In order to create safe working conditions, OSHA and the NEC [110.26] provide working space requirements that vary according to the hazards involved with the installation and equipment. The NEC starts 110.26 by stating the space must be sufficient for “ready and safe operation and maintenance” of electrical equipment. This general statement applies to all electrical equipment. This single condition sets the stage for the more specific requirements found in 110.26.
When applying the requirements, the goal isn't to see what you can get by with. It's to protect people from injuries due to electric shock and arc blast/arc flash. Consequently, you may want to exceed the numbers given in 110.26 to satisfy the intent of this section. Think through the work processes that are likely to occur in the area. For example, is there enough room to safely use a lifting boom on that heavy breaker?
Requirement exceptions
Per 90.3, the working space requirements of 110.26 don't apply to equipment included in Chapter 8. Although signaling and communications equipment don't require a clear working space, they can't encroach on the working space of the electrical equipment.
The NEC doesn't require working space for the back or sides of an assembly where all connections and renewable or adjustable parts are accessible from the front [110.26(A)(1)(a)].
Where special permission is granted in accordance with 90.4, working space for equipment that operates at not more than 30VAC or 60VDC can be less than the distance in Table 110.26(A)(1) [110.26(A)(1)(b)]. Read the definition of “Special Permission” in Art. 100.
If you're replacing electrical equipment, you can apply Table 110.26(A)(1) Condition 2 working space requirements between dead-front switchboards, panelboards, or motor control centers located across the aisle from each other [110.26(A)(1)(c)] — but only if:
-
Width, depth, and height
Conditions of maintenance and supervision ensure that written procedures have been adopted to prohibit equipment on both sides of the aisle from being open at the same time, and
-
Only authorized, qualified persons will service the installation.
A common area of disagreement is the phrase “likely to require” in 110.26(A), which says, “Equipment that is likely to require examination, adjustment, servicing, or maintenance while energized must have sufficient working space in accordance with (1), (2), and (3)….” Get clarification on what “likely to require” means from the Authority Having Jurisdiction (AHJ).
In all cases, the working space must be of sufficient width, depth, and height to permit all equipment doors to open 90° [110.26(A)(2)].
The width of the working space must be a minimum of 30 in., but in no case less than the width of the equipment.
You can measure the width of the working space from left to right, from right to left, or simply centered on the equipment. The working space for one piece of equipment can overlap the working space for other electrical equipment (Fig. 1 on page 32).
See Table 110.26(A)(1) for the minimum depth required of a specific application — it's not always 3 ft. For example, it's 4 ft at a 480V motor control center (MCC) with exposed live parts on both sides of the working space.
“Headroom” is another way we refer to the height of a working space. For service equipment, switchboards, panelboards, and motor control equipment, the headroom in front of equipment must be at least 6½ ft, measured from the grade, floor, or platform [110.26(E)]. For equipment more than 6½ ft in height, the headroom can't be less than the height of the equipment.
Exception: The minimum headroom requirement doesn't apply to service equipment or panelboards rated 200A or less in an existing dwelling unit. See the definition of “Dwelling Unit” in Art. 100.
Equipment such as raceways, cables, wireways, cabinets, and panels can be above or below electrical equipment, but must not extend more than 6 in. into the equipment working space [110.26(A)(3)] (Fig. 2).
Clear spaces
Working space covered by 110.26 must be clear at all times [110.26(B)]. Therefore, it can't double as a storage area. It's dangerous to service energized parts in the first place. It's unacceptable to subject electrical workers to the additional dangers of working around boxes, cabinets, and other impediments in their working space.
When normally enclosed live parts are exposed for inspection or servicing in a passageway, the working space must be suitably guarded from occupants using the passageway. Make allowances for a fire alarm evacuation, which will have numerous occupants moving through the passageway.
Entrance and egress
At least one entrance/egress of sufficient area must provide access to and egress from the working space [110.26(C)(1)]. Building codes contain minimum dimensions for doors and openings for personnel travel. Check with the AHJ for clarification of “sufficient area.”
You must have an entrance to and egress from the working space at each end of the working space of electrical equipment rated 1,200A or more, if the equipment is over 6 ft wide [110.26(C)(2)]. The openings must be not less than 24 in. wide and 6½ ft high. You can have a single entrance/egress, if:
-
The location permits a continuous and unobstructed way of egress travel, or
-
The required working space depth is doubled, and the equipment is located so the edge of the entrance is no closer than the required working space distance.
