Improving Uptime by Addressing Maintenance Errors
Maintenance errors can lead a shadow existence, reducing uptime without ever being seen. Consider these examples:
- At an appliance plant in Tennessee, an inexplicably high rate of motor failure was attributed to apparently random power anomalies due to the process of elimination. Motor lubrication was eliminated from the list of potential failure causes because the records showed it was done on schedule. A major effort was put into chasing red herrings when all along the problem was the motor lubrication was done incorrectly. Once a qualified engineer looked at how maintenance was actually done, the problem was brought to light and corrected.
- After many years of reliability, barrel heaters began failing on a regular basis at a plastics plant in Alabama. Maintenance records showed the required PMs were being done, so troubleshooting got sent down the wrong fork in the road. The electrician who had previously been assigned to perform the PMs noticed the trouble began after his duties were changed. So he watched a PM being performed and identified the problem. The electrician who was now performing these was “retightening” the mounting screws, causing the heaters to warp slightly. The loss of contact with the barrels meant less heat transfer and more current being pushed through the heaters to get to the desired temperature, resulting in premature failure of the heaters.
- Feedwater controls were calibrated quarterly, using the wrong reference point at a nuclear power plant on the northeastern seaboard. This created a very tight window in which oscillations could occur without tripping the reactor. It tripped about three times per year, resulting in just over $1 million per incident. After each trip, a technician would decalibrate one or two of the controllers, and the system would be fine until the next calibration. This went on for over a decade before an outside contractor (this author) was tasked with solving the problem. Changing the PMs to use a different reference point solved the problem, and there were no more feedwater system trips of the reactor.
Just because a PM has been performed doesn’t mean the system or equipment is any better off than before. As these examples illustrate, a PM can actually reduce equipment reliability. A process to prevent this is as follows:
- Generate a report from your CMMS showing the most commonly performed PMs on critical equipment.
- Modify the report to also show the most common failure modes on critical equipment.
- Examine the data to identify the PMs that most likely entail maintenance errors.
- For each of the PMs from the previous step, have a qualified person examine how it is actually done in the field. Try to have this person witness performance by multiple technicians, and take notes on what is being done incorrectly or incompletely.
- Repeat the previous step using a different qualified person.
- Identify the maintenance errors, then update the procedures.
- Conduct training on the updated procedures, including hands-on demonstrations by both instructor and student(s). Only those who complete the training and pass a hands-on demonstration for a given PM procedure are qualified to perform the PM.
- Repeat the above process for non-critical equipment.
About the Author
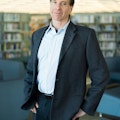
Mark Lamendola
Mark is an expert in maintenance management, having racked up an impressive track record during his time working in the field. He also has extensive knowledge of, and practical expertise with, the National Electrical Code (NEC). Through his consulting business, he provides articles and training materials on electrical topics, specializing in making difficult subjects easy to understand and focusing on the practical aspects of electrical work.
Prior to starting his own business, Mark served as the Technical Editor on EC&M for six years, worked three years in nuclear maintenance, six years as a contract project engineer/project manager, three years as a systems engineer, and three years in plant maintenance management.
Mark earned an AAS degree from Rock Valley College, a BSEET from Columbia Pacific University, and an MBA from Lake Erie College. He’s also completed several related certifications over the years and even was formerly licensed as a Master Electrician. He is a Senior Member of the IEEE and past Chairman of the Kansas City Chapters of both the IEEE and the IEEE Computer Society. Mark also served as the program director for, a board member of, and webmaster of, the Midwest Chapter of the 7x24 Exchange. He has also held memberships with the following organizations: NETA, NFPA, International Association of Webmasters, and Institute of Certified Professional Managers.