Electrical Troubleshooting Quiz — May 6, 2025
In this scenario, the plant is divided into four parts. Motor failures in three of them are fairly rare and the rates are similar. Once a motor is replaced, that is pretty much the last time. You work as a maintenance electrician in one of those areas. In the fourth area, motor failures occur at a much higher rate and a few of those motors have been replaced four times in the past three years.
Until recently, nobody was aware of this difference because there are de facto four maintenance departments. They are siloed from each other. They don’t share people or maintenance reports. The problem was identified by the new plant electrical engineer. Digging into this is on her list, but it’s a big list. She is also tasked with either hiring someone as her assistant or promoting a maintenance electrician into that job. After doing some research into who might be a good candidate, she settled on you. If you can solve this problem for her, she will put you in for the promotion.
What can you rule out right away, and what are some things you should look at?
Answer to Quiz
Unless this fourth area is on its own service, you can rule out power supply problems such as low voltage. You can also rule out motor storage issues, motor sourcing issues, and the like because the stockroom and the purchasing department aren’t part of this silo mentality that exists in maintenance.
The most likely problem, given the silo mentality, is that maintenance in this area operates differently than maintenance in the others. One likely difference is how they perform motor lubrication. This job is typically not handled by a junior person, because it requires precision, attention to detail, and strict adherence to well thought-out practices. What often happens instead is that the job is considered grunt work, and it’s done with no training, no oversight, and no skill. The results include such things as overgreasing, undergreasing, not leaving the drain plug out long enough (or removing it at all), and using incompatible greases. All of which lead to early motor failure. So, check into that fourth area to see exactly who is doing the motor lubrication, exactly what grease they are using, and exactly how they are performing the grease change.
If all this checks out, and it probably won’t, then look at the power factor, harmonics, and voltage balance at each motor. The first two can almost always be fixed with a variable speed drive. The last one will require some rewiring, but maybe only at a panel or two.
The plant has four areas, are they serving significantly different functions? This could mean radically different loads. Ensure each motor correctly matches the application it’s intended for. That includes not only the size, but the design type and insulation rating.
Do a failure analysis, determining the failure mode for each motor that has been replaced over the past three years. You can do this with a spreadsheet and then create a bar graph sorting from highest to lowest. This gives you a Pareto analysis. For the sake of efficiency, focus on the three modes with the tallest bars. It won’t take much digging to identify what maintenance failures or other issues are causing these. Once you know, you can make a list of suggested fixes to provide for your prospective new boss.
About the Author
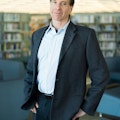
Mark Lamendola
Mark is an expert in maintenance management, having racked up an impressive track record during his time working in the field. He also has extensive knowledge of, and practical expertise with, the National Electrical Code (NEC). Through his consulting business, he provides articles and training materials on electrical topics, specializing in making difficult subjects easy to understand and focusing on the practical aspects of electrical work.
Prior to starting his own business, Mark served as the Technical Editor on EC&M for six years, worked three years in nuclear maintenance, six years as a contract project engineer/project manager, three years as a systems engineer, and three years in plant maintenance management.
Mark earned an AAS degree from Rock Valley College, a BSEET from Columbia Pacific University, and an MBA from Lake Erie College. He’s also completed several related certifications over the years and even was formerly licensed as a Master Electrician. He is a Senior Member of the IEEE and past Chairman of the Kansas City Chapters of both the IEEE and the IEEE Computer Society. Mark also served as the program director for, a board member of, and webmaster of, the Midwest Chapter of the 7x24 Exchange. He has also held memberships with the following organizations: NETA, NFPA, International Association of Webmasters, and Institute of Certified Professional Managers.