Article 511 provides the requirements for commercial garages — areas used for the storage or repair of self-propelled vehicles that use combustibles (liquid or gas) for power. Such vehicles include, but are not limited to, passenger automobiles, buses, trucks, and tractors. Shops and service or repair centers where these types of vehicles are serviced are most likely within the scope of Art. 511.
Article 511 makes a distinction between a parking garage and a commercial repair garage. Parking garages are simply those used for parking or storage, and they are permitted to be unclassified. The task of determining the classification for repair garages is not quite as simple — much of this classification hinges on whether the garage is considered to be a major or minor repair garage [511.2]:
- Major repair garage. A building (or portion of a building) where engine overhauls, painting, body and fender work, and repairs that require draining of the motor vehicle fuel tank are performed. These areas may include associated floor space used for offices, parking, or showrooms.
- Minor repair garage. A building (or portion of a building) used for lubrication, inspection, engine tune-ups, parts replacement, fluid changes (such as oil, antifreeze, transmission fluid, brake fluid, or air-conditioning refrigerants), brake system repairs, tire rotation, and similar routine maintenance work. These areas may include associated floor space used for offices, parking, or showrooms.
It’s important to note that in both of these definitions, “repair garages” may include associated floor space used for, and designated as, offices, parking areas, or showrooms. This is because an activity in a garage area can produce vapor accumulation that is not always limited to the repair garage area only, but can migrate to adjoining areas, resulting in possible hazardous conditions.
Accumulations and classifications
Article 511 is primarily concerned with the accumulation of combustible vapors and gases in two places:
- Pits. Flammable or combustible liquid-produced vapors can accumulate in any depression below floor grade. These are volatile vapors and gases that are heavier than air, sink to the lowest areas, and pool there. Dangerous concentrations of these vapors and gases can develop and need only a spark or source of ignition to ignite or explode.
- Ceiling areas. Volatile gases or vapors that are lighter than air rise into the elevated ceiling areas and accumulate there. Once again, these accumulations can be ignited easily by a spark or other source of ignition.
Different areas in the same building can be classified in different ways. In fact, not every area in a repair garage is a classified location. If you ensure that an area adjacent to a classified location meets certain ventilation requirements — or you can satisfy the AHJ that the area doesn’t present an ignition hazard — it’s possible for that area to be an unclassified location. This provides a way out of the “associated floor space” provision that was mentioned in the repair garage definitions.
Areas adjacent to classified locations aren’t classified if mechanically ventilated at a rate of four or more air changes per hour, or when walls or partitions effectively cut off the adjacent area [511.3(E)], as shown in Fig. 1.
It’s also possible for an entire building to be unclassified. Garages used just for parking or storage garages aren’t classified [511.3(A)]. The key here is the possibility of vapor accumulation. Exactly how those vapors might accumulate is the basis for the classification — and that depends largely on the nature of usage of the building.
Repair garages that dispense motor fuels must have the dispensing functions classified according to Table 514.3(B)(1). Article 514 provides the requirements for motor fuel dispensing facilities, so it’s appropriately brought into play in a repair garage where fuels are also dispensed.
Although the requirements of Art. 511 for major repair garages and minor repair garages have some similarities, they are distinctly different.
Major repair garages
Where gasoline or gaseous fuels (such as natural gas, hydrogen, or LPG) won’t be dispensed, the classification rules in (1), (2), and (3) apply.
(1) Floor areas.
- Ventilation provided. The floor area can be unclassified where there’s a minimum of four air changes per hour for each square foot of floor area [511.3(C)(1)(a)].
- Ventilation not provided. The entire floor area is classified as Class I, Div. 2 up to 18 in. above the floor [511.3(C)(1)(b)].
(2) Ceiling areas. Where vehicles fueled with lighter-than-air gaseous fuels are repaired or stored, the area within 18 in. of the ceiling is subject to classification. Natural gas and hydrogen are examples of lighter-than-air gaseous fuels. The type of ventilation is once again a key component in the classification of this area:
- Ventilation provided. The ceiling area is unclassified where ventilation is provided from not more than 18 in. from the highest point in the ceiling to exhaust the ceiling area at a rate of at least 1 cfm/sq ft at all times that the building is occupied — or whenever vehicles using lighter-than-air gaseous fuels are parked below this area.
- Ventilation not provided. The ceiling area is classified as Class I, Div. 2.
(3) Pit areas in lubrication or service room. The pit area in lubrication or service rooms of major repair garages is classified based on ventilation (Fig. 2):
- Ventilation provided. The pit area is classified as Class I, Div. 2 where there’s a minimum of six air changes per hour.
