Navigating the NEC’s Requirements for Hazardous (Classified) Locations
Rules for hazardous (classified) locations can be found in Chapter 5 [Special Occupancies] of the National Electrical Code (NEC). What are these specific locations, and why is the word “classified” in parentheses? These are typically two of the first questions people ask when they review this chapter in the Code.
In the early days of the NEC, electricity itself was considered hazardous. Certain locations, where gasoline vapors might be present, were considered “extra-hazardous.” An electrical spark or heat from electrical equipment may ignite the vapors with catastrophic results. As the Code evolved, we have successfully managed the everyday hazards of electricity through proper installation. In specific locations where flammable gases or vapors, combustible dusts, fibers, or flyings may be present, specific installation practices must be followed to prevent fire and explosions. Such locations are “classified,” and installation work must meet the requirements for that specific classified location.
Classification overview
Determining if certain areas are to be classified is the job of a team of professionals. Depending on needs, electrical and chemical engineers and design and operations personnel work together during the design process to classify the area. In addition, the likelihood of when, during system operation, the materials may be present in ignitable concentrations is also the job of the classification team. Area classification drawings are produced with detailed information that will later become valuable to workers in the field.
Chapter 5 of the NEC
The NEC allows for two different methods to classify hazardous locations based on the type of materials present in the same area as electrical equipment. In 1931, the Class/Division system (Division System) was introduced in the Code. In 1996, the International IEC Zone Classification system (Zone System) was introduced in the Code. See the “Codes Working Together for Safety” and “The Zone System of Classification” Sidebars at the end of the article. The systems are similar and perform the same purpose — fire and explosion prevention —but there is enough difference that they cannot be used interchangeably. The NEC forbids using both methods to classify the same location.
The Division system is laid out logically in the NEC (Fig. 1). You can find it in Art. 500 Hazardous (Classified) Locations, Classes I, II, and III, Divisions 1 and 2, which is sometimes referred to as the textbook for hazardous locations. It contains information regarding all three Classes and their Divisions with ample informational notes and examples of materials found in different groups.
The Division system divides materials into three different classes (with examples):
- Class I — flammable gases (acetylene) and flammable vapors produced from certain liquids (gasoline) and combustible vapors produced from liquids (diesel fuel). The main difference between a combustible and a flammable liquid is their flash point — the temperature at which a liquid gives off enough vapor to ignite in air. Flammable liquids reach their flash point at less than 100°F (37.8°C). Combustible liquids reach their flash point at temperatures equal to or greater than 100°F (37.8°C). Gasoline has a flash point of -50.8°F, making it flammable. Grade 2-D diesel fuel has a flash point of approximately 125°F to 160°F (52°C to 71°C) or more, depending upon composition. Thus, diesel fuel is combustible, and locations are typically not classified as hazardous.
- Class II — combustible dusts (aluminum dust, flour, grain). See Photo 1.
- Class III — combustible fibers/flyings or ignitable fibers/flyings (rayon, cotton, types of textile mill products, certain areas of woodworking facilities).
Within each Class, it must be determined if the material is expected during normal operation (Division 1) or only at certain times, such as maintenance (Division 2). Specific Code Articles then address each class.
- Article 501 Class I locations
- Article 502 Class II locations, and
- Article 503 Class III locations.
Article 504 [Intrinsically Safe Systems] provides installation rules for those systems where a spark or heat produced by this intrinsically safe equipment will not have enough energy to ignite a surrounding mixture.
Article 505 Zone 0, 1, and 2 locations is the alternative method to Area Classification. The Zone system classifies flammable gases, vapors, or liquids by Zone rather than Class and Division.
Article 506 Zone 20, 21, and 22 locations for combustible dusts or ignitable fibers/flyings is the Zone system providing an alternative method of classification for Class II (combustible dusts) and Class III (ignitible fibers) found in the Division system.
A set of NEC Articles for specific locations that are routinely constructed appears in Arts. 511 – 517. See Fig. 2.
