Working with Contractors as Electrical Maintenance Workers
You may have heard the occasional contractor horror story, but it doesn’t mean you shouldn’t trust contractors. In fact, contractor success stories abound. In many plants, contractors are a flexible, welcome supplement to the maintenance work force. Whether bringing in skills you don’t have or just providing extra labor, contractors can — and often do — truly add to the safety, performance, and cost-effectiveness of maintaining plant equipment and infrastructure.
How do the successful plants achieve their success with contractors? Here are some recommendations to keep in mind.
- Clearly define the project and the contractor’s role. Discuss what you want done and what the contractor can do. Come to an agreement on exactly what will be done, when it will be done, what resources you will and will not provide, and how the work will be inspected/approved. Then put this into a written agreement.
- Agree on clean-up issues. Ideally, the contractor will remove all scrap material and related items, disposing of them per your company policy and the plant’s procedures.
- Get the estimate signed and approved before work begins. Don’t surprise the plant controller with an unexpected expense. Make sure the estimated completion date also gets the blessing of the plant manager and the plant controller so they know when the funds will be needed.
- Stick with the scope. Once you hire a contractor to do X job, don’t unilaterally expand the scope. If the contractor identifies something additional that must be done, don’t ask them to “throw that in.” Treat it as an additional project and decide whether it will be done concurrent with this one, after this one, or as a prerequisite to this one.
- Give the contractor a single point of contact. Don’t make them chase down Bill for one thing, Susan for another, and Hector for yet another. This leads to confusion, inefficiency, cost overruns, and scheduling problems. The single point of contact for the contractor should handle the company’s internal issues for the contractor — whether that’s security or arranging for safety training.
- Ensure access from day one. Get gate access, building access, security badges, break room privileges, etc., arranged ahead of time. On the first day, the single point of contact should either greet the contractor at a pre-arranged point or be readily available to respond to a call to meet them.
- If providing equipment, such as a scissor lift, ensure it’s in working order at least a day before the contractor arrives. Have a means of qualifying the contractor to operate it, unless you are also providing a person to operate it. Double check portable lighting, portable cords, and anything else you are providing.
- Don’t nickel and dime them on supplies. Generally, it is the contractor’s duty to provide the tools and materials needed to complete the work. But sometimes, things just happen. Maybe someone drops a nut from a ladder, and it can’t be found. Why send one of the contractors to the local home center when you have fasteners in your stock room? If a test lead comes apart and they don’t have a spare, you can supply them a set. Something more expensive, however, needs to be replaced by them or paid for as a line item deduction against their project fee.
- Don’t hover over them. Depending upon the project and your plant’s security protocols, someone may need to escort the contractor at all times. If this is the case, the escort must understand the importance of not distracting the contractor with chit chat or interfering with them in any other way such as micromanaging their work. This person, however, should answer any questions the contractor has (either directly or by contacting someone who would have the correct answer).
- Inspect often. When a qualified person periodically inspects the work as it proceeds, this is much more efficient than ripping things out because you found a problem at the end. This inspection person may or may not be the escort. Any issues should be discussed with the contractor’s on-site foreman or project manager. The only exceptions are if there’s a safety violation or an environmental rules violation; stop the work immediately to resolve the problem. Then report this to the onsite foreman and the company’s project manager.
- Update the plant manager on the progress of the project at each major stage. A small project can be considered to have one stage: completion. If there are internal customers, such as a production superintendant, update them as well. Updates need to be short but informative and should cover not just progress but also problems encountered and any changes to cost or scheduling.
- Pay fully and on time. Help the contractor correctly submit the invoice. If it’s a large amount that would create a financial burden for the contractor if payment is late, follow up to ensure Accounts Payable is processing it.
- Do a follow-up. If you liked working with this contractor and vice-versa, have a short conversation about working together in the future. What did you learn from this project that could make a future one go more smoothly? Having a long-term relationship with a trusted, proven contractor can pay huge dividends.
This last point is exemplified by this short case history. A plant in central Tennessee had three service entrances. On the Fourth of July one year, one of those went up in smoke. The plant electrical engineer called his trusted, proven contractor, and they had a team out there in less than an hour on that holiday. Amazingly, that part of the plant was ready for operations again by 6:00 the following morning — about the time the last of the contractors drove off.
About the Author
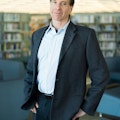
Mark Lamendola
Mark is an expert in maintenance management, having racked up an impressive track record during his time working in the field. He also has extensive knowledge of, and practical expertise with, the National Electrical Code (NEC). Through his consulting business, he provides articles and training materials on electrical topics, specializing in making difficult subjects easy to understand and focusing on the practical aspects of electrical work.
Prior to starting his own business, Mark served as the Technical Editor on EC&M for six years, worked three years in nuclear maintenance, six years as a contract project engineer/project manager, three years as a systems engineer, and three years in plant maintenance management.
Mark earned an AAS degree from Rock Valley College, a BSEET from Columbia Pacific University, and an MBA from Lake Erie College. He’s also completed several related certifications over the years and even was formerly licensed as a Master Electrician. He is a Senior Member of the IEEE and past Chairman of the Kansas City Chapters of both the IEEE and the IEEE Computer Society. Mark also served as the program director for, a board member of, and webmaster of, the Midwest Chapter of the 7x24 Exchange. He has also held memberships with the following organizations: NETA, NFPA, International Association of Webmasters, and Institute of Certified Professional Managers.