Handling Preventive Maintenance (PM) Backlogs
If your PMs are scheduled correctly, then you are doing just enough PM work to take corrective action before emerging problems significantly degrade equipment performance and/or interrupt operation of that equipment. This means that getting behind schedule on PMs increases the likelihood of equipment degradation or failure. Simply staying behind isn't a practical option.
Unfortunately, many things can cause you to fall behind on PMs. Two big causes are personnel changes and unplanned downtime, both of which hold clues for catching up:
- Re-evaluate and streamline PM procedures to eliminate unnecessary steps.
- Hire a contractor to supplement your workforce, performing a specific project that would otherwise occupy your people.
- Invest in better tools and test equipment to increase worker efficiency.
- Invest in training so people are not only more skilled, but also feel more valued.
- Contract out a predictive maintenance (PdM) project (e.g., ultrasonic bearing analysis) and the repair work for the problems found.
About the Author
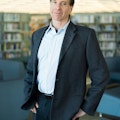
Mark Lamendola
Mark is an expert in maintenance management, having racked up an impressive track record during his time working in the field. He also has extensive knowledge of, and practical expertise with, the National Electrical Code (NEC). Through his consulting business, he provides articles and training materials on electrical topics, specializing in making difficult subjects easy to understand and focusing on the practical aspects of electrical work.
Prior to starting his own business, Mark served as the Technical Editor on EC&M for six years, worked three years in nuclear maintenance, six years as a contract project engineer/project manager, three years as a systems engineer, and three years in plant maintenance management.
Mark earned an AAS degree from Rock Valley College, a BSEET from Columbia Pacific University, and an MBA from Lake Erie College. He’s also completed several related certifications over the years and even was formerly licensed as a Master Electrician. He is a Senior Member of the IEEE and past Chairman of the Kansas City Chapters of both the IEEE and the IEEE Computer Society. Mark also served as the program director for, a board member of, and webmaster of, the Midwest Chapter of the 7x24 Exchange. He has also held memberships with the following organizations: NETA, NFPA, International Association of Webmasters, and Institute of Certified Professional Managers.