The Differences Between Grounding and Bonding ― Part 5 of 12
Courtesy of www.MikeHolt.com.
This article is the fifth in a 12-part series on the differences between grounding and bonding.
Let us start our discussion by focusing on the bonding requirements for services.
The metal parts of raceways and/or enclosures containing service conductors must be bonded together [Sec. 250.92(A)]. Use bonding jumpers around reducing washers and ringed knockouts for service raceways (Fig. 1). You can use standard locknuts to make mechanical connections to raceways, but you cannot use them as the bonding means [Sec. 250.92(B)].
Ensure service bonding by one of these methods [Sec. 250.92(B)]:
(1) Bond metal parts to the service neutral conductor. A main bonding jumper is required to bond the service disconnect enclosure to the service neutral conductor [Sec. 250.24(B) and Sec. 250.28]. At the service disconnect enclosure, the service neutral conductor provides the effective ground-fault current path to the power supply [Sec. 250.24(C)]; therefore, you don’t have to install a supply-side bonding jumper in PVC conduit containing service-entrance conductors [Sec. 250.142(A)(1) and Sec. 352.60, Exception No. 2].
(2) Terminate metal raceways to threaded couplings or listed threaded hubs.
(3) Terminate metal raceways to threadless fittings.
(4) Use listed devices, such as bonding-type locknuts, bushings, wedges, or bushings with bonding jumpers to the service neutral conductor. A listed bonding wedge or bushing with a bonding jumper to the service neutral conductor is required when a metal raceway containing service conductors terminates to a ringed knockout.
A supply-side bonding jumper of the wire type used for this purpose must be sized per Table 250.102(C)(1), based on the size/area of the service phase conductors within the raceway [Sec. 250.102(C)]. A bonding-type locknut, bonding wedge, or bonding bushing with a bonding jumper can be used for a metal raceway that terminates to an enclosure without a ringed knockout.
A bonding locknut differs from a standard locknut in that it contains a bonding screw with a sharp point that drives into the metal enclosure to ensure a solid connection. Bonding one end of a service raceway to the service neutral provides the necessary low-impedance fault current path to the source.
Bonding communications systems
A bonding termination device must be provided for communication systems [Art. 805], radio and TV equipment [Art. 810], CATV [Art. 820] and similar systems [Sec. 250.94]. You bond these different systems together to minimize voltage differences between them.
An intersystem bonding termination device must meet all the following requirements [Sec. 250.94(A)]:
(1) Be accessible.
(2) Have a capacity for at least three intersystem bonding conductors.
(3) Be installed so it does not interfere with the opening of any enclosure.
(4) Be securely mounted and electrically connected to the service disconnect, meter enclosure, or grounding electrode conductor (GEC).
(5) Be securely mounted and electrically connected to the building’s disconnect or GEC.
(6) Be listed as grounding and bonding equipment.
Exception: An intersystem bonding termination device is not required where communications systems are not likely to be used.
An “Intersystem Bonding Termination” is a device that provides a means to connect communications systems’ (twisted wire, antennas, and coaxial cable) bonding conductors to the building grounding electrode system [Art. 100] (Fig. 2).
Bonding metal parts
Metal parts intended to serve as the equipment grounding conductors (EGCs) must be bonded together to ensure they can safely conduct any fault current likely to be imposed on them [Sec. 110.10, Sec. 250.4(A)(5), Sec. 250.96(A), and Table 250.122 Note].
Nonconductive coatings (such as paint) must be removed to ensure an effective ground-fault current path, or the termination fittings must be designed so removal is unnecessary [Sec. 250.12].
Bonding 277V and 480V circuits
Metal raceways or cables containing 277V or 480V circuits terminating at ringed knockouts must be bonded to the metal enclosure with a bonding jumper sized per Sec. 250.122 [Sec. 250.102(D)].
Where oversized, concentric, or eccentric knockouts are not encountered, or where a box or enclosure with concentric or eccentric knockouts is listed to provide a reliable bonding connection, a bonding jumper is not required. But you must use one of the methods listed in the Exception to Sec. 250.97. For example, use two locknuts on rigid metal conduit or intermediate metal conduit — one inside and one outside of boxes and cabinets.
Equipment bonding jumpers must terminate by any of the eight means listed in Sec. 250.8 [Sec. 250.102(B)]. These include listed pressure connectors, terminal bars, and exothermic welding.
Supply-side bonding jumper sizing
Supply‑side bonding jumpers must be sized per Table 250.102(C)(1), based on the size/area of the phase conductor within the raceway or cable [Sec. 250.102(C)(1)].
If the phase supply conductors are paralleled in two or more raceways or cables, size the supply‑side bonding jumper for each per Table 250.102(C)(1), based on the size/area of the phase conductors in each raceway or cable [Sec. 250.102(C)(2)].
A single supply-side bonding jumper installed for bonding two or more raceways or cables must be sized per Table 250.102(C)(1), Note 3, based on the equivalent area of the supply-side phase conductors [Sec. 250.102(C)(2)].
Let’s take a look at an example to help clarify these requirements.
Question: What size supply‑side bonding jumper is required for three metal raceways, each of which contain 400kcmil service conductors?
Answer: As per Sec. 250.102(C)(2) and Table 250.102(C)(1), you need a 1/0 AWG supply-side bonding jumper for each raceway. A single supply-side bonding jumper is permitted for multiple raceways based on the equivalent area of the supply-side phase conductors.
