Your plant has several custom-built production machines that use various plug-in circuit boards. The standard practice has been to troubleshoot to the board level and then replace the entire board.
Corporate management sent a consultant to your plant to look for ways to reduce costs. One of his recommendations was to have maintenance replace the failed component on a board rather than replace the whole board. His math showed a cost-savings of 83%.
Sounds like a no-brainer until you look more closely:
1. Probably something in your power distribution system zapped that component. The other components were also stressed. The “repaired” board almost certainly has a much higher risk of failure than a new one.
2. Sending the electricians to electronics training so they can properly solder on a two-sided PCB and operate the requisite bench equipment is not a trivial expense. Neither is the requisite bench equipment.
3. If you have spare boards in inventory, replacement is quick. Repairing a board while the machine is down doesn’t make economic sense; perhaps repairing the damaged one after replacing it with a spare does, but see the previous two points.
About the Author
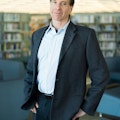
Mark Lamendola
Mark is an expert in maintenance management, having racked up an impressive track record during his time working in the field. He also has extensive knowledge of, and practical expertise with, the National Electrical Code (NEC). Through his consulting business, he provides articles and training materials on electrical topics, specializing in making difficult subjects easy to understand and focusing on the practical aspects of electrical work.
Prior to starting his own business, Mark served as the Technical Editor on EC&M for six years, worked three years in nuclear maintenance, six years as a contract project engineer/project manager, three years as a systems engineer, and three years in plant maintenance management.
Mark earned an AAS degree from Rock Valley College, a BSEET from Columbia Pacific University, and an MBA from Lake Erie College. He’s also completed several related certifications over the years and even was formerly licensed as a Master Electrician. He is a Senior Member of the IEEE and past Chairman of the Kansas City Chapters of both the IEEE and the IEEE Computer Society. Mark also served as the program director for, a board member of, and webmaster of, the Midwest Chapter of the 7x24 Exchange. He has also held memberships with the following organizations: NETA, NFPA, International Association of Webmasters, and Institute of Certified Professional Managers.