Developing a Motor Strategy to Maximize Energy Savings
Motors constitute a large share of the load at a typical industrial facility. They drive mixers, blowers, conveyors, grinders, and other kinds of equipment. In most facilities, huge amounts of energy savings in motor systems go unrealized. Most of the measures that reduce energy waste also extend motor life and tend to improve uptime and reliability as well.
Doing one or two things to improve energy efficiency helps, but a comprehensive assessment and improvement strategy will maximize the savings. Have you considered all of the following?
• Upgrade to an energy-efficient motor. This (nearly always) makes sense, even if the existing motor is working fine. If you keep track of the cash flows and calculate the Internal Rate of Return, the savings are compelling. Also note that better components and better construction are the main ways a motor gets an “energy efficient” designation. That means increased reliability.
• Match the motor to the conditions and load. Design type, temperature rating, and other considerations can make a big difference in both how much energy a motor uses and how long it lasts in a given application.
• Use VFDs, not gearboxes, for speed reduction (where appropriate). Unless you need torque multiplication, avoid pairing motors with gearboxes. When selecting a VFD, choose one that is power factor corrected and harmonics corrected if it’s available for the application.
• Be fanatical about the supply power. Low power factor, excess harmonics, and voltage imbalance all make a motor draw more power to do the same work. Where possible, put single-phase loads on their own transformers; this will reduce voltage imbalance.
• Minimize voltage drop. Voltage drop means more current draw, which means more heat in the motor. Through a combination of larger conductors and locating transformers closer to their loads, you can reduce voltage drop dramatically.
• Cool it. Simple changes in air flow around motors can reduce their operating temperature, thus making them more efficient. Consider solutions that involve ducting or forced air.
• Align and monitor. When a motor isn’t aligned properly, we typically see the effect in the form of excess vibration. What is vibration, actually? It’s the use of supply energy to move the motor rather than the load. You want to get a perfect alignment, so use the proper tools (e.g., laser alignment system). And then monitor motor vibration, or at least add manual measurement to your PM system.
• Correct load-related issues. If a motor drives a gearbox that has lubrication deficiencies, more energy is required. Lubrication typically falls under the mechanical arm of the maintenance department, rather than the electrical arm. The problem is that the task is normally not performed properly (if at all). Generally, the gearbox should be slightly warmer than the ambient temperature. If your spot temperature gun or your thermographic camera shows more than a few degrees of difference, the plant engineer needs to know that the lubrication program probably is due for an overhaul. Else, the energy-wasting gearboxes will need overhauls when they eventually fail.
About the Author
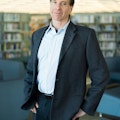
Mark Lamendola
Mark is an expert in maintenance management, having racked up an impressive track record during his time working in the field. He also has extensive knowledge of, and practical expertise with, the National Electrical Code (NEC). Through his consulting business, he provides articles and training materials on electrical topics, specializing in making difficult subjects easy to understand and focusing on the practical aspects of electrical work.
Prior to starting his own business, Mark served as the Technical Editor on EC&M for six years, worked three years in nuclear maintenance, six years as a contract project engineer/project manager, three years as a systems engineer, and three years in plant maintenance management.
Mark earned an AAS degree from Rock Valley College, a BSEET from Columbia Pacific University, and an MBA from Lake Erie College. He’s also completed several related certifications over the years and even was formerly licensed as a Master Electrician. He is a Senior Member of the IEEE and past Chairman of the Kansas City Chapters of both the IEEE and the IEEE Computer Society. Mark also served as the program director for, a board member of, and webmaster of, the Midwest Chapter of the 7x24 Exchange. He has also held memberships with the following organizations: NETA, NFPA, International Association of Webmasters, and Institute of Certified Professional Managers.