Looking for power quality issues typically is not done until such issues are suspected in a troubleshooting situation. If an area of the plant has power quality problems, but the equipment failure rates don’t seem unusually high, a typical maintenance department won’t even look at power quality.
Yes, equipment malfunctions should draw attention to power quality. Motor failures, in particular, may be caused by power quality problems. But the threshold at which power quality problems should be addressed isn’t when equipment fails. It’s when the cost of powering that equipment is considerably more than it should be. And the only way to know when that occurs is to perform a power quality analysis.
What “poor power quality” means in practical terms is that the usability of the power is diminished, so the equipment requires more power to do the same work.
Maybe someone used a harmonic analyzer and found that your total harmonic distortion (THD) falls within the range of what one standard or another shows is acceptable. What that standard isn’t going to tell you is that 300 pieces of equipment running on that “acceptable” power are all wasting energy. And it adds up.
To reduce the waste, look for the load (or a few loads) that most contribute to harmonic distortion on a particular feeder — the big switching power supply in that control cabinet, for example. Many harmonics mitigation techniques exist, so figure out the one best suited to the specific application. It might be as simple as installing a tank circuit or harmonics filter.
One easy fix if the source is an electronic motor drive is to replace that drive with one that is harmonics-corrected. Chances are good that it will also be power factor-corrected, rendering that inductive load neutral in terms of power factor. This is a productive area for energy savings, because low power factor at the load is often rampant in a given facility and typically the only power factor correction in the plant is at the service.
Power factor correction at the service enables you to avoid the utility’s low power factor penalty. But it doesn’t do anything for low power factor at large inductive loads. The uncorrected low power factor at these loads means each one will just draw more power to do the same work.
Severe power quality problems may contribute to, or cause, equipment failures. But that doesn’t mean you should consider power quality problems only when they are severe. Even seemingly minor power quality problems may cost plenty of money because all of the equipment on the affected feeder(s) will require more power and the losses multiply...every day, all year long.
About the Author
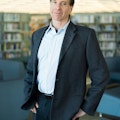
Mark Lamendola
Mark is an expert in maintenance management, having racked up an impressive track record during his time working in the field. He also has extensive knowledge of, and practical expertise with, the National Electrical Code (NEC). Through his consulting business, he provides articles and training materials on electrical topics, specializing in making difficult subjects easy to understand and focusing on the practical aspects of electrical work.
Prior to starting his own business, Mark served as the Technical Editor on EC&M for six years, worked three years in nuclear maintenance, six years as a contract project engineer/project manager, three years as a systems engineer, and three years in plant maintenance management.
Mark earned an AAS degree from Rock Valley College, a BSEET from Columbia Pacific University, and an MBA from Lake Erie College. He’s also completed several related certifications over the years and even was formerly licensed as a Master Electrician. He is a Senior Member of the IEEE and past Chairman of the Kansas City Chapters of both the IEEE and the IEEE Computer Society. Mark also served as the program director for, a board member of, and webmaster of, the Midwest Chapter of the 7x24 Exchange. He has also held memberships with the following organizations: NETA, NFPA, International Association of Webmasters, and Institute of Certified Professional Managers.