With the 2020 revision of the NEC, Art. 242 replaced two individual Articles that appeared in earlier editions of the Code — Art. 280 [Surge Arrestors] and Art. 285 [Transient Voltage Surge Suppressors (TVSSs)]. Implementing a good strategy for overvoltage protection encompasses the material contained in both of those prior Articles.
Part I of Art. 242 provides the general, installation, and connection requirements for overvoltage protection and overvoltage protective devices (i.e., surge protective devices or SPDs). Part II covers SPDs rated 1,000V or less that are permanently installed on premises wiring systems. Part III covers surge arresters permanently installed on premises wiring systems over 1,000V nominal.
It will bring you to tiers
Distribution step-down transformers do not filter out transients. They reduce transients by the same proportion they step down the line voltage. For example, a 480V/120V delta/wye transformer has a 4 to 1 turns ratio, which means a 1,800V spike coming into that transformer will translate to a 450V spike on the other side of it.
It helps to think of power distribution voltage levels as a series of layers that get smaller as you go from the source to the point of use. We start with the higher voltages and further break down voltage levels into what we call a tiered protection strategy.
SPDs are designed to reduce transient voltages present on premises power distribution wiring and load-side equipment. These transient voltages can originate from sources ranging from lightning to laser printers. Voltage spikes and transients that are caused by the switching of utility power lines, power factor correction capacitors, or lightning can reach thousands of volts and amperes. Voltage spikes and transients that are caused by utilization equipment such as photocopiers, laser printers, and other highly reactive loads can be in the hundreds of volts.
Transients produced by utilization equipment are the typical culprits when you have frequent failures of electronic equipment such as computers, telecommunications equipment, security systems, and electronic appliances.
An SPD limits transient voltages by diverting or limiting surge current and preventing the continued flow of current while remaining capable of repeating these functions [Art. 100].
A key concept in the application of these devices is they limit transient voltages rather than eliminate them. How much a particular device limits transient voltages depends on which level of power distribution and environment it is designed for.
A given SPD device can limit voltage only within a certain range. That’s why a tiered system is necessary. The first SPD device downstream of the disturbance handles the voltage down to something on par with that level of voltage distribution. This continues for as many levels as needed until you’re at the branch circuit SPD, which can’t possibly handle the original transient but can easily handle what the other SPDs have passed to it.
Prohibited uses
You cannot use an SPD [Sec. 242.6]:
(1) In circuits that exceed 1,000V.
(2) In ungrounded systems, impedance grounded systems, or corner-grounded delta systems unless listed specifically for use on these systems.
(3) If the voltage rating of the SPD is less than the maximum continuous phase-to-ground voltage available at the point of connection.
SPD requirements
SPDs must be listed [Sec. 242.8]. UL 1449, Standard for SPDs, says these units are intended to limit the maximum extent of transient voltage surges on power lines to specified values. They are not intended to function as lightning arresters.
SPDs are susceptible to failure at high fault currents. SPDs must be marked with their short-circuit current rating. You cannot install an SPD where the available fault current exceeds its rating [Sec. 242.10].
Where you use SPDs, ensure each phase conductor of the SPD-protected circuit is connected [Sec. 242.20]. If the SPD comes as a 3-phase system in a box, simply connect the phase wires of the SPD to the electrical system’s phase wires. Otherwise, you will probably be connecting an individual SPD between any two conductors (whether ungrounded or grounded). A grounded conductor and the equipment grounding conductor can be interconnected only by the normal operation of the SPD during a surge [Sec. 242.30].
Line and grounding conductors must be at least 14 AWG (12 AWG if aluminum) [Sec. 242.28]. Connect only one conductor to a terminal, unless the terminal is identified for multiple conductors [Sec. 110.14(A)]. Don’t make the leads any longer than necessary, and avoid bends that are sharp or unnecessary [Sec. 242.24] (Fig. 1). Shorter conductors and minimal bends improve SPD performance by helping to reduce conductor impedance during high-frequency transient events.
Types 1, 2, 3, and 4
SPD types are numbered from the service (Type 1), feeder (Type 2), branch circuits (Type 3) to components integrated into the equipment (Type 4). As the energy level decreases, the Type number increases. For that reason, using each Type in a tiered strategy is the only way to effectively protect infrastructure and loads from transients.
Here is a more detailed explanation of the tiers.
Type 1 SPDs normally go on the supply side of the service disconnect [Sec. 242.12(A)(1)]. However, you can install them on the load side of the service disconnect per the requirements of Sec. 242.14 [Sec. 242.12(A)(2)] (Fig. 2). For example, you might want to use a Type 1 SPD on a particular feeder that supplies a large motor.
Type 2 SPDs must be connected to the load side of the service disconnect [Sec. 242.14(A)] rather than the supply side. You can connect them anywhere on the load side of the feeder overcurrent protective device [Sec. 242.14(B)] and you can connect them anywhere on the premises wiring of a separately derived system [Sec. 242.14(C)].
Type 3 SPDs must be connected somewhere on the load side of branch circuit protection [Sec. 242.16], and their application stops at the equipment served.
Type 4 SPDs are installed in the equipment served, and can be installed only by the equipment manufacturer [Sec. 242.18]. A common scheme is metal oxide varistors (MOVs) connected between each power input line and ground. You may see these, for example, inside a case power supply. They shunt the remaining overvoltage out of the power line. However, they are easily destroyed if the incoming voltage exceeds their rating. Proper application of Types 1, 2, and 3 upstream of the MOV-protected equipment is essential.
Effective protection
Your transient protection system needs to consist of layers of transient shields, each one at a lower energy level as you peel back another layer of the transient protection onion. The idea is to keep knocking down the voltage level of the transient.
Correctly select the SPDs that will most economically and effectively protect your branch circuits and their loads.
These materials are provided by Mike Holt Enterprises in Leesburg, Fla. To view Code training materials offered by this company, visit www.mikeholt.com/code.
About the Author
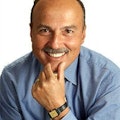
Mike Holt
Mike Holt is the owner of Mike Holt Enterprises (www.MikeHolt.com), one of the largest electrical publishers in the United States. He earned a master's degree in the Business Administration Program (MBA) from the University of Miami. He earned his reputation as a National Electrical Code (NEC) expert by working his way up through the electrical trade. Formally a construction editor for two different trade publications, Mike started his career as an apprentice electrician and eventually became a master electrician, an electrical inspector, a contractor, and an educator. Mike has taught more than 1,000 classes on 30 different electrical-related subjects — ranging from alarm installations to exam preparation and voltage drop calculations. He continues to produce seminars, videos, books, and online training for the trade as well as contribute monthly Code content to EC&M magazine.