave and the ongoing skilled labor shortage.
For example, by utilizing innovative packaging solutions from manufacturers that ease material handling, electrical contractors can reduce the physical effort normally needed to position larger reels for pulling or pulling smaller wires out of packaging. Adopting these packaging solutions would involve moving away from spools on circuit wiring and instead leveraging coils enclosed in a plastic shell. For larger gauge wires, contractors can procure exact lengths and configurations on an easily movable piece of reusable reel-like equipment, which aids in minimizing waste by reducing the amount of scrap reels.
Taking advantage of manufacturer engineering services is another best practice that can help ease labor shortage challenges. For example, these engineering services can be leveraged to speed installation with optimized wire color combinations and circuit labeling. They can also provide detailed, standardized drawings that help new crew members complete tasks quickly and accurately, ensuring projects stay on schedule. Standardization offers time and labor efficiencies that can be redeployed to other essential project tasks, and savings can be passed on to the customer.
Training
Standardized training procedures are yet another area where the industry can utilize best practices to improve knowledge and safety for its team members. Currently, many training programs are led by industry veterans, whose experience is invaluable; however, these programs may not include the latest technology and practices due to reliance on older methods and equipment. By standardizing training, companies can simplify and quicken the onboarding process for new team members, ensuring everyone quickly aligns with safety protocols and project expectations.
Standardized training programs help workers understand the differences in approach for specific scenarios. For example, every cable pulled through a conduit should be carefully calculated, but there is a significant amount of detail involved. A standardized approach to training ensures that all variables are considered while imparting knowledge of why certain steps are necessary. This ensures that all team members understand the “how” and “why” behind the protocols for each scenario. Instead of creating these training programs themselves, contractors should investigate the training programs offered through their suppliers, so they can focus their attention on their upcoming and ongoing projects.
Quality control and compliance
With everyone following consistent practices and utilizing standardized processes and equipment, collaborating contractors can ensure the margin for error is small and quality is never compromised on projects. For example, electricians sometimes risk damaging cables when using trucks or forklifts to pull them into place. When standardized practices require pre-planning the cable pulls with tension and sidewall calculations, contractors can be confident that cables have been installed correctly and will perform as expected. It also provides contractors and their clients with peace of mind, knowing that their investments are properly safeguarded and have been handled by professionals trained to the highest standards. By maintaining quality control, contractors can ensure the long-term reliability of installations, avoid costly repairs, and protect the project’s reputation.
Code compliance is an obvious requirement for every construction project and is essential to maintaining customer and employee trust as well as a positive reputation. A contractor’s success often depends on their ability to deliver projects on time and within budget. However, if Code compliance is overlooked or safety incidents occur because protocols are not followed, contractors can face liability issues, jeopardizing their business and reputation. By standardizing safety protocols and training, large projects that have multiple contractors on site can minimize the possibility of accidents and failed inspections, knowing they are all operating with the same knowledge to protect both lives and the success of the project.
Conclusion
Standardization within the construction industry should be considered more than just a best practice — it is a necessity. By creating consistent approaches in safety, efficiency, training, and quality control, contractors can streamline workflows, improve project outcomes, and protect their workforce. While some may fear that standardization could stifle job-site ingenuity that has in the past led to new methods and practices, the reality is that it enables innovation to thrive within a structured framework, where risks are minimized, and productivity is maximized. As the industry faces a skilled labor shortage and more complex projects, standardization will play a pivotal role, allowing contractors to continue to deliver high-quality projects even as they face both old and new challenges.
About the Author
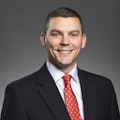
Jason Faircloth
Jason Faircloth is the director of Southwire Solutions. As the leader of Southwire’s Contractor Solutions Organization across the US, Jason and his team spend their time training contractors on the benefits of adopting the most recent technology to make their work more safe, more efficient, and ultimately, more profitable. After 12 years at Southwire with several years in each of their business segments, Jason has returned to his roots in the contractor world. Prior to joining Southwire, Jason spent 8 years owning and managing a specialty trade contracting company in Northeast Florida after receiving an engineering degree from the University of Georgia. When he is not working, he enjoys spending time with his wife and four sons.