Measuring Maintenance Performance
How do you measure the performance of the maintenance department? Here are some commonly used metrics:
- Decrease in total downtime. This metric can be manipulated by quick fixes and incorrect focus. It does not have a value component, so focusing on this metric is a dangerous approach.
- Response time. This metric can be manipulated by having a quick but unhelpful response system. This metric has value when it is applied to critical equipment and when “response” is defined as more than a quick drive-through.
- PM backlog. Some experts consider this metric good if there is a small backlog of uncompleted PMs. But if there is a backlog, then maintenance has put urgent things in front of important things. That’s how you get a snowball effect.
- Total PMs completed in X period. The theory is that it’s good when this number goes up, but what does that mean? That maintenance has become busier doing unnecessary or unproductive PMs? Or that the work planners have broken a few PMs into smaller ones?
- Workforce utilization. The normal way this is viewed is 100% utilization is good, and anything lower means you have room for improvement. However, what if the maintenance were done so expertly that unscheduled downtime was zero and with such skill that the workforce was used at only 50%? You have an ideal outcome but the metric looks bad. Now, that is an extreme case but it illustrates something about using this metric. The goal isn’t to keep people busy but to keep equipment working properly.
- Share of total downtime attributable to maintenance. This is purely a political metric that shifts the focus from solving problems to allocating blame for them. Instead of playing this game, Maintenance should take ownership of downtime problems and work with other departments to solve them if those other departments are involved.
- Average repair time. Using this metric leads to fast, incomplete repairs that reduce equipment availability.
- Total training hours. Like some other metrics on this list, this is an example of an aggregate that does not have any relation to the major goal of maintenance or the value provided by maintenance. While it appears to be a useful metric, it just leads you down the wrong path.
Critical equipment
If these metrics have such drawbacks, should you use any metrics? Yes, because that which you cannot measure you cannot improve. However, instead of starting at the input end or the middle, start at the end and work your way backward. Start with answering the question of which equipment is critical equipment. In general, the answer will look like this and in this order of importance:
- Equipment that is necessary for human safety. Example: Fire protection equipment.
- Equipment that is necessary for environmental safety. Example: Transformer leakage containment systems.
- Equipment that provides electrical infrastructure. Example: The switchgear supplied by the electrical service.
- Production equipment that the production department has identified (and ranked) as most critical to keep running. The calculation for this includes such things as revenue per hour, capacity to fill orders, and the requirement to satisfy a particular customer. On this last one, perhaps a line makes something that is No. 10 in profitability but there’s only one customer for it and there are other potential suppliers. So, either this line is reliable or that account will be lost.
Did you notice that production is No. 4 on that list and even then, we’re talking only about critical production?
Now that you have this list, work your way backward to determine how well maintenance supports each of those items. The metric “total training hours” is not relevant to maintenance performance but training targeted at each of those items is. In other words, training for the sake of training is not helpful. But training that supports the goals of the organization is helpful, extremely so.
If it’s been six years since anyone has had any training on fire pump maintenance and nobody in maintenance can select on a multiple-choice test which NEC article pertains to fire pumps, do you think maintenance gets an A on its report card even if each maintenance worker has totaled up 300 hours of training in the past year?
There is no set of metrics that works universally, but there are general principles that do. Apply those principles in relation to the plant’s hierarchy of equipment criticality, and you will be able to accurately see how well maintenance is doing and exactly where it needs to improve.
About the Author
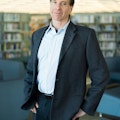
Mark Lamendola
Mark is an expert in maintenance management, having racked up an impressive track record during his time working in the field. He also has extensive knowledge of, and practical expertise with, the National Electrical Code (NEC). Through his consulting business, he provides articles and training materials on electrical topics, specializing in making difficult subjects easy to understand and focusing on the practical aspects of electrical work.
Prior to starting his own business, Mark served as the Technical Editor on EC&M for six years, worked three years in nuclear maintenance, six years as a contract project engineer/project manager, three years as a systems engineer, and three years in plant maintenance management.
Mark earned an AAS degree from Rock Valley College, a BSEET from Columbia Pacific University, and an MBA from Lake Erie College. He’s also completed several related certifications over the years and even was formerly licensed as a Master Electrician. He is a Senior Member of the IEEE and past Chairman of the Kansas City Chapters of both the IEEE and the IEEE Computer Society. Mark also served as the program director for, a board member of, and webmaster of, the Midwest Chapter of the 7x24 Exchange. He has also held memberships with the following organizations: NETA, NFPA, International Association of Webmasters, and Institute of Certified Professional Managers.