Art. 430, Part VIII provides the requirements for motor control centers (MCCs). The requirements for motor control circuits are in Part VI, and the requirements for motor controllers are in Part VII.
An MCC is a centralized system of panels for supplying, controlling, and protecting motor circuits. Among other advantages, an MCC:
- Reduces construction costs because supply feeders come to a single place (the MCC) instead of being run in multiple directions.
- Improves floor space utilization efficiency via equipment density. That leaves more space for revenue production.
- Declutters the floor space. This provides a neater appearance while allowing for better lighting and easier conformance to working space requirements.
- Reduces the costs of startup, maintenance, and repair by eliminating all the walking between equipment that would be necessary with a distributed arrangement.
MCCs must have overcurrent protection, and comply with Parts I, II, and III of Art. 240 [430.94]. You can provide the protection ahead of the MCC or use a main overcurrent protection device within the MCC.
If the MCC is used as a service, it must have a single main to disconnect all ungrounded service conductors [430.95]. However, you can use a second disconnect for additional equipment. For service-entrance MCCs, place barriers to isolate service busbars and terminals from the rest of the MCC [430.97(E)].
What if your MCC consists of multiple sections? This is a common configuration. To prevent dangerous differences of potential between these sections, you must bond them with an equipment grounding conductor [430.96]. Note that the term “equipment grounding conductor” means equipment bonding conductor. There’s no ground connection; ground means the earth [100]. You will find a list of approved equipment “grounding” (bonding) conductors in 250.118.
The requirements for busbar in MCCs [430.97] echo those presented for switchboards [408.3] and industrial control panels [409.102]. How they differ: the switchboard requirements don’t address phase arrangement and the industrial control panel requirements don’t address horizontal runs through sections. The MCC requirements address both.
Minimum wire-bending space in MCCs must comply with Art. 312. The minimum wire-bending space at terminals is provided by Table 312.6(B).
Please note that bend radius specifications for conductors apply to the installation procedure, not the finished installation. If the bend radius is exceeded at any time, even just for a second and only once, the insulation is probably damaged. Factor this in when considering how much clearance you actually need for the type and size of conductors you will be installing. You also need minimum spacing between bare metal parts, per 430.97(D).
Part VIII concludes with a requirement for documenting the available fault current at the MCC [430.99]. The documentation must include the date of the fault current calculation and be available to those authorized to inspect, install, or maintain the installation.
Implied, but not stated, here is the requirement that a new fault current calculation is performed if there’s any modification that would possibly render the last calculation obsolete. You can compare the date of the calculation to the date of equipment changes, and then look at those changes to see if any conflicts may exist.
About the Author
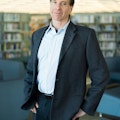
Mark Lamendola
Mark is an expert in maintenance management, having racked up an impressive track record during his time working in the field. He also has extensive knowledge of, and practical expertise with, the National Electrical Code (NEC). Through his consulting business, he provides articles and training materials on electrical topics, specializing in making difficult subjects easy to understand and focusing on the practical aspects of electrical work.
Prior to starting his own business, Mark served as the Technical Editor on EC&M for six years, worked three years in nuclear maintenance, six years as a contract project engineer/project manager, three years as a systems engineer, and three years in plant maintenance management.
Mark earned an AAS degree from Rock Valley College, a BSEET from Columbia Pacific University, and an MBA from Lake Erie College. He’s also completed several related certifications over the years and even was formerly licensed as a Master Electrician. He is a Senior Member of the IEEE and past Chairman of the Kansas City Chapters of both the IEEE and the IEEE Computer Society. Mark also served as the program director for, a board member of, and webmaster of, the Midwest Chapter of the 7x24 Exchange. He has also held memberships with the following organizations: NETA, NFPA, International Association of Webmasters, and Institute of Certified Professional Managers.