So-called cost-cutting is a constant threat to effective maintenance operations. And that’s especially frustrating in regard to test equipment.
Say you work in maintenance, and you notice the electrical testing firm that does your annual cable testing and switchgear maintenance always has the equipment needed to do the job efficiently. And it’s typically not very old.
You, on the other hand, often have problems obtaining the test equipment you need to take your equipment reliability to the next level. Or even keep it where it is.
You are certain the test equipment would have paid for itself several times over, based on the cost of downtime that you can see in your computerized maintenance management system (CMMS) reports. And you wonder what those executives have been smoking, every time they turn down your purchase request.
It’s not that they have been smoking anything. It’s that their perspective is different from yours.
Let’s say your purchase request poses hypothetical situations, with the costs of each if they happen at your plant. The executives look at those scenarios and yawn, because these don’t seem likely. After all, they have not happened yet, have they? And if not, what is the risk factor and what is the calculation of that risk factor based on?
One way to avoid that problem is to go back to your CMMS history and analyze specific downtime incidents. What is the failure mode for each, and what predictive maintenance tool(s) would have revealed a need for intervention?
For example, three motors failed because of a bearing failure. This resulted in a total cost to the company of $187,000 in unplanned downtime and repair costs. An ultrasonic test set would have enabled you to see the impending bearing failures long in advance (as in several months or more).
After some research, you found the ultrasonic test set that will best fit your needs. It’s about $1,600. That’s chump change compared with the $187,000 already lost, but you need hard data to prove to management that this is the solution. How do you get the data?
It will be much easier to get approval to lease this test set, mostly because the cost is so much less than for buying one and partly because equipment leasing and equipment buying are normally two different types of expenditure in the budget. You can use a lease to prove you need the ownership.
Before you lease the equipment, contact the manufacturer for a guide on how to use it. Probably, you can download the user manual from the manufacturrer's website. The instructions won’t make you an expert, but you at least won’t be wasting leased time trying to figure out how to use the thing and how to record the test data.
Once you’ve leased the test set, you want to go for proof of concept. So another bit of preparation you should do before actually leasing it is to make a list of which motors you will test in the limited time available.
Include motors that:
- Exhibit excess vibration.
- Have had bonding deficiencies (undesired current will flow through the bearings, burning them up).
- Are deemed critical, either because of their cost or the revenue loss that would result from failure of that motor.
- Are stopped and started the most.
If you understand the ultrasonic profiles produced using the test set, you can accurately predict that bearing failure is going to happen in certain motors. A real expert can tell you about when to expect that.
Your next step is to schedule corrective action. In this scenario, you want to photo-document everything. Say you have a critical 75 HP motor with damaged bearings. You know that a month from now, the line it drives will be down for a tooling change. You schedule your replacement for that downtime window.
After the replacement, send the old motor to a repair shop for complete analysis and repair. Ensure enough photos are taken to completely show the damage and, if possible even indicate its cause (for example, arc tracks). Get the damaged bearings back so you can take even more photos.
Now it’s just a matter of writing the purchase request for the test set you want and submitting the photo documentation, actual downtime cost accrued with early prevention, and estimated downtime cost had that prevention not happened.
You can apply this “lease it to prove my case” method to other kinds of test equipment; a power analyzer, for example. A cheap one isn’t good, and a good one isn’t cheap. But the cost of the tool pales beside the savings you can generate from using it (as is typically the case with test equipment).
Now, there is an exception. Some kinds of test equipment require specialized training. How do you get the training if you can barely get management to pay for the equipment?
You can contract out a project to someone who is certified on that equipment. For example, you are constantly dealing with high-impedance connection issues throughout the plant.
It’s unlikely someone without training will effectively use a thermographic camera in the high emissivity environment of the typical electrical panel. A Level II thermographer has the training to overcome the issues encountered.
Let’s say you have that same electrical testing firm mentioned earlier. They already do thermographic analysis of your switchgear, as part of their maintenance plan for it. As proof of concept, you have them perform thermographic analysis in places where you’ve been experiencing those connection problems. Then use the results to bolster your case for the training. And if you don’t think that evidence is compelling enough, get thermographic analysis on your motors (that should do it).
The “trick” to obtaining test equipment in a “No, you can’t have it” environment is to show management graphically and numerically what they are already spending as an alternative. Prove the concept with real data, and your chances for purchase approval go from dismal to near certainty.
About the Author
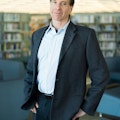
Mark Lamendola
Mark is an expert in maintenance management, having racked up an impressive track record during his time working in the field. He also has extensive knowledge of, and practical expertise with, the National Electrical Code (NEC). Through his consulting business, he provides articles and training materials on electrical topics, specializing in making difficult subjects easy to understand and focusing on the practical aspects of electrical work.
Prior to starting his own business, Mark served as the Technical Editor on EC&M for six years, worked three years in nuclear maintenance, six years as a contract project engineer/project manager, three years as a systems engineer, and three years in plant maintenance management.
Mark earned an AAS degree from Rock Valley College, a BSEET from Columbia Pacific University, and an MBA from Lake Erie College. He’s also completed several related certifications over the years and even was formerly licensed as a Master Electrician. He is a Senior Member of the IEEE and past Chairman of the Kansas City Chapters of both the IEEE and the IEEE Computer Society. Mark also served as the program director for, a board member of, and webmaster of, the Midwest Chapter of the 7x24 Exchange. He has also held memberships with the following organizations: NETA, NFPA, International Association of Webmasters, and Institute of Certified Professional Managers.