Electrical Troubleshooting Quiz — June 3, 2024
You were recently hired as the plant electrical engineer for a two-shift manufacturing plant that makes components a variety of industries. There are about 350 operators on the day shift and just over half as many on the backshift.
Your predecessor quit on short notice taking a job elsewhere. You learned from your lead electrician that her predecessor did the same thing. In fact, nobody seems to stay long in your job. You asked why, and he said, “Trying to get funds from management is like trying to get blood from a turnip.”
Now the plant engineer and plant manager have presented you with a problem they want fixed. Feeder cable failures have been increasing over the past decade, and four feeder cables have failed in the past two years. But they didn’t fail open — they failed to ground. “It always starts off with the breaker randomly tripping, then the trips happen more often then it just stays tripped. The problem is the cable shorts out somehow,” you are told.
You asked your lead electrician to show you the cable testing data in the CMMS, and after he stopped laughing, he reminded about the turnip. Without any cable testing data, how do you solve this problem?
Answer to Quiz. You don’t have an electrical problem to solve. You have a math problem to solve. On one side of the equation is the cost of cable testing and replacement. To get this done correctly and efficiently within a limited production downtime window, it will need to be outsourced to a qualified electrical testing firm. It can’t be just insulation resistance testing because one year’s worth of data is pretty useless; do it to establish a baseline for future testing. The testing firm will probably recommend hi-pot testing to find the cables with the most deteriorated insulation so those can be replaced before they fail.
On the other side of the equation, you have historical costs. The management already knows what a single cable failure has cost them, and they have plenty of examples — not just the repair costs but the downtime costs also. Get this second figure from the production department; how much revenue was lost during the unplanned outage caused by cable failure X? Also contact the sales department to see if they lost orders due to the downtime, and ask the plant controller for financial data related to cable failure X.
You can take the average cost of the last five failures, to show an “average cost” based on historical data. Now you can compare the cost of testing and scheduled repair to the cost of simply reacting to an unexpected failure.
That’s a best case scenario because due to sheer luck, none of those failures were catastrophic.
But a catastrophic failure is not unlikely. If they aren’t maintaining the feeder cables, it’s also true they aren’t testing the breakers. This sets the stage for a truly catastrophic event. This cost is enormous, and you don’t need to actually calculate it. You might ask the plant controller to give you a reasonable estimate.
Then there’s the middle scenario, one that also relies on luck. You just get more of the costly failures that aren’t catastrophic. How many of these can the company tolerate?
The same electrical testing firms that gave you a quote for cable testing (and other recommended testing) has data and anecdotes from many other plants. Ask them for something relevant to your situation. A feeder failure can result in more than just lost revenue due to downtime. A fire is sometimes the result. What damage have they seen, and do they have any photographs they can share?
Next, look more closely at your situation. The feeder failures have been accelerating. What if four fail in the same year? That’s not unlikely. Or what if the feeder to X equipment fails? How much would that cost in downtime to repair (revenue lost) and cost to repair?
Now you can describe, and provide costs for, multiple scenarios of feeder failure. None of them are good and each of them costs more that doing the maintenance that is required to safely operate the plant.
Go to management and show them the math. They will see that the best outcome that can be achieved financially and otherwise is to perform the recommended testing at the recommended times so preventive measures can be taken. Then feeder failures stop happening because you can replace deteriorating feeders before failure occurs. This is the real solution to the problem.
About the Author
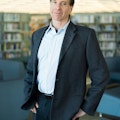
Mark Lamendola
Mark is an expert in maintenance management, having racked up an impressive track record during his time working in the field. He also has extensive knowledge of, and practical expertise with, the National Electrical Code (NEC). Through his consulting business, he provides articles and training materials on electrical topics, specializing in making difficult subjects easy to understand and focusing on the practical aspects of electrical work.
Prior to starting his own business, Mark served as the Technical Editor on EC&M for six years, worked three years in nuclear maintenance, six years as a contract project engineer/project manager, three years as a systems engineer, and three years in plant maintenance management.
Mark earned an AAS degree from Rock Valley College, a BSEET from Columbia Pacific University, and an MBA from Lake Erie College. He’s also completed several related certifications over the years and even was formerly licensed as a Master Electrician. He is a Senior Member of the IEEE and past Chairman of the Kansas City Chapters of both the IEEE and the IEEE Computer Society. Mark also served as the program director for, a board member of, and webmaster of, the Midwest Chapter of the 7x24 Exchange. He has also held memberships with the following organizations: NETA, NFPA, International Association of Webmasters, and Institute of Certified Professional Managers.