The materials
Understanding NEC installation requirements means understanding the basics of the materials involved. For example, in a commercial garage, a light switch installed in a pit beneath the vehicle where the mechanic is making repairs is classified as Class I, Division 1 if gasoline or LPG vehicles are being serviced. However, if certain ventilation requirements are met, the pit may become a Class I, Division 2 location. Why? Gasoline vapors are three times heavier than air. LPG (mostly propane and butane) is approximately twice as heavy as air. These flammable vapors would then tend to accumulate in the pit. Ventilation would help minimize the concentration, thus dropping the classification to Division 2. The bottom line for the installer is the nameplate on the switch enclosure must specifically state it is applicable for Class I locations — then Division 1 or 2 as appropriate. Using an ordinary switch box in the enclosure is setting the area up for a fire or explosion.
NEC Sec. 500.6 [Materials] places materials into distinct groups based on their properties. The exception is Class III, which does not have any material groups assigned.
Class I materials with examples:
- Group A – Acetylene
- Group B – Hydrogen
- Group C – Ethylene
- Group D – Propane
Class II materials with examples:
- Group E – certain metal dusts, such as zirconium and uranium
- Group F – coal and coke dusts in specific concentrations
- Group G – Flour, grain, wood, plastics, and chemicals
The operating temperature of electrical equipment must not exceed the autoignition temperature of gases or vapors. The autoignition temperature is the minimum temperature required for ignition, and the operating temperature of electrical equipment must never be allowed to exceed this temperature. The NEC uses a set of Temperature Codes (T Codes) to simplify meeting this requirement. NEC Table 500.8(C)(4) Classification of Maximum Surface Temperature provides these T Codes.
Given the information above on the different materials, it only makes sense that enclosures, wiring devices, and wiring methods must be able to protect against hazards. The practical side for installation and maintenance is “read the nameplate.” The Class, Division, material group, and T Code will all be on the nameplate as applicable. Refer to area classification drawings as necessary and obtain engineering help if necessary, as shown in Photo 2.
Protection
Several techniques and methods are used to prevent ignitable materials from coming in contact with electrical ignition sources and will mitigate the results should an explosion occur within the equipment.
The most obvious method of protection is to simply remove the electrical equipment from the classified area. Since this is not always possible, other methods, such as ventilation to remove or reduce mixtures, proper grounding and bonding, the use of an intrinsically safe system, static protection, and automatic system shutdowns, are examples of various methods that can be used to prevent fire and explosion.
Beyond the above-listed methods, specially designed and constructed electrical equipment is used to provide protection.
Explosionproof equipment is not designed to prevent an explosion, but allows the explosion to occur within the enclosure and provide an escape route for the hot gases produced to escape into the surrounding classified location only after they are cooled below the temperature to cause ignition in that surrounding area (Photo 3).
Dust ignitionproof equipment is found in Class II, often Division 1 locations, and does not permit any heat generated inside the enclosure, such as from an electrical arc or spark, to cause ignition of specified dust in the vicinity of the equipment.
Dusttight enclosures do not allow dust to enter.
Purged and pressurized equipment maintains a positive pressure within the enclosure to prevent the entry of materials.
Nonincendive circuits, equipment, and components are found in Class I and Class II systems. They are low-energy and will not cause fire or explosion under specified conditions.
Oil immersion places electrical equipment in a protective liquid.
Hermetically sealed indicates electrical equipment sealed by the fusion of metal to prevent the entrance of external atmospheres.
Combustible gas detection systems utilize stationary gas detectors to provide input to control systems.
Different optical radiation protection techniques are needed because of the ignition danger posed by the use of fiber optics, optical communication equipment, LED lighting, and laser systems.
Skin effect trace heating “IEEE 844.1” is designed for heat trace systems that utilize a high-frequency AC to heat the surface of pipes and vessels.
The wiring methods for each Class and Division can be found in Secs. 501.10, 502.10, and 503.10 as applicable for the Class location.
Rigid metal conduit and MC-HL cable are common wiring methods in many locations. The NEC permits rigid and intermediate metal conduits in all locations.
