Are you prepared to take responsibility for the consequences of not testing?
At a time when corporate accountants are scrutinizing a company's every expenditure, cost-cutting can go too far — and often does. Keeping an eye on the bottom line is important, but attempting to save a few dollars in one budget area only to cause more expensive problems down the road is counterproductive. Acceptance testing is one of the most recent casualties of this cost-cutting craze, but eliminating it can be more costly than you think.
When implemented properly, acceptance testing consists of four steps:
-
Factory acceptance testing — performed before equipment ships to work out design and manufacturing flaws.
-
Testing upon receipt — performed after delivery but before the equipment is signed for to ensure the shipment arrived intact.
-
Installation acceptance testing — performed immediately after installation to uncover installation errors.
-
Start-up testing (also called pre-op testing) — performed before full-time operation to “test drive” the equipment and work out operational bugs.
This battery of testing maximizes efficiency by ensuring everyone in the whole chain — from design to installation — builds systems with parts that work. This testing also establishes baseline data particular to the installation. From there, you can do predictive monitoring and preventive maintenance to maximize uptime while minimizing cost.
Engineers are recognizing the importance of acceptance testing, forcing the powers that be to give it some attention. But it comes with a price many companies don't want to pay. As a compromise, companies are increasingly employing a “test once” policy. As a result, this testing is on the decline and total cost of ownership is up.
According to Stuart Jackson, Instel Power Services, Greenville, S.C., if allowed to test equipment only once, most end-users would test two years after start-up. He says this choice is based on the increasingly prevalent misconception that testing is necessary only to check for imminent failure. Because they believe new equipment is unlikely to fail, some engineers think it's unnecessary to test new installations — but this ignores the possibility that something could happen during delivery and installation. Jackson thinks the initial stages of testing are the most valuable and should be the last ones cut if you're forced to choose.
With budgetary pressures increasing, can you save money by eliminating one or more stages of acceptance testing? Sure you can — temporarily. But the real question is, Which stage should you cut? Let's look at each of these stages in detail to help you make a more informed decision.
Factory acceptance testing.
Wouldn't it be nice if you could head off defective switchgear at the factory before it even ships? That's the idea behind factory acceptance testing (FAT). This form of testing usually applies to complete systems (such as process controls, switchgear, and production machinery), custom-designed products, and critical components or assemblies. The goal of FAT is to identify and solve problems at the factory, where the cost and time investment of doing so is much less than in the field. Most of the time, you can't take delivery until you are almost ready to install the system — and that's a bad time to find errors that require three weeks to resolve.
FAT allows an engineer representing the customer to ensure the system matches the design and that the factory corrects errors in construction, fabrication, component selection, assembly, and programming before shipment. Tests may include everything from point-to-point wiring checks to simulated operation. This differs from the manufacturer's normal quality-assurance process — with FAT, the customer has representatives put the system through its paces.
As an added bonus, the technician or engineer who participates in FAT gets factory training, becomes familiar with system operation, can ensure completion of system documentation, and often obtains free improvements or customizations.
Despite the advantages of FAT, customers are cutting back on it or eliminating it, citing manufacturer warranties as relieving them of all risk in the case of design or manufacturing errors. This mentality ignores many costs. The reality is that start-up of any major system is a team effort. Even with an individual contract, a manufacturer is rarely liable for lost production caused by start-up delays.
Testing upon receiving.
Even the best carriers occasionally damage equipment in transit — equipment can be damaged or lost during packing, loading, unloading, and unpacking. Testing upon receiving consists mostly of a visual inspection, and is often nothing more than a parts count. So the cost is usually negligible, but certain items require testing upon receipt.
In the case of a motor used in a critical process system, you should perform an insulation resistance check when it arrives — before you sign the shipping papers to accept the motor. You should also rotate the shaft to ensure it's not bent. A machinist, mechanic, or millwright can verify this with a dial indicator. If you don't already have a set of test procedures to implement upon receiving equipment, contact the manufacturer before a critical item ships and ask for recommendations. Then, assign a qualified person to test the equipment when it arrives.
Installation acceptance testing.
Installation errors are common, yet some managers refuse to budget for the testing that reveals such errors. This way of thinking ignores the fact that an error in an electrical system can result in catastrophic damage upon energization.
Installation acceptance testing typically involves point-to-point wiring and labeling checks that verify the wiring matches the prints and insulation resistance testing that verifies cable integrity. It also includes visual inspections that verify proper assembly, leveling, mounting, fit and finish, and conformance to applicable codes. It's common during this stage of testing to develop a punch-list of items that need correction. Some items on that list may delay start-up, while others delay final payment.
Finally, testing at this stage provides baseline data for later troubleshooting and predictive maintenance trending (Photo, on page 32). Thus, you'll often see something like “provide test data to owner” on the punch-list.
Start-up testing.
Start-up testing provides a “dry run” to ensure the equipment does its job. To prove a system is going to work, you must test it with the power on. Depending on the complexity of the installation, you may test one subsystem at a time.
For example, in a backup power installation, you should test the battery charging system, transfer switch, generator, and other major components and fix any errors. Then test these sub-systems as a unit by cutting off main power and witnessing that the system does, indeed, come online and provide an output. Test it under load to ensure it can maintain and sustain the load transfer.
While start-up testing might uncover some manufacturing or installation error, it's more likely you'll discover a weakness in the system design or a problem interacting with the other equipment in the plant. Think of start-up testing as a glorified test drive.
Reversing the decline.
You save time and money by testing after every major phase of construction, but with the current economic situation it can be difficult to convince decision-makers that acceptance testing has a high return on investment. The trend of reducing acceptance testing to cut costs is an exercise in false economy, and it can carry a heavy price. Acceptance testing didn't come about as a “make work” practice. Veterans do it because it works. Failure to perform acceptance testing sets the stage for disaster.
About the Author
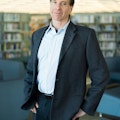
Mark Lamendola
Mark is an expert in maintenance management, having racked up an impressive track record during his time working in the field. He also has extensive knowledge of, and practical expertise with, the National Electrical Code (NEC). Through his consulting business, he provides articles and training materials on electrical topics, specializing in making difficult subjects easy to understand and focusing on the practical aspects of electrical work.
Prior to starting his own business, Mark served as the Technical Editor on EC&M for six years, worked three years in nuclear maintenance, six years as a contract project engineer/project manager, three years as a systems engineer, and three years in plant maintenance management.
Mark earned an AAS degree from Rock Valley College, a BSEET from Columbia Pacific University, and an MBA from Lake Erie College. He’s also completed several related certifications over the years and even was formerly licensed as a Master Electrician. He is a Senior Member of the IEEE and past Chairman of the Kansas City Chapters of both the IEEE and the IEEE Computer Society. Mark also served as the program director for, a board member of, and webmaster of, the Midwest Chapter of the 7x24 Exchange. He has also held memberships with the following organizations: NETA, NFPA, International Association of Webmasters, and Institute of Certified Professional Managers.