Developing a Safety Culture in Your Business
Developing a Safety Culture in Your Business
May 1, 1999 12:00 PM, By Mark Lamendola, Technical Editor
Safety depends on individual decisions, not luck. How do you successfully encourage individuals to make the right decisions?
Whose responsibility is safety? How do you reduce personal injuries and their impact on your bottom line (and your peace of mind)? People cause injuries; people can prevent them. Thus, you must train and lead people into safe behavior. This is the essence of developing a safety culture; an environment in which people consciously seek safe ways to work.
You've probably tried logos, signs, meetings, awards, programs, supervisor intervention, monetary incentives, and even disciplinary action. Since these tools don't fix the underlying problems, companies who place all their faith in them continue to have poor safety records. But some companies have outstanding safety records. What's their secret? They plan according to the adage: "If you fail to plan, you plan to fail." They have planned for, and achieved, a safety culture that pervades the business.
The futility of enforcement. What happens when you have safety enforcement rather than a safety culture? People then play "fool the enforcer." In this no-win game, people say to each other, "Here comes the boss, better put on your safety glasses." Your goal is for the worker to say, "This could expose my eyes to injury. I'll put on my safety glasses."
Sometimes people change positions suddenly, to avoid being caught doing something unsafe. People rearrange the materials or tools they are working with, stop what they are doing, or leave temporarily. They may attach grounds or lockouts they should have attached before starting. These are the useless results of safety enforcement. A safety program won't fix this; it is a tool you use to fix this. Let's begin by looking at safety basics that culture must embrace.
Personal Protective Equipment (PPE). Before beginning a task, ask, "What body parts might I expose to danger?" Then you select the proper PPE to protect those body parts. Many people play a game in which managers try to make workers wear PPE, and workers find ingenious ways not to wear PPE. In fact, it is the job of every manager to teach each employee that you wear PPE to protect not only your ability to earn a living, but to enjoy life. This teaching is an ongoing process of training and reinforcement.
The cost of providing PPE pales next to the expense and pain of an injury. Give employees a clear message on safety. Do some employees waste or steal ear plugs? Don't remove earplug dispensers; hold users accountable for maintaining the supply. Rather than penalize people for damaged or lost safety glasses, counsel them on proper care; provide a sliding co-payment based on normal wear and tear. The bottom line is: Encourage personal responsibility for PPE without being onerous. (See the article, "Protective Equipment: Up Front And Personal," in this issue, for more detailed information on PPE.)
Positions of people. Positions of people can cause injuries. You can strike against an object (like a sharp corner table), or be struck by an object (like a falling box). Do you route cords to prevent tripping hazards? Do you clean up spills immediately? If you reach for one carton, are you going to pull another down on top of you? When you tighten a lug, are your knuckles in line with sharp edges? Where is your body in relation to the objects around, above, and below you? Looking at the Photo (on page 44 of the original article), notice how each worker pays close attention to potential safety hazards in his work area.
You can fall to the same level or to a lower level. You can fall into something or you can fall off of something. Ladder safety is fertile ground for injury reduction. A person with a mentality of "it can't happen to me" is dangerous to everyone. If that person is on a ladder, beware of falling objects and falling people. You can be caught in, on, or between objects. When setting a 200 hp motor in place, are you placing your hands between it and the mounting pad? When a lift truck backs across your path, do you walk behind it or wait for the operator to finish the maneuver?
How do you keep from contacting temperature extremes? Before gripping an unfamiliar pipe, touch the surface lightly with your fingertips. Wear the right gloves and use the recommended tools, whether freeze-fitting bearings or taking a voltage measurement. When welding, an apron and gloves reduce burn hazards. Assume an unknown object is too hot or cold, and plan accordingly. How serious are you about lockout/tagout? Do you know the OSHA standards? Do you have a copy of OSHA Paragraph 1910.331-1910.398? Do you regularly read sources of safety information?
You can reduce inhaling, absorbing, and swallowing dangers through proper use of PPE, but also consider all possible means of containing any dangerous substances. How can you prevent a spill, leak, or splash? Do your procedures help reduce these hazards?
Overexertion often results in muscular or thermal exhaustion; but lifting too much weight can tear tendons from the bone, and introduce bone fragments into soft tissue. Once damaged, tendons and ligaments heal slowly and often cause "domino" or "secondary" injuries that would not have happened without the original injury.
