Summarizing NEC Art. 503 on Class III Locations
Article 503 is the third in the series of Class X Location Articles. These can be summarized as:
- Article 501, Class I Locations. Gases.
- Article 502, Class II Locations. Liquids.
- Article 503, Class III Locations. Fibers.
For more detailed explanations of Class I, II, and III locations, see Sec. 500.5. What’s important to notice here is the “stuff” gets bigger as the Class number increases. Thus, the requirements are most stringent for Class I locations and least stringent for Class III locations. Accordingly, Art. 501 is longer and more detailed than Art. 502. And in turn, Art. 502 is longer and more detailed than Art. 503.
A peculiarity of fibers is the thermal aspect. They can insulate equipment, resulting in fire or damage such as carbonization. Thus the general requirement is that equipment in Class III locations be able to function at full rating without developing excess surface temperatures [503.5]. The thermal aspect also comes into play when selecting motors. For example, they must be totally enclosed, nonventilated, totally enclosed pipe ventilated, or totally enclosed fan cooled [503.125]. One reason for this rule is to keep combustibles out of motors so they don’t ignite, but it has the added benefit that your motor won’t rely on air flowing through it and thus overheat as fibers build up/block that airflow. In a pulp mill, for example, you need totally enclosed motors for this reason.
The wiring methods for Division 1 (combustibles present under normal conditions) are repeated for Division 2 (combustibles present only under abnormal conditions) [503.10(a)(1)], but in Division 2, you are permitted to use open wiring on insulators in areas that are used soley for storage if you meet a couple of conditions [503.10(B)(2)].
For raceways, Arts. 501 and 502 limit you to conduit, but Art. 502 also permits you to use electrometallic tubing EMT [503.10(A)(1)(1)]. If you think about how you assemble conduit versus how you assemble tubing, then the exclusion of EMT for gases and liquids makes sense and so does its inclusion for fibers. The rules for flexible connections [503.10(A)(3] also make sense with this thought in mind. Boxes and fittings must be dust-tight [503.10(A)(2)]. You can install nonincendive field wiring using any of the wiring methods permitted for unclassified locations [503.10(A)(4)].
You can’t have uninsulated exposed parts that operate at more than 30V (15V in wet locations). [503.25]. This requirement should not be particularly surprising, nor should the “grounding” (bonding) requirements for wiring systems and equipment [503.30]. As with other hazardous locations, you must bond per Art. 250 Part VI (equipment “grounding” and equipment “grounding” conductor). If you look at Figure 250.1, you will also see that Parts IV and V of Art. 250 also apply. And, of course, you cannot rely on locknut bushings or double locknuts for bonding purposes; use bonding jumpers to complete the bonding path.
You’ll find equipment requirements for Class III locations in Art. 503, Part III. Most everything needs to be dusttight. The goal is to keep fibers out of the equipment. Even ventilation pipes must be tight enough at connection points to prevent the ingress of appreciable amounts of fibers. If you keep that goal in mind as you design and install electrical systems and equipment in Class III locations, you’ll meet most of the requirements almost automatically.
About the Author
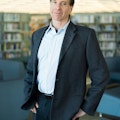
Mark Lamendola
Mark is an expert in maintenance management, having racked up an impressive track record during his time working in the field. He also has extensive knowledge of, and practical expertise with, the National Electrical Code (NEC). Through his consulting business, he provides articles and training materials on electrical topics, specializing in making difficult subjects easy to understand and focusing on the practical aspects of electrical work.
Prior to starting his own business, Mark served as the Technical Editor on EC&M for six years, worked three years in nuclear maintenance, six years as a contract project engineer/project manager, three years as a systems engineer, and three years in plant maintenance management.
Mark earned an AAS degree from Rock Valley College, a BSEET from Columbia Pacific University, and an MBA from Lake Erie College. He’s also completed several related certifications over the years and even was formerly licensed as a Master Electrician. He is a Senior Member of the IEEE and past Chairman of the Kansas City Chapters of both the IEEE and the IEEE Computer Society. Mark also served as the program director for, a board member of, and webmaster of, the Midwest Chapter of the 7x24 Exchange. He has also held memberships with the following organizations: NETA, NFPA, International Association of Webmasters, and Institute of Certified Professional Managers.