How to Cut Down on Motor Downtime Costs
If someone told you that corporate was going to make sure you have enough resources to cut in half the cost of motor downtime by 50% in your plant, would you have a good laugh? Most maintenance managers would.
However, most maintenance managers can get there without additional resources. It’s knowing how best to use existing resources that will get you there. This doesn’t mean pushing maintenance techs to work harder or faster, and it doesn’t involve shortcuts with safety. The key involves taking your limited resources away from maintaining motors where the potential costs of downtime are less significant and using those resources where the potential costs of downtime are greater. This is very different from the practice of allocating maintenance resources as if all motors are of equal value.
Follow these steps.
Step No. 1. Go into your CMMS and generate a report that includes each motor. Include this data in the report:
- Asset number
- Motor size
- Motor purpose / name of system (equipment, line, or whatever)
- Assigned maintenance procedures
- Associated PdM
- Associated monitoring
- Criticality score
The last item on the list above is probably not in there. Before filling it in, make sure all of the other items are completed.
Step No. 2. Assess and assign criticality. Here are the criticality categories:
- Category 0. Essential for protecting human life, the environment, or significant property. Examples include fire pump system motors (including pond aerators if used), oil sump motors, and process vat agitators where catastrophic damage will occur upon loss of agitation. This won’t be very many motors. Think of a failure here as akin to putting you in front of a fast-moving bus.
- Category 1. Major production assets. Downtime here may result in loss of significant revenue or an important customer. The production department can identify these, and it’s usually based on revenue. This won’t be very many motors, either.
- Category 2. Main production assets. Downtime here is painful, because of the revenue loss but it won’t put the plant at an existential risk. This category also includes human comfort assets, such as HVAC.
- Category 3. Minor production assets. Downtime here is undesired but not especially painful.
- Category 4. Assets that don’t contribute to revenue, or to protecting human life or the environment. An example would be motorized window blinds in the admin building.
Step No. 3. Allocate maintenance resources based on criticality.
- Category 0. Consult the appropriate standards from IEEE, ANSI, and NFPA for the recommended maintenance practices. Focus first on the predictive ones, and if you don’t have the inhouse expertise, either develop it or outsource it. Outsourcing also allows you to forego the cost of buying the specialized test equipment you will likely need. Identify any monitoring you can do in place of manual testing, and add it.
- Category 1. Implement the same program as for Category 0. Where there’s competition for resources, allocate them to Category 0 until you can resolve the conflict. For example, you have only X dollars available for thermography. Until you can bring thermography costs down (that is often possible by tweaking the program) or obtain more dollars, then Category 0 gets all it needs with Category 1 getting what’s left over.
- Category 2. Streamline manual maintenance tasks by accounting for the risk incurred if certain tasks are not done. For example, taking voltage measurements at the motor controller is nice if you can afford the time to do it. But failure rates here are extremely low. Bearing problems, however, are where you find the most failures. So what can you do to reduce bearing failures? Vibration monitoring, vibration analysis, and bearing temperature monitoring will definitely help. What about your motor lubrication program? Poor lubrication practices are common, and they result in excess bearing failures; so take a good hard look at how you lubricate motors. Odds are that you’re not doing it correctly.
- Category 3. If resources are thin by the time you get to these, then other than doing the motor lubrication (correctly), let them run to near failure. What is near failure, and how does that differ from failure? You can add inexpensive remote motor vibration monitoring, which will tell you when a motor’s bearings are damaged. You can then schedule a motor replacement before the motor fails and creates an unexpected production shutdown.
- Category 4. Generally, it is best to let these run to failure. If the motor for a set of motorized blinds fails, the downtime is no big deal and neither is replacing the motor. The same thing applies to sump pumps, which are not typically under constant demand anyhow. The run to failure thinking on these is starting to change, because it is now so easy and inexpensive to stick a vibration sensor on motors these days. You can get a warning that a motor’s bearings are headed for failure, and simply replace any such motor with that problem. But setting these up in the monitoring system can be time-consuming, so run to failure is still the dominant view.
Implementing this scheme isn’t always easy, because nobody wants their department to have downtime or equipment failures. You can stop the resistance to implementation by simply pointing out the relative values. A small grinder that’s used to generate $5,000/month of revenue as opposed to Line 3 that generates $5,000 an hour of revenue? It’s no contest.
About the Author
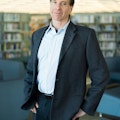
Mark Lamendola
Mark is an expert in maintenance management, having racked up an impressive track record during his time working in the field. He also has extensive knowledge of, and practical expertise with, the National Electrical Code (NEC). Through his consulting business, he provides articles and training materials on electrical topics, specializing in making difficult subjects easy to understand and focusing on the practical aspects of electrical work.
Prior to starting his own business, Mark served as the Technical Editor on EC&M for six years, worked three years in nuclear maintenance, six years as a contract project engineer/project manager, three years as a systems engineer, and three years in plant maintenance management.
Mark earned an AAS degree from Rock Valley College, a BSEET from Columbia Pacific University, and an MBA from Lake Erie College. He’s also completed several related certifications over the years and even was formerly licensed as a Master Electrician. He is a Senior Member of the IEEE and past Chairman of the Kansas City Chapters of both the IEEE and the IEEE Computer Society. Mark also served as the program director for, a board member of, and webmaster of, the Midwest Chapter of the 7x24 Exchange. He has also held memberships with the following organizations: NETA, NFPA, International Association of Webmasters, and Institute of Certified Professional Managers.