How Maintenance Can Better Support Production
The production department of any manufacturing plant exists to get product out the door, on time, within budget, and made to spec. The maintenance department of any manufacturing plant exists to support the production department in this goal.
Maintenance does this by such things as preventing unscheduled downtime and optimizing machine performance. And maintenance does this within its budget. The funding for that budget comes out of the revenue generated by the production department. This relationship puts the maintenance function secondary to the production function, even though the two functions depend on each other.
When there’s a problem, such as a production shortfall, someone has to take the blame for it. This dynamic can create a blame game relationship between people in the two departments scenario instead of a mutually supporting problem-solving one. To avoid the former and foster the latter, give the production department what they need.
What production does not need:
- Maintenance planners planning work based on convenience to the maintenance department. Instead, ask the maintenance department to prioritize the equipment and help determine when equipment can be available for the recommended maintenance.
- Maintenance workers “correcting” operators. That is the job of production supervisors. Instead, ask the operator questions if you perceive an operator error. For example, a maintenance tech can explain that he understands the process to be X, and then ask if that’s changed. If you don’t get a resolution, you may just have to be patient.
- Blame. When a problem is discovered, don’t jump to judgment and don’t start pointing fingers. If you are blamed for something, don’t blame back. Instead, admit that the problem may lie with maintenance but further fact gathering is needed to determine the actual cause so that a solution can be implemented. Ask if you can have 48 hours (or whatever time seems appropriate) to report back with your findings.
- Excuses. Nobody wants to hear why you “can’t” solve their problem or why you failed to adequately do so. Instead, own the problem. People respond much more favorably to seeing responsible behavior than seeing someone trying to avoid responsibility through excuse-making.
- Promises. Nobody likes it when a promise isn’t kept. So don’t promise to deliver something when you don’t yet know the full scope of what must be done. “We’ll have it up again within the hour” can really backfire. Instead, provide assurance that you are taking the problem seriously and then outline what your first steps will be.
- Sloppiness. Your work must be professional. Work methodically, clean up after yourself, document things properly,
- Surprises. Keep the affected parties informed. Hiding a problem until stakeholders are affected by it will make it impossible for them to prepare for it. Always give production an accurate report of anything you do for them.
- Call backs. “There’s never enough time to do it right, but always enough time to do it over.” It is much better to spend 10 or 15 extra minutes ensuring a repair or maintenance task is properly done (including clean-up, testing, and operational verification with the operator) than to get another trouble call for the same problem. Especially if they have to wait through half an hour of additional downtime due to the error.
- Injuries. Last, but not least, safety is paramount. No good manager of any department wants to see people injured. Aside from the humanitarian aspects, there are many big costs involved. Generally, a serious injury on the job is bad for everyone not just the injured person. The difference between a serious injury and a close call is just dumb luck, so put safety first rather than push the envelope on it.
About the Author
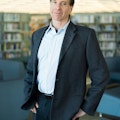
Mark Lamendola
Mark is an expert in maintenance management, having racked up an impressive track record during his time working in the field. He also has extensive knowledge of, and practical expertise with, the National Electrical Code (NEC). Through his consulting business, he provides articles and training materials on electrical topics, specializing in making difficult subjects easy to understand and focusing on the practical aspects of electrical work.
Prior to starting his own business, Mark served as the Technical Editor on EC&M for six years, worked three years in nuclear maintenance, six years as a contract project engineer/project manager, three years as a systems engineer, and three years in plant maintenance management.
Mark earned an AAS degree from Rock Valley College, a BSEET from Columbia Pacific University, and an MBA from Lake Erie College. He’s also completed several related certifications over the years and even was formerly licensed as a Master Electrician. He is a Senior Member of the IEEE and past Chairman of the Kansas City Chapters of both the IEEE and the IEEE Computer Society. Mark also served as the program director for, a board member of, and webmaster of, the Midwest Chapter of the 7x24 Exchange. He has also held memberships with the following organizations: NETA, NFPA, International Association of Webmasters, and Institute of Certified Professional Managers.