Load-side bonding jumper sizing
Size bonding jumpers on the load side of feeder and branch‑circuit overcurrent devices per Sec. 250.122 [Sec. 250.102(D)].
Let’s examine another example to help clarify these requirements.
Question: What size equipment bonding jumper is required for each metal raceway where the circuit conductors are protected by a 1,200A overcurrent protective device (OCPD)?
Answer: If you use a single bonding jumper to bond two or more metal raceways, size it per Sec. 250.122, based on the rating of the largest circuit OCPD. In this case, a quick check of Table 250.122 shows us that a 3/0 AWG equipment bonding jumper is required (Fig. 3).
Bonding piping systems and exposed structural metal
Electrically continuous metal water piping must be bonded to one of the following [Sec. 250.104(A)(1)]:
(1) Service-disconnect enclosure
(2) Service neutral conductor
(3) GEC, if of sufficient size
(4) One of the grounding electrodes of the grounding electrode system if the GEC or bonding jumper to the electrode is of sufficient size
The metal piping system bonding jumper must be copper if within 18 in. of the surface of earth [Sec. 250.64(A)] and adequately protected if exposed to physical damage [Sec. 250.64(B)].
A ferrous metal raceway containing a GEC must be made electrically continuous by bonding each end of the raceway to the GEC [Sec. 250.64(E)]. The points of attachment must be accessible.
Size metal water piping system bonding jumpers per Table 250.102(C)(1), based on the size/area of the service phase conductors. These are not required to be larger than 3/0 copper or 250kcmil aluminum or copper-clad aluminum, except as permitted in Sec. 250.104(A)(2) and (A)(3).
Bonding is not required for isolated sections of metal water piping connected to a nonmetallic water piping system. In fact, these isolated sections of metal piping should not be bonded because they could become a shock hazard under certain conditions.
When an electrically continuous metal water piping system in an individual occupancy is metallically isolated from other occupancies in a building, the metal water piping system for that occupancy can be bonded to the equipment grounding terminal of the occupancy’s switchgear, switchboard, or panelboard. Size the bonding jumper based on the rating of the circuit OCPD per Sec. 250.102(D) [Sec. 250.104(A)(2)].
The metal water piping system of a building supplied by a feeder must be bonded to one of the following:
(1) The equipment grounding terminal of the building’s disconnect enclosure.
(2) The feeder equipment grounding conductor.
(3) One of the building’s grounding electrodes of the grounding electrode system if the grounding electrode or bonding jumper to the electrode is of sufficient size.
Size the bonding jumper per Sec. 250.102(D), but it’s not required to be larger than the largest feeder phase or branch-circuit conductor supplying the building.
Other metal‑piping systems in or attached to a building must be bonded [Sec. 250.104(B)]. The piping is considered bonded when it is connected to an appliance that is connected to the circuit equipment grounding conductor.
Informational Note 1: Bonding all metal piping and metal air ducts will provide additional safety.
Informational Note 2: Further information can be found in NFPA 54, The National Fuel Gas Code, and NFPA 780, Standard for the Installation of Lightning Protection Systems.
Exposed structural metal that is interconnected to form a metal building frame must be bonded to one of the following [Sec. 250.104(C)]:
(1) The service-disconnect enclosure.
(2) The neutral at the service disconnect.
(3) The building’s disconnect enclosure for those supplied by a feeder.
(4) The GEC where of sufficient size.
(5) One of the grounding electrodes of the grounding electrode system if the GEC or bonding jumper to the electrode is of sufficient size.
Author’s comment: This requirement does not apply to metal framing members (such as metal studs) or the metal skin of a building.
Metal water piping systems and structural metal interconnected to form a building frame must be bonded to the transformer secondary winding per Sec. 250.104(D)(1) through (D)(3). For example, exposed structural metal used this way in the area served by a transformer must be bonded to the secondary neutral conductor where the GEC is connected at the transformer [Sec. 250.104(D)(2)].
Exception No. 1: Bonding to the transformer is not required if the metal structural frame serves as the grounding electrode [Sec. 250.52(A)(2)] for the transformer.
Don’t be the one at fault
With all the details involved, an omission or oversight is likely when bonding for fault current. That could result in tragic consequences.
Try this verification method. On an installation drawing, mark all the points where a bonding jumper should provide a fault path back to the source. Then walk down the installation with that drawing and markup what is missing.
These materials are provided to us by Mike Holt Enterprises in Leesburg, Fla. To view Code training materials offered by this company, visit www.mikeholt.com/code.About the Author
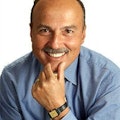
Mike Holt
Mike Holt is the owner of Mike Holt Enterprises (www.MikeHolt.com), one of the largest electrical publishers in the United States. He earned a master's degree in the Business Administration Program (MBA) from the University of Miami. He earned his reputation as a National Electrical Code (NEC) expert by working his way up through the electrical trade. Formally a construction editor for two different trade publications, Mike started his career as an apprentice electrician and eventually became a master electrician, an electrical inspector, a contractor, and an educator. Mike has taught more than 1,000 classes on 30 different electrical-related subjects — ranging from alarm installations to exam preparation and voltage drop calculations. He continues to produce seminars, videos, books, and online training for the trade as well as contribute monthly Code content to EC&M magazine.