In the NEC, the word “hazardous” denotes the way a particular location is classified due to either:
1. Flammability properties within that area (Art. 500 – 506).
2. Specific use of that area (Art. 510 – 517).
In this article, we’ll look at how locations are classified according to flammability properties. Hazardous location requirements exist not only to prevent a fire or explosion, but also to contain the fire or explosion should it occur. An explosion-proof enclosure, for example, is designed to contain and suppress an explosion — not, as might be supposed, to protect what’s inside the enclosure if an explosion occurs.
Hazardous organization
The NEC arranges flammability properties into Class I, II, and III, in Art. 501, 502, and 503, respectively. It defines and describes these in Art. 500 (OSHA also defines and describes these). Art. 500 is the basis for all hazardous location work and the related Articles that follow it (see Figure).
You don’t use Art. 500 by itself; you always pair it with at least one other in the series. All hazardous locations come under Art. 500. Then the requirements are modified according to Class (and then further modified according to additional breakdowns).
Something you may notice in Art. 500 is the sheer number of Informational Notes. There are nearly five dozen of them, most of which are references to other standards.
Another difference you see in Art. 500 is it seems to avoid these two rules:
• Article-specific definitions are in the xxx.2 section of an Article.
• Definitions appearing in multiple Articles are in Art. 100.
You won’t find the definition of a Class I, II, or III location in Sec. 500.2, because that definition isn’t specific to Art. 500. However, it’s not in Art. 100 either. Instead, turn to Sec. 500.5. There, you’ll find that 500.5(A) requires you to classify locations based on the properties of flammables or combustibles present (or likely to be present). It also provides a short definition of each:
• 500.5(B). Class I: Flammable gases. Art. 501.
• 500.5(C). Class II: Combustible dust. Art 502.
• 500.5(D). Class III: Easily ignitable fibers/flyings. Art 503.
Mixed particles
Notice that the ignitables get bigger as the class number increases. Unfortunately, there isn’t always a clear boundary (and the NEC allows for this). You can easily have a mix of particle sizes.
Suppose you are working in a Class III (Art. 503) location, such as a sawmill. The same material (e.g., sawdust) may be Class II (Art. 502) if the predominant material is “larger” than dust.
But when should you consider sawdust to be fiber instead of dust? The 2011 NEC actually has a precise answer to that question in 500.2. It defines combustible dust as finely divided solid material that’s 420 microns (or smaller) in diameter and presents a fire or explosion hazard when dispersed and ignited in air.
Electricians generally don’t carry around equipment for obtaining and measuring continuous flow samples of airborne particulates, so why does the NEC provide this number? The facility operator will know the ranges of particulate size, and you use that information rather than playing chemist for the day.
The number gives you a reference basis, but the NEC doesn’t prevent you from considering a location Class II if the fibers happen to be 421 microns instead of 420. Sometimes, the choice between Class II and Class III locations is one of erring on the side of caution. The question is not one of “What can I get by with?” but “How do I prevent ignition?”
The site’s insurer will have to approve the Class II versus III decision. If there’s a reasonable possibility that Class II size particulates could be present in significant quantity to ignite an explosion someday, the insurer will probably want the tighter standards. That means designating the area as Class II rather than Class III.
Divisions, zones, and groups
In Art. 500, 501, 502, and 503, Class I, II, and III locations are further broken down into Divisions. The simplified version is a given Class will be either:
• Division 1: The ignitables are significantly present under normal conditions.
• Division 2: The ignitables are significantly present under abnormal conditions.
You’ll find more nuanced descriptions of Division 1 and Division 2 for Class I, II, and III respectively in 500.5(B), (C), and (D).
In Art. 505, the NEC presents a zone classification system as an alternative to the Class I division classification system in Art. 500. In Art. 506, the NEC presents a zone classification system as an alternative to the division classification system in Art. 500, 502, and 503.
Correctly determining the Class and then the Division or Zone is critical to correctly applying the requirements for a given hazardous location. Obviously, sealing against gases (Class I) is more difficult than sealing against fibers (Class III). Whether the ignitables are normally present in concentrations high enough to present a combustion hazard (Division or Zone) also bears upon what measures you need to take to prevent the ignition of flammables and the spread of combustion.
In addition to these classifications, you also must determine the Group. [500.6]. For Class I, Group A is acetylene. Groups B through D are materials with different ranges of combustibility. For Class II, it’s Group E, F, or G, depending upon the material.
