Four Electrical Infrastructure Tests to Add to Your Maintenance Routine
In the typical manufacturing plant, “maintenance” does not include attention to the electrical infrastructure. The focus of the typical maintenance department is on performing production equipment PMs and reacting to equipment failures. The assumption about the electrical infrastructure is once it works, it always works. The reality is different — and the consequences can be costly.
For example, a three-shift manufacturing plant in Alabama had an excellent equipment maintenance record. But this plant had a “time bomb” between one of its service entrances and the utility transformer. One of the cables had been spliced in a manner that wasn’t Code-compliant; the splice was improperly made and protected. The connection got hot, and the insulation around the spice melted, resulting in lots of acrid smoke. Despite heroic and costly efforts to repair the damage, this resulted in more than 24 hours of downtime for one-third of the plant.
Even correctly installed infrastructure will fail. Feeder cables subjected to repeated transient voltages, for example, begin to show evidence of insulation breakdown. That’s when they should be replaced, not when they fail unexpectedly. Their replacement should be planned and scheduled when this evidence of insulation breakdown is discovered; that’s how you keep costs down and uptime up. You discover this through one of many tests that should be performed regularly.
Among these are:
- Cable testing. This includes insulation resistance testing, low-resistance ohmmeter testing, and high-pot testing.
- Transformer testing. Oil-filled transformers allow for several tests to assess their condition. It’s a common misperception that you can’t run any tests on dry-type transformers, but a qualified thermographer will disagree.
- Bolted connection inspection and conductance testing. In a nod to infrastructure testing, some maintenance plans call for tightening bolted connections during a shutdown. This practice actually causes the connections to fail. Instead, you must assess the condition of the connection using a low-ohms meter. If it’s bad, disassemble it. Then clean the mating surfaces, replace the locking hardware, and torque to the recommended value. Retorquing does not work, because the initial torque is a measure of how much you permanently deform the connection hardware. You can torque a bolt only once; it’s a mechanical physics thing.
- Circuit breaker testing. The common misperception about breakers is if they are closed, they are fine. But the purpose of a breaker is to open the circuit when a certain current value is reached (and/or maintained for X time). A breaker that doesn’t open is merely a conductor. It’s no longer a circuit breaker and is no longer protecting the circuit or the premises.
Additional testing beyond the basics listed above may be indicated. But it takes expertise in infrastructure maintenance to identify what that testing would be.
The typical maintenance department is not set up for infrastructure maintenance. It lacks the qualified persons and the specific equipment. Odds are that a thorough search for the IEEE Red Book (the one that provides the standards for maintaining the power distribution system for an industrial plant) would turn up nothing. It is almost guaranteed that if you asked the plant electrical engineer what to do with insulation resistance test results, that person would not be able to give the correct answer (trend over time and look for the hockey stick). And that’s assuming there even is a plant electrical engineer.
A cost-effective solution that works for plants of all sizes is:
- Obtain the IEEE Red Book.
- Make a list of what tests should be run on what equipment and how often.
- Contact a firm that specializes in electrical testing of infrastructure to go over your plan and provide a time and cost quote. Be sure at this stage to also ask about availability, because you will need to schedule this well in advance.
- Repeat the preceding step twice.
- Compare the quotes. If one looks “too good to be true” compared to the other two, it probably is. Get a fourth quote.
- Decide on a time for scheduling the shutdown, and get preliminary approval.
- Decide on a firm. Agree on the shutdown time.
- Schedule the shutdown.
That’s a simplification of the plan. You’ll also need to arrange for security, plant personnel to escort and assist the testing personnel, a staging area, a secure storage area, parking and access, lighting needs, temporary power needs, and a host of other things. An experienced testing firm already has a list of these needs. Take their list not as “nice to have” but as essential items to provide. Get this rolling well in advance.
Following the testing, there’s a findings review that must be conducted. Let the testing firm take the lead there, as well. Part of it will involve their recommendations for a follow-up testing session. Part of it will involve their identification of “fix this as soon as you can” recommendations. If this list is long or the needs are beyond in-house expertise, then you will need to contract with an electrical services firm to do that work. There may be long lead times involved, so begin the discussion right away. For example, if you have an oil-filled transformer going bad you will likely have to order one to be built for you and the building process can take months.
Pro tip: You can get a jump start on failure prevention by obtaining the lifespan numbers from the manufacturer. For example, if you have feeder breakers that are 30 years old, it is probably time to replace them. So, what you’d want to do is replace them during the testing shutdown and have the testing firm take baseline data. Doing this is expensive and a hard sell to management, which is why you need something from the manufacturer.
Another way you can get ahead of failure is with oil-filled transformers. You can use a combination of age and oil sample testing to assess whether a transformer is at risk for failure. Schedule the replacement such that baseline testing can be performed by a qualified firm.
There is no better time to test equipment than when it is new. A common misperception is that you should wait a year before testing. But if you do that, you have no way to establish what is normal for that equipment in new condition and thus you have no baseline from which to assess deterioration. You have to wait a full year just to get a pseudo baseline and a total of two years to assess deterioration from the time of installation. A lot can happen in two years.
About the Author
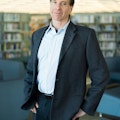
Mark Lamendola
Mark is an expert in maintenance management, having racked up an impressive track record during his time working in the field. He also has extensive knowledge of, and practical expertise with, the National Electrical Code (NEC). Through his consulting business, he provides articles and training materials on electrical topics, specializing in making difficult subjects easy to understand and focusing on the practical aspects of electrical work.
Prior to starting his own business, Mark served as the Technical Editor on EC&M for six years, worked three years in nuclear maintenance, six years as a contract project engineer/project manager, three years as a systems engineer, and three years in plant maintenance management.
Mark earned an AAS degree from Rock Valley College, a BSEET from Columbia Pacific University, and an MBA from Lake Erie College. He’s also completed several related certifications over the years and even was formerly licensed as a Master Electrician. He is a Senior Member of the IEEE and past Chairman of the Kansas City Chapters of both the IEEE and the IEEE Computer Society. Mark also served as the program director for, a board member of, and webmaster of, the Midwest Chapter of the 7x24 Exchange. He has also held memberships with the following organizations: NETA, NFPA, International Association of Webmasters, and Institute of Certified Professional Managers.