Industrial motors are responsible for a major chunk of the energy usage in industry, and in the nation as a whole. Yet more often than not, motor installations waste energy because they lack the simple modifications that can make them more energy-efficient.
Obviously, you can improve this situation by specifying energy-efficient motors as replacements or as the choice for the original installation. But the motor system as a whole may still be energy-inefficient. Let’s look at a few ways to solve that problem.
- Power factor. Most facilities have power factor correction capacitors at the service, not to actually improve power factor but to avoid the utility’s power factor penalty. Putting the capacitors here will do nothing for low power factor at the load. A motor, being an inductive load, will shift power factor one direction; a corrective capacitor at the motor will shift it in the other. A capacitor sized to offset the motor’s inductance can put power factor at unity. This means the motor will use less electricity to do the same amount of work.
- Load matching. Often, a motor is oversized to meet maximum load conditions. During normal conditions, that big motor is using more electricity than needed. Let’s say the motor turns an impeller in a hydraulic system. To prevent overpressurization, the system has a bypass valve to shunt some of the impeller’s output out of the system. This is, essentially, wasted motor usage. One way to solve this is with a variable speed drive. If you specify a drive that is also power-factor-corrected, you kill two birds with one stone. You can kill three power-wasting birds if you specify a drive that’s also harmonics-corrected.
- Excess heat. Motors run less efficiently when hot. To accurately prioritize which motors need heat remediation, conduct a thermographic analysis of each motor system. You want to look for high ambient temperature directly around the motor relative to the ambient temperature of the room. Or if a room is small, how hot is it compared with the larger area of the building it’s in (vent the room, if need be). The motors that have too much heat can be ducted with a supply of cooling air; if you put the fan on a controller that can vary fan speed based on the actual temperature, you’ll optimize this arrangement.
- Voltage imbalance. For three-phase motors, periodically check for voltage imbalance. This is one cause of the heat just discussed. Ducting is not recommended to address heat caused by voltage imbalance—correcting the imbalance is. The actual calculation involves several steps. As a rule of thumb you want to keep this below 2% to reduce the amount of excess heat in the motor.
- Gearbox problems. Gearboxes can easily be neglected. They may be left out of the mechanical maintenance program because they are part of the motor system and therefore electrical, and left out of the electrical program because they are obviously mechanical systems. Your first line of defense is to make them someone’s responsibility. Someone needs to conduct thermal imaging on them periodically (hot gearboxes mean wasted energy and possibly reduced motor life), and someone needs to maintain the lubricant inside them. The imaging and lubrication duties can be split, but they should not be shared (if they are shared, then the assumption is “the other guys will get this,” and that won’t happen). Vibration testing also should be done at the gearbox, not just at the motor.
About the Author
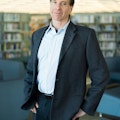
Mark Lamendola
Mark is an expert in maintenance management, having racked up an impressive track record during his time working in the field. He also has extensive knowledge of, and practical expertise with, the National Electrical Code (NEC). Through his consulting business, he provides articles and training materials on electrical topics, specializing in making difficult subjects easy to understand and focusing on the practical aspects of electrical work.
Prior to starting his own business, Mark served as the Technical Editor on EC&M for six years, worked three years in nuclear maintenance, six years as a contract project engineer/project manager, three years as a systems engineer, and three years in plant maintenance management.
Mark earned an AAS degree from Rock Valley College, a BSEET from Columbia Pacific University, and an MBA from Lake Erie College. He’s also completed several related certifications over the years and even was formerly licensed as a Master Electrician. He is a Senior Member of the IEEE and past Chairman of the Kansas City Chapters of both the IEEE and the IEEE Computer Society. Mark also served as the program director for, a board member of, and webmaster of, the Midwest Chapter of the 7x24 Exchange. He has also held memberships with the following organizations: NETA, NFPA, International Association of Webmasters, and Institute of Certified Professional Managers.