Energy savings is often thought of as something extra you do, after the fact, to reduce thermal losses. For example, you add insulation. But you can build in energy savings just by making different choices throughout a project. A great example of this is saving energy with power distribution feeders in a facility.
By default, we tend to design energy inefficiencies into our electrical infrastructure. This isn’t because we are deliberately trying to waste energy. It’s because we aren’t deliberately trying to save it.
For offices and general receptacles, you need 120V, so stepdown transformers supply 208/120V. Sometimes, this is just one big transformer and one big panel. While that arrangement saves the design engineer time, it typically increases the cost of construction and definitely increases the cost of operation.
Ideally, you will distribute 480V as far inside the building as you can — so far that all feeders are 480V and only branch circuits are at a lower voltage. First of all, it costs less in labor and materials to carry that same power at 480V than at 120V (smaller wire due to lower current, smaller raceway due to smaller wire, etc.). More important, the distribution itself is more efficient at 480V. The closer the 120V transformer is to its 120V loads, the more energy-efficient your system will be. Thus, it’s smart to:
- Use several small, strategically situated 480V-120/208V transformers instead of one large, centrally situated one. The idea here is to get the shortest 208/120V branch circuits that are practical.
- Use a similar approach for 277V. Rather than a center tap off the service transformer, use several smaller 480V-480/277V transformers. Better yet, see if you can replace 277V with 480V, since the typical uses (lighting and reheat boxes) are available in 480V versions.
Yes, there’s additional engineering cost involved with this route, but the construction savings alone may pay for it. Consider that you’ll run smaller conductors in smaller raceways. You’ll recover costs in other areas, also. The real payoff, however, is in the energy savings. These savings will continue over the life of this infrastructure.
However, the savings can be vaporized by errors in construction. To prevent that, perform AC resistance testing across feeder connections prior to energizing the system. Then ensure that all connections are subject to periodic thermographic inspection so that high resistance connections can be disassembled and replaced with new hardware. Remember, simply tightening a “loose” connection (one indicated as hot by the thermographic inspection) can actually make matters worse. If it’s a bad connection, replace it with a good one.
About the Author
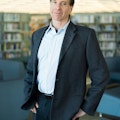
Mark Lamendola
Mark is an expert in maintenance management, having racked up an impressive track record during his time working in the field. He also has extensive knowledge of, and practical expertise with, the National Electrical Code (NEC). Through his consulting business, he provides articles and training materials on electrical topics, specializing in making difficult subjects easy to understand and focusing on the practical aspects of electrical work.
Prior to starting his own business, Mark served as the Technical Editor on EC&M for six years, worked three years in nuclear maintenance, six years as a contract project engineer/project manager, three years as a systems engineer, and three years in plant maintenance management.
Mark earned an AAS degree from Rock Valley College, a BSEET from Columbia Pacific University, and an MBA from Lake Erie College. He’s also completed several related certifications over the years and even was formerly licensed as a Master Electrician. He is a Senior Member of the IEEE and past Chairman of the Kansas City Chapters of both the IEEE and the IEEE Computer Society. Mark also served as the program director for, a board member of, and webmaster of, the Midwest Chapter of the 7x24 Exchange. He has also held memberships with the following organizations: NETA, NFPA, International Association of Webmasters, and Institute of Certified Professional Managers.