While maintenance strives to reduce risk by preventing failures, the typical focus of a repair is to restore normal operation. Unscheduled repairs make this focus necessary. When production is interrupted, that down time is usually not a good time to review the design of the equipment. Operators may be standing around with no other tasks assigned, and shipments might be late.
Scheduled repairs are a different story. Using predictive maintenance tools, we can often see an equipment condition that will lead to failure if intervention is not made. Suppose ultrasonic testing reveals that the bearings of a critical motor will fail in the next six to nine months. You now have the luxury of ordering a spare and arranging with a motor shop to repair this one. But why are those bearings damaged?
There’s significant cost involved in this repair. The risk management part of the maintenance function requires taking steps to prevent a recurrence. In this case, you’d make a list of all possible contributors to bearing failure (e.g., incorrect lubrication, improper bonding, load issues, etc.) and investigate for each one of them.
About the Author
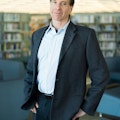
Mark Lamendola
Mark is an expert in maintenance management, having racked up an impressive track record during his time working in the field. He also has extensive knowledge of, and practical expertise with, the National Electrical Code (NEC). Through his consulting business, he provides articles and training materials on electrical topics, specializing in making difficult subjects easy to understand and focusing on the practical aspects of electrical work.
Prior to starting his own business, Mark served as the Technical Editor on EC&M for six years, worked three years in nuclear maintenance, six years as a contract project engineer/project manager, three years as a systems engineer, and three years in plant maintenance management.
Mark earned an AAS degree from Rock Valley College, a BSEET from Columbia Pacific University, and an MBA from Lake Erie College. He’s also completed several related certifications over the years and even was formerly licensed as a Master Electrician. He is a Senior Member of the IEEE and past Chairman of the Kansas City Chapters of both the IEEE and the IEEE Computer Society. Mark also served as the program director for, a board member of, and webmaster of, the Midwest Chapter of the 7x24 Exchange. He has also held memberships with the following organizations: NETA, NFPA, International Association of Webmasters, and Institute of Certified Professional Managers.