Electrical Troubleshooting Quiz — Feb. 1, 2022
In 2020, the administrative office building of your manufacturing plant underwent a lighting upgrade. It’s a free-standing, one-story building with its own electrical service (120/240V). It had been shut down during the federally mandated shutdown related to COVID-19. The facilities manager took advantage of this window of non-occupation to upgrade the troffer lighting from fluorescent to LED.
It seemed fine until a few months ago. Since then, several of the office workers have complained about the lights being too dim. The facilities manager has a light meter left over from the upgrade, and after taking readings, she agrees with the complaints.
She also said the office manager told her some of the light switches sometimes make a “sparky sound” when operated. Everything else in the office seems to work right, including the all-important coffee pot.
You’ve been tasked with diagnosing this problem and providing the solution. What issues should you look at?
Check lighting equipment
Start with something easy; take voltage measurements on the supply breakers. It is unlikely you will find a problem here, but when a system is malfunctioning, you nearly always check the power supply first. If the voltage checks out, note the location of those breakers. You may need to come back to them.
The switches should be considered part of the power supply to the lights. Take a look at them. It is entirely possible they are dimmer switches. Look on one side of the toggle for a slider. Move this up a bit, and you probably have solved the low light problem.
What about the arcing at the switches? Identify which switches made the sound and replace them. Switches go bad, eventually. If they have a dimming function, replace them with LED-compatible dimming switches. Using a dimming switch that isn’t compatible with LED will often present no problems at first. Then over a few months, damage accumulates and you hear arcing plus the light may be dimmer.
Next, ascertain what exactly the upgrade consisted of:
- New complete LED troffers that replace the old lighting fixtures, ballasts, lenses, and lamps— everything from the branch circuit conductors forward.
- Fixture upgrades that replace the ballast with an LED supply; LED lamps are then mounted in the same fixture.
- Replacement of the fluorescent lamps with LED lamps that run from the same ballast supply and have an LED power supply integral to the lamp.
If the upgrade is one of the first two options, the LED power supply should be fine. It should not degrade over so little time. That is not the case with the third option.
With the third option, cramming so much into that tiny package involves engineering compromises such that even high-quality versions are less durable than either of the other two options. Short cycling and excess heat can add to early demise. Even so, this would not explain these symptoms so early on in the life cycle if the lamps are any of the major brands.
Perhaps they are not. Perhaps someone thought to save money by selecting inexpensive ones with a much lower-than-expected lifespan due to poor design or poor packaging of the integrated LED power supply. If you don’t recognize the brand, that’s almost certainly the problem.
You can try replacement lamps in one fixture and see if the light output improves. If it does, your facilities manager must choose one of these options:
- Keep replacing cheap integrated lamps.
- Replace cheap integrated lamps with quality ones.
- Use a solution that doesn’t involve an integrated lamp (e.g., replace the whole troffer system or just the ballast forward).
While you’re in there, look at the lens. If it appears dirty or dingy, clean or replace and check the lighting. Why not check the lighting with the lens removed and compare it to a reading with the lens installed? Because the lens is designed to diffuse the light; you need to see what the light output is with the lens in place just as it will be in place during normal operation.
Power quality
If the lighting equipment itself checks out and the low lighting remains, the next step is to check the branch circuit power for low power factor, excess harmonics, and waveform distortion. You will need a hand-held power analyzer to check for these and other power quality problems. The fact that the other equipment, including the coffee pot, all works fine doesn’t mean you can rule out power quality problems. LED power supplies are sensitive to problems that may show no effect on other equipment.
Determine from the manufacturer what numbers you need to see in terms of power quality. But wait, if these worked fine for so long, why would power quality now be an issue? Load changes happen in offices all the time. Printers, copiers, network devices, computer workstations, and other equipment can change the power quality profile. And if enough people are charging their smartphones, tablets, headsets, and other devices, all those little USB power supplies can add up to a “tipping point” problem. They could push an aspect or two of the power quality from acceptable to detrimental.
Once you identify power quality problems, you’ll need to determine which loads are contributing the most or which loads have changed since installation. For example, the copier your company leases was replaced with a newer model. Try running it with a power analyzer on the branch circuit and see what happens.
What if managing loads to fix this annoys everyone? One solution would be to set a new transformer and panel just for the lighting branch circuits.
About the Author
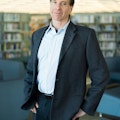
Mark Lamendola
Mark is an expert in maintenance management, having racked up an impressive track record during his time working in the field. He also has extensive knowledge of, and practical expertise with, the National Electrical Code (NEC). Through his consulting business, he provides articles and training materials on electrical topics, specializing in making difficult subjects easy to understand and focusing on the practical aspects of electrical work.
Prior to starting his own business, Mark served as the Technical Editor on EC&M for six years, worked three years in nuclear maintenance, six years as a contract project engineer/project manager, three years as a systems engineer, and three years in plant maintenance management.
Mark earned an AAS degree from Rock Valley College, a BSEET from Columbia Pacific University, and an MBA from Lake Erie College. He’s also completed several related certifications over the years and even was formerly licensed as a Master Electrician. He is a Senior Member of the IEEE and past Chairman of the Kansas City Chapters of both the IEEE and the IEEE Computer Society. Mark also served as the program director for, a board member of, and webmaster of, the Midwest Chapter of the 7x24 Exchange. He has also held memberships with the following organizations: NETA, NFPA, International Association of Webmasters, and Institute of Certified Professional Managers.