MC-HL Metal Clad Hazardous Location cable requirements are found in Sec. 330.130 of Article 330 MC Cable. MC-HL cable is constructed of a gas/vapor-tight continuous corrugated metallic sheath, has an overall jacket of a polymeric material such as PVC, and must have a separate equipment grounding conductor, as shown in Photo 4.
A conduit seal fitting is used in electrical conduit runs to prevent the passage of gases, vapors, or flames through the conduit. To work effectively, always follow the manufacturer’s instructions when pouring sealing compound into the fitting. Seal location requirements are found in Sec. 501.15 [Sealing and Drainage], as shown in Fig. 5a and 5b.
Summary
Any installation or maintenance work in Hazardous (Classified) locations must meet the specific requirements found in Chapter 5 [Special Occupancies]. Article 500 provides much useful information. The individual Articles for each class then provide the specifics for Class I – gases and vapors, Class II – combustible dusts, and Class III – fibers/flyings. Protecting people and property from fire and explosions is what makes the proper installation and maintenance of hazardous (classified) equipment and systems necessary.
Codes Working Together for Safety
In March of 1937, a tragic explosion occurred at the New London School in New London, Texas. It is believed that a spark from a worker operating a switch ignited an accumulation of odorless natural gas in the building. At the time, requirements for electrical installations in “extra hazardous” locations, such as gas environments, were minimal. Natural gas is naturally odorless, and there were no requirements for the use of a gas additive for odorization purposes. Thus, an electrical spark was allowed to ignite the natural gas. An estimated 294 students and teachers died in the explosion.
States began to pass laws, the industry began to self-regulate, and today the Federal Pipeline Safety Regulations (49 CFR 192.625) provide minimum odorization requirements for natural gas. In addition to the National Electrical Code (NEC), the NFPA 54 Fuel Gas Code provides electrical requirements for grounding and bonding, electrical circuits, and electrical connections of gas piping installation. ANSI standards of the American Gas Association, the NFPA Codes, and the ICC Codes all work together to keep hazardous locations safe today.
The Zone System of Classification
The International IEC zone system of classification is another method of area classification provided in the NEC.
Article 505 Zone 0, 1, and 2 locations address flammable gases, vapors, and liquids.
In a Zone 0 location, ignitable concentrations of flammable gases or vapors are present continuously or for long periods. (The inside of a tank, for example)
A Zone 1 location is where ignitable concentrations exist under normal operating conditions or frequently, such as equipment requiring frequent maintenance.
A Zone 2 location is where ignitable mixtures are not normally present, but if they do exist, it would only be for a short period.
Material groups within this system are identified as IIA, IIB, and IIC. Equipment requirements, protection techniques, wiring methods, and seal fitting requirements are identified for different zones.
Article 506 Zone 20, 21, and 22 locations address combustible dusts or ignitable fibers/flyings.
A Zone 20 location is where ignitable concentrations of combustible dusts or ignitable fibers/flyings are present continuously or for long periods.
A Zone 21 location is where ignitable concentrations are likely to exist occasionally.
A Zone 22 location is where ignitable mixtures are not likely to occur, but if they do exist, it would only be for a short period.
Material groups within this system are identified as IIIA, IIIB, and IIIC. Equipment requirements, protection techniques, and wiring methods are identified for different zones.
About the Author
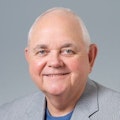
Randy Barnett
CESCP
Randy Barnett is an NFPA Certified Electrical Safety Professional, a long-time journeyman electrician, instructor and author with expertise in industrial electrical construction and maintenance. He is Electrical Codes & Safety Manager for NTT Training. Because of his ability to develop and deliver quality programs, Randy has trained more than 10,000 students in all 50 states, including Canada, Singapore, Afghanistan, Dubai, Trinidad, and Saudi Arabi. His articles appear in numerous trade publications and, his book on "Commercial and Industrial Wiring" is used as an entry-level text in many electrician training programs. Randy also appears at various corporate and trade association speaking engagements and consults on training program design and implementation. Randy is a graduate of the U.S. Navy Nuclear Power School, served as a nuclear electrician in submarines and holds a B.S. in business.