Prioritizing Maintenance and Repairs
Are you putting out so many fires that you can’t keep up with the PM work and maintenance is being blamed for production shortfalls? If so, your situation is fairly typical. It’s called chasing your own tail. The problem is that, no matter how fast you run, you will never catch it.
If you slow down to do the PM work, the payoff in reduced failures may take months to materialize. In the interim, your perceived performance is even worse. What can you do?
In a typical mid-sized or larger plant, there is one production line, machine, or process that makes more money than anything else in the plant. When that money-maker line goes down, the repercussions to the plant are more serious than when the line with the lowest revenue goes down.
If your plant has several production lines, you need to rank each one by its revenue-making capabilities. You can probably get the information from the production department, so start by asking there. To avoid getting bogged down in a big data collection project, identify only the top three for now.
For the top revenue-making line, focus whatever resources you need to keep it running perfectly. Take resources from anything not in the top three. Do all the PM, PdM, training, upgrades, spare parts assessment, repair kit assembly, procedure refinement, automatic monitoring, and root cause analysis needed to eliminate unscheduled shutdowns of this one line.
Be methodical and painfully thorough. If your root cause analysis revealed something systemic such as low power factor, voltage imbalance, or excess triplen harmonics, a fix there will reduce problems with equipment elsewhere and probably everywhere.
Once you begin to see significant improvement with the top money-maker line, some of your resources will free up. Using those resources and the lessons you learned on the top line, knock out some easy wins on the next two top lines. For example, if you learned that motor soft foot was causing issues on the top money-maker, then you can create work orders to identify and correct this on the other two.
Once you determine that the top line is no longer being hit with excessive failures, allocate adequate resources to keep it that way. PM and PdM here are never deferred. The line rolls off your high attention list because it’s taken care of. Turn your main focus onto the No. 2 revenue-producer. When it no longer suffers from excessive downtime, do the resource allocation thing again. Repeat for the third revenue-producer.
What the plant controller, plant manager, and upstream management will see is increasing revenue from this plant. Anyone else’s criticism isn’t going to matter much because the plant exists to produce revenue. It’s why you didn’t start with just any line or machine, but with the top revenue-makers.
With the top three in good shape, identify the next three and repeat this whole process. Then the next three and so on. When a resource conflict arises, go back to your revenue ranking to determine the winner. Always let the responsible production managers know this is the metric you used. If production tells you that, in this case, they want an exception due to a specific reason, such as this way a delivery won’t be missed but your way it will, be flexible.
With the chase-your-tail approach, everybody loses. With the revenue-ranking approach, you get winners and you get losers. To avoid having sore losers, communicate to everyone how you are prioritizing maintenance and repairs.
About the Author
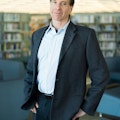
Mark Lamendola
Mark is an expert in maintenance management, having racked up an impressive track record during his time working in the field. He also has extensive knowledge of, and practical expertise with, the National Electrical Code (NEC). Through his consulting business, he provides articles and training materials on electrical topics, specializing in making difficult subjects easy to understand and focusing on the practical aspects of electrical work.
Prior to starting his own business, Mark served as the Technical Editor on EC&M for six years, worked three years in nuclear maintenance, six years as a contract project engineer/project manager, three years as a systems engineer, and three years in plant maintenance management.
Mark earned an AAS degree from Rock Valley College, a BSEET from Columbia Pacific University, and an MBA from Lake Erie College. He’s also completed several related certifications over the years and even was formerly licensed as a Master Electrician. He is a Senior Member of the IEEE and past Chairman of the Kansas City Chapters of both the IEEE and the IEEE Computer Society. Mark also served as the program director for, a board member of, and webmaster of, the Midwest Chapter of the 7x24 Exchange. He has also held memberships with the following organizations: NETA, NFPA, International Association of Webmasters, and Institute of Certified Professional Managers.