Tip of the Week: Have you customized your PM procedures?
A large manufacturing facility decided to hire a maintenance consultant because it just could not get any traction in reducing equipment failures.
The first thing the maintenance consultant did was look at a representative sample of the Preventive Maintenance (PM) procedures. They seemed fine. He then went through the maintenance schedule with the maintenance department’s scheduling person. Again, everything seemed fine.
His next step was to review a representative sample of the repair logs, but they didn’t really tell him anything. The documentation was skimpy, to say the least. There were no As Found photos and no As Left photos. There was no mention anywhere of root cause analysis. He asked the scheduling person, who also maintained these logs, where that information was. Maintenance personnel didn’t collect that information.
The consultant then discussed his findings (and lack thereof) with the plant engineer and concluded with the question: “How do you determine which PM activities to do and when to do them?”
The plant engineer said the procedures all followed the manufacturer’s recommendations. “No sense reinventing the wheel,” he said.
But it’s not reinventing the wheel. It’s making sure you have a steering wheel. In this case, there was no feedback from the repairs to modify the PMs for the actual failure causes. Because these causes were not addressed, the failures continued.
In another plant, four different drive motors on a long, complicated line blew their overloads in the same week. In each case, the whole line stopped. Obviously, the manufacturer-recommended PMs weren’t doing the trick anymore. Something had changed, and an engineer was tasked to determine what that was. He began by monitoring the current draw on several motors.
The problem turned out to be a drift in a particular set of mechanical adjustments. It increased the load on certain motors, and with enough variance from that (and from production itself) a motor could get overloaded. This problem happened twice more during the investigation phase, but never again after that because the mechanical arm of the maintenance department added another task to its PMs. You can easily guess what that task was.
Maintain based on your actual conditions and usage, not on some “typical” application assumed by manufacturers whose recommendations are really a starting point.
About the Author
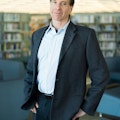
Mark Lamendola
Mark is an expert in maintenance management, having racked up an impressive track record during his time working in the field. He also has extensive knowledge of, and practical expertise with, the National Electrical Code (NEC). Through his consulting business, he provides articles and training materials on electrical topics, specializing in making difficult subjects easy to understand and focusing on the practical aspects of electrical work.
Prior to starting his own business, Mark served as the Technical Editor on EC&M for six years, worked three years in nuclear maintenance, six years as a contract project engineer/project manager, three years as a systems engineer, and three years in plant maintenance management.
Mark earned an AAS degree from Rock Valley College, a BSEET from Columbia Pacific University, and an MBA from Lake Erie College. He’s also completed several related certifications over the years and even was formerly licensed as a Master Electrician. He is a Senior Member of the IEEE and past Chairman of the Kansas City Chapters of both the IEEE and the IEEE Computer Society. Mark also served as the program director for, a board member of, and webmaster of, the Midwest Chapter of the 7x24 Exchange. He has also held memberships with the following organizations: NETA, NFPA, International Association of Webmasters, and Institute of Certified Professional Managers.