Tip of the Week: Identify and Articulate Your Training Needs
In many companies, training plans aren't based on actual needs. Maybe a manager reads a brochure and thinks: “Hey, that sounds important. I think I’ll send somebody.”
Or maybe a lubrication technician out in the plant mixes incompatible greases every few months and destroys some production equipment. Nobody at the plant understands that “lubrication technician” is really a senior, not junior, position. Everybody at the plant gets upset with the electricians for taking so long to change the motors. They don’t know that those motors would not have failed if the person lubricating them actually had a clue about how to do that job correctly.
The list of “or maybe” scenarios could go on and on. What does this mean for you? It means you need to be sensitive to the many clues that you may need training, such as:
• You don’t have a clear idea of how to approach the work when you start it. This means you don’t know what you’re doing and you plan to figure it out as you go. This is a great way to make big mistakes.
• You do know how to turn on a piece of test equipment and take basic measurements with it, but that’s all. The iconic example of this situation is the untrained thermographer.
• You encounter problems and frustrations while doing what seemed like a straightforward task. Any time you feel reminded of the joke about the carpenter who said, “I cut it twice and it’s still too short,” you need training.
So you may be able to identify training needs, but how do you ask for training without making it look as if you’re incompetent? As noted earlier, a maintenance technician may fear letting his boss know that he doesn't know his job 100 percent. But that very fear is keeping him from moving toward 100 percent.
The key is in how you frame the request. You want to show the company not that you have a deficiency but that your improved proficiency may save them money. And if you take the initiative, you will probably rack up more than just a few attaboys.
Here’s one method that works.
First, find some new insight into the task you want training on. Think about it, ask coworkers, go online—whatever you can do to come up with one good improvement.
Show your supervisor how you performed the task previously. Then show your supervisor how you perform it now. How much is that improvement worth? Put a dollar figure on it.
Then find a source of training. When you submit your training request, you can show that something you discovered on your own now saves the company $500 a year. The training course you recommend costs $1,200, and if you could save $500 a year just on your own, it makes sense that training provided by experts could save much more and quickly pay for itself.
About the Author
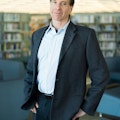
Mark Lamendola
Mark is an expert in maintenance management, having racked up an impressive track record during his time working in the field. He also has extensive knowledge of, and practical expertise with, the National Electrical Code (NEC). Through his consulting business, he provides articles and training materials on electrical topics, specializing in making difficult subjects easy to understand and focusing on the practical aspects of electrical work.
Prior to starting his own business, Mark served as the Technical Editor on EC&M for six years, worked three years in nuclear maintenance, six years as a contract project engineer/project manager, three years as a systems engineer, and three years in plant maintenance management.
Mark earned an AAS degree from Rock Valley College, a BSEET from Columbia Pacific University, and an MBA from Lake Erie College. He’s also completed several related certifications over the years and even was formerly licensed as a Master Electrician. He is a Senior Member of the IEEE and past Chairman of the Kansas City Chapters of both the IEEE and the IEEE Computer Society. Mark also served as the program director for, a board member of, and webmaster of, the Midwest Chapter of the 7x24 Exchange. He has also held memberships with the following organizations: NETA, NFPA, International Association of Webmasters, and Institute of Certified Professional Managers.