Protection techniques
The NEC provides 11 protection techniques [500.7]. Some are permissible in some situations but not in others. For example, you can use dusttight equipment in a Class III area, but in a Class I area you must use explosionproof equipment. The reason is dusttight equipment can prevent fibers from getting in or out, but they can’t stop gases.
The NEC also provides many equipment requirements [500.8]. Any equipment you install must:
• Be determined to be suitable for the intended use [500.8(A)].
• Be identified for use in the Class and Group of the
location [500.8(B)(1)].
• Meet specific external or exposed surface temperature requirements [500.8(B)(1)].
• Be marked to show its temperature range and the environment for which it has been evaluated [500.8(C)].
Temperature classes
Unfortunately, temperatures are also designated with a class system. You’ll have to be careful not to confuse the temperature class with the hazardous area class.
• Class I applies to vapors and gases. The temperature marking can’t exceed the ignition temperature of the specific gas or vapor to be encountered.
• Class II applies to dust. The temperature marking must be less than the ignition temperature of the specific dust to be encountered.
For general circuits, you must close unused openings of enclosures [110.12(A)]. But for Class II Temperature classes, you must use listed metal close-up plugs [500.8(E)(3)].
All Class II Temperature raceway is threaded; you must use conduit rather than tubing. Make the conduit and fittings wrenchtight, for two reasons:
1. To prevent sparking when fault current flows through the conduit system.
2. To ensure the explosion-proof integrity of the conduit system (where applicable).
Applying Art. 500 through 517
You don’t classify a building as Class I, II, or III. You classify an area. For example, consider a fairly typical factory situation. In one wing, workers make parts from combustible material. There’s combustible dust in the air. In another wing, where they dip and clean, the air contains combustible vapor. You would not need to classify the whole building as Class I — just the area where the vapors are present.
You can think of Art. 500, 501, 502, and 503 as a set of Articles that detail the requirements for hazardous locations. Art. 505 and 506 provide alternative requirements to the Division system of those other Articles.
Given that structure, Art. 504 could be viewed as being out of sequence. It provides the requirements for a special kind of circuit that can be used in hazardous locations. That circuit is “intrinsically safe,” meaning it can’t create a spark or thermal effect capable of igniting the flammable gas-air, vapor-air, or dust-air.
For certain occupancies, Art. 510 through 517 apply. In any given occupancy, you might have Class I, Class II, and Class III locations all present. You will always apply Art. 500, but you may also apply several other articles from 501-517 in a given facility.
Always begin by examining each area for what combustibles are present, or may be present, in sufficient quantities to cause ignition. Then classify the area accordingly. This will tell you whether Art. 501, 502, or 503 applies to that area. If you wish an alternative to the Division system, apply Art. 505 or 506. If you are installing intrinsically safe equipment, apply Art. 504.
On top of this, apply the appropriate Article from 510 through 517 if the area or occupancy is a garage, aircraft hanger, fuel-dispensing facility, bulk storage plant, spray application, dipping/coating process, or health care facility.
Lamendola is an electrical consultant based in Merriam, Kan. He can be reached at [email protected].
About the Author
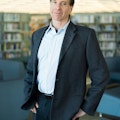
Mark Lamendola
Mark is an expert in maintenance management, having racked up an impressive track record during his time working in the field. He also has extensive knowledge of, and practical expertise with, the National Electrical Code (NEC). Through his consulting business, he provides articles and training materials on electrical topics, specializing in making difficult subjects easy to understand and focusing on the practical aspects of electrical work.
Prior to starting his own business, Mark served as the Technical Editor on EC&M for six years, worked three years in nuclear maintenance, six years as a contract project engineer/project manager, three years as a systems engineer, and three years in plant maintenance management.
Mark earned an AAS degree from Rock Valley College, a BSEET from Columbia Pacific University, and an MBA from Lake Erie College. He’s also completed several related certifications over the years and even was formerly licensed as a Master Electrician. He is a Senior Member of the IEEE and past Chairman of the Kansas City Chapters of both the IEEE and the IEEE Computer Society. Mark also served as the program director for, a board member of, and webmaster of, the Midwest Chapter of the 7x24 Exchange. He has also held memberships with the following organizations: NETA, NFPA, International Association of Webmasters, and Institute of Certified Professional Managers.