- Ventilation not provided. The pit area is classified as Class I, Div. 1 up to the floor level.
Minor repair garages
Where flammable liquids won’t be dispensed or transferred, the classification of (1), (2), and (3) apply.
(1) Floor areas. Floor areas are unclassified, but pit areas are classified based on the ventilation of the pit:
- Ventilation provided. The pit area can be unclassified where there’s a minimum of four air changes per hour.
- Ventilation not provided. The pit area is classified as Class I, Div. 2 up to the floor level.
(2) Ceiling areas. The ceiling area is unclassified where lighter-than-air gaseous fuels, such as natural gas or hydrogen, won’t be transferred.
(3) Pit areas in lubrication or service room. Pits, below-grade work areas, or subfloor work areas must be classified based on the ventilation provided:
a) Ventilation provided. The pit area is unclassified where ventilation is provided to exhaust the pit area at a rate of not less than 1 cfm/sq ft of the floor area at all times that the building is occupied or when vehicles are parked in or over this area. The exhaust air must be taken from a point within 12 in. of the floor of the pit.
b) Ventilation not provided. The pit area is classified as Class I, Div. 2 up to 18 in. above the floor level and extending out 3 ft from the edge of the pit.
Wiring and equipment
If you have a Class I location, install wiring and equipment per Art. 501 and wire fuel-dispensing units in accordance with Art. 514.
Portable lighting equipment provides a potential hazard simply because it’s portable and thus “could” be used in a hazardous location. The lamp and cord of portable lighting equipment must be supported or arranged in a manner so that it can’t be used in a hazardous location [511.3(B)]. Portable lighting equipment not so restrained must be identified for a Class I, Div. 1 location [501.130(B)].
Wiring installed above a Class I hazardous location must be in raceways, Types AC or MC cable, or manufactured wiring systems. Or, it is allowed in PLTC cable installed according to Art. 725 or TC cable installed according to Art. 336 [511.7(A)], as shown in Fig. 3.
If you install pendant cords above a Class I hazardous location, use only cords listed for hard usage in accordance with Table 400.4 [511.7(A)(2)].
Equipment with make-and-break contacts installed less than 12 ft above the floor level (excluding receptacles, lamps, and lampholders) must be of the totally enclosed type or be of the type constructed to prevent sparks or hot metal particles from escaping [511.7(B)(1)(a)].
If you install lampholders or lamps for fixed lighting over travel lanes or where exposed to physical damage, locate them at least 12 ft above floor level unless the luminaires are of the totally enclosed type or constructed to prevent sparks or hot metal particles from escaping [511.7(B)(1)(b)].
Install conduit, cable, and boundary seals per 501.15. Where the Class I, Div. 1 boundary is beneath the ground, you can install the sealing fitting after the conduit leaves the ground. However, there must not be any unions, couplings, boxes, or fittings (except explosionproof reducing bushings) between the sealing fitting and the point where the conduit leaves the earth [501.15(A)(4) Ex 2], as shown in Fig. 4.
If an area is classified in accordance with 511.3(B), don’t locate battery chargers and batteries being charged within the classified area [511.10].
GFCI protection is required for all 15A and 20A, 125V receptacles used for service and repair operations, such as electrical automotive diagnostic equipment, electric hand tools, and portable lighting devices [511.12].
Avoiding confusion
A potential source of confusion is that following the Art. 511 classification requirements provides different classifications for seemingly similar areas. It’s important to first distinguish between a “major repair” and “minor repair” garage before you apply the rules for classified locations. The next important factor is to evaluate the ventilation options; the use of proper ventilation will usually decrease the classification by one division or render the area unclassified.
The potential problem in repair garages is the accumulation of explosive or ignitable vapors and gases. The focus of Art. 511 is to prevent that accumulation when possible — and to prevent any possibility of it coming into contact with an ignition source in any case.
About the Author
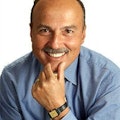
Mike Holt
Mike Holt is the owner of Mike Holt Enterprises (www.MikeHolt.com), one of the largest electrical publishers in the United States. He earned a master's degree in the Business Administration Program (MBA) from the University of Miami. He earned his reputation as a National Electrical Code (NEC) expert by working his way up through the electrical trade. Formally a construction editor for two different trade publications, Mike started his career as an apprentice electrician and eventually became a master electrician, an electrical inspector, a contractor, and an educator. Mike has taught more than 1,000 classes on 30 different electrical-related subjects — ranging from alarm installations to exam preparation and voltage drop calculations. He continues to produce seminars, videos, books, and online training for the trade as well as contribute monthly Code content to EC&M magazine.