Traditionally, we think of repairs as what you do to restore equipment to its normal condition. For example, a palletizer stops working because its drive motor throws a bearing. You replace the motor.
But what if your plant had a policy that says every time you replace or service a motor, you ensure it has remote sensors on it? The next time that palletizer motor is overheated, vibrates excessively, or exhibits any problems that your Internet of Things (IoT) system is monitoring for (or maybe you're not with IoT yet but have something that still monitors), someone can fix the problem before expensive downtime is incurred.
Stop thinking of repairs as just a means of restoring operation. Start thinking of them as a means to increase reliability.
In some cases, it won't mean adding remote sensors and monitoring when directly replacing equipment. It will mean adding those to equipment upgrades or it will mean upgrading the equipment to a version that has connectivity (“smart breakers,” for example).
You can't expect the repair tech, who is usually under time pressure, to think of these enhancements on the fly. They need to be planned, one asset number at a time. Plan in the CMMS and have the necessary parts in the stockroom.
About the Author
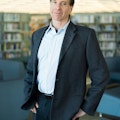
Mark Lamendola
Mark is an expert in maintenance management, having racked up an impressive track record during his time working in the field. He also has extensive knowledge of, and practical expertise with, the National Electrical Code (NEC). Through his consulting business, he provides articles and training materials on electrical topics, specializing in making difficult subjects easy to understand and focusing on the practical aspects of electrical work.
Prior to starting his own business, Mark served as the Technical Editor on EC&M for six years, worked three years in nuclear maintenance, six years as a contract project engineer/project manager, three years as a systems engineer, and three years in plant maintenance management.
Mark earned an AAS degree from Rock Valley College, a BSEET from Columbia Pacific University, and an MBA from Lake Erie College. He’s also completed several related certifications over the years and even was formerly licensed as a Master Electrician. He is a Senior Member of the IEEE and past Chairman of the Kansas City Chapters of both the IEEE and the IEEE Computer Society. Mark also served as the program director for, a board member of, and webmaster of, the Midwest Chapter of the 7x24 Exchange. He has also held memberships with the following organizations: NETA, NFPA, International Association of Webmasters, and Institute of Certified Professional Managers.