Fig. 4. Guidelines on installing foreign systems.
Where equipment with overcurrent or switching devices rated 1,200A or more is installed, personnel door(s) for entrance to and egress from the working space located less than 25 ft from the nearest edge of the working space must have the door(s) open in the direction of egress and be equipped with panic hardware or other devices that open under simple pressure [110.26(C)(3)]. This applies only to doors that are intended to provide an entrance or exit from the equipment room, so it doesn't apply to unrelated doors that are within 25 ft, such as a door leading to a janitor's closet. In addition, notice that while the requirement for two entrances/exits is dependent on the amperage and the physical size of the equipment, this rule applies regardless of the physical width.
Electricians who suffer burns on their hands in electrical arc flash or arc blast events often can't open doors equipped with knobs that must be turned, and they can't pull a door that opens toward them. Because this requirement is in the NEC, the electrical contractor is responsible for ensuring that panic hardware is installed where required. Some electrical contractors chafe at being held liable for nonelectrical responsibilities, but this rule exists to save the lives of electricians.
Illumination
Service equipment, switchboards, panelboards, and MCCs located indoors must have illumination in (or next to) the working space [110.26(D)]. Illumination must not be controlled by automatic means only.
The NEC doesn't provide the minimum footcandles required for proper illumination, but lighting application guides do. Proper illumination of electrical equipment rooms is essential for the safety of those working on such equipment.
Saving a few bucks on installed lighting only to incur the costs of temporary lighting or extended downtime later isn't good economics, but this isn't just a matter of economics. The safety issue makes good lighting not only sensible, but also imperative.
Dedicated space
Switchboards, panelboards, and MCCs must have dedicated equipment space and be protected from damage [110.26(F)].
Outdoor equipment must comply with 110.26(F)(2). For indoor equipment, the following requirements apply:
-
The footprint space (width and depth of the equipment) extending from the floor to a height of 6 ft above the equipment, or to the structural ceiling (whichever is lower), must be dedicated for the electrical installation. You cannot install any piping, ducts, or other equipment foreign to the electrical installation in this dedicated footprint space (Fig. 3).
-
Exception: Suspended ceilings with removable panels can be within the dedicated footprint space [110.26(F)(1)(d)].
-
Electrical raceways and cables not associated with the equipment in the dedicated space can still be located within the dedicated space. These aren't considered “equipment foreign to the electrical installation.”
-
Foreign systems can be located above the dedicated space if protection is installed to prevent damage to the electrical equipment from condensation, leaks, or breaks in the foreign systems (Fig. 4).
-
Sprinkler protection piping isn't permitted in the dedicated space, but the NEC doesn't prohibit sprinklers from spraying water on electrical equipment.
-
A dropped, suspended, or similar ceiling isn't considered a structural ceiling.
Electrical equipment rooms and enclosures housing electrical equipment or apparatus controlled by locks are considered accessible to qualified persons who require access [110.26(G)].
See the definition of “Accessible as it applies to equipment” in Art. 100.
Now you can answer the question of how much working space is enough — and you know that the correct answer depends on what space you're talking about, what equipment is in that space, and other factors. The distance tables in OSHA and in 110.26 are starting points, not maximums.
What you're really trying to do is ensure that the space around the equipment doesn't prevent the safe operation and maintenance of that equipment. Meet that goal, and you'll satisfy OSHA, the NEC, and your insurance company. None of these are concerned, however, with the efficiency of maintenance and operation.
Often, people want to reduce working space in a misguided effort to maximize revenue per square foot for the facility. The reality is that you maximize revenue per square foot only when you allow enough space for efficient operation, maintenance, and repair.
About the Author
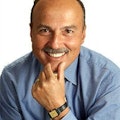
Mike Holt
Mike Holt is the owner of Mike Holt Enterprises (www.MikeHolt.com), one of the largest electrical publishers in the United States. He earned a master's degree in the Business Administration Program (MBA) from the University of Miami. He earned his reputation as a National Electrical Code (NEC) expert by working his way up through the electrical trade. Formally a construction editor for two different trade publications, Mike started his career as an apprentice electrician and eventually became a master electrician, an electrical inspector, a contractor, and an educator. Mike has taught more than 1,000 classes on 30 different electrical-related subjects — ranging from alarm installations to exam preparation and voltage drop calculations. He continues to produce seminars, videos, books, and online training for the trade as well as contribute monthly Code content to EC&M magazine.