Even when the weight is light, you can injure yourself if you don't use proper lifting techniques or muscle preparation. Most people know about "bend at your knees, not at your waist," yet they are still at high risk of lifting-related injury because of poor preparation. (See sidebar)
Tools and equipment. Here are three ways people use tools improperly:
- The tool is wrong for the job
- The person is using the tool incorrectly
- The tool is in an unsafe condition.
Using a screwdriver as a pry bar, pulling a knife toward you, and using damaged meter leads are examples. You can drastically reduce injuries just by asking people to explain why they are using a tool in a certain way. Encourage employees to replace worn or broken tools voluntarily. The price of replacing a mushroomed hammer or damaged saw blade is trivial compared to a broken or severed finger.
Procedures and orderliness. There are three reasons why people don't follow procedures. For these reasons, they may also not work in an orderly fashion or practice good housekeeping:
- The procedures are inadequate in content or writing method.
- People don't know or understand the procedures.
- People consciously decide not to follow the procedures.
Ensure your procedures address your situations. Write them clearly and concisely. Use clear verb-noun headings like "lockout energy sources." Check procedures by physically walking through them. Audit them on a predetermined schedule to ensure they remain germane.
Routinely coach employees on procedures and policies. Posting a different procedure in a visible place each week is one way to do this. Another is to include a safety reminder, such as "Never stand on a stepladder's top step" in pay envelopes. You can buy ready-made materials, and you can find sources in EC&M's ads.
Whatever method you use, change its timing, delivery, and content frequently or people will stop paying attention to the message. Don't stop giving the message, or you give an unintended message that safety thoughts need not be present.
If you take care of the first two problems, people will follow procedures once they clearly understand their importance. A safety culture is the most, if not only, effective means of making sure this happens.
How to build a safety culture. Building a safety culture is not a safety function, but a project management function. And no safety director can do it alone (see sidebar, on page 50). Sometimes, you must hammer your point home. A new maintenance manager encountered an entrenched tradition of not wearing safety glasses. His new safety glass policy didn't require anyone to wear safety glasses. However, those who chose not to wear them had to stand up at the weekly shift meeting and tell the group how they planned to make a living with no eyesight. The result: Everyone wore his or her safety glasses without being reminded.
Use this approach for safety. However you manage your other projects, you need to build a safety culture in a particular way. Consider the ATTAM approach: Assess, Train, Teach, Assign, and Monitor.
Assess. Observe people working, and take notes. What are the recurring unsafe acts? Record each unsafe act as it occurs. Once employees notice you in an area, they put on a face of safety and limit your ability to observe. That's the time to ask, "Why are these unsafe acts occurring?"
Assess your people to determine who can champion the correcting of attitudes, behavior, and ignorance. Who are the key players? Usually, they are crew leaders, supervisors, and others with authority. Identify the people, then identify their attitudes and basic safety knowledge.
Train. Once you've selected your safety champions, you must do more than just tell them, "Now I am making safety part of your performance evaluation." They must learn the causes of injury and alternatives to practicing those causes. You must train everyone that safety is equal to or greater than all other goals, including production. Safety champions are teachers, but they are only as effective as their training and the backing of management allow them to be. Consider purchasing "train the trainer" safety programs.
Teach. Your trained safety champions teach safety to the rest. The simple teaching method has three parts. First, stop when you enter an area. Scan the area, then look, listen, smell, and feel for unsafe conditions. Look for such things as improper tool use. Listen for high ambient noise. Smell for gasoline fumes. Feel for high heat.
When you notice an unsafe act, approach the worker, making him or her aware of the unsafe practice. Then you must follow up to ensure that worker corrects it. You also teach by looking for safe acts. For example, if you see an employee working overhead and wearing a safety belt, let that person know you recognize and appreciate his or her attention to safety.
Assign. Some unsafe acts wouldn't happen if you could correct environmental problems. For this, you must hold individuals responsible. If it's nobody's job, nobody will do it. Make specific work assignments and hold individuals accountable for certain safety objectives.
- Assign individuals to inspect equipment and work areas for problems such as poor lighting, missing guards, damaged equipment.
- Assign ownership of an individual problem to an individual (who may lead a group in resolving it).
- Assign individual safety ownership of specific power distribution equipment, so such activities as breaker testing and transformer inspection actually happen.
- Assign someone to audit inspections, safety tours, safety meetings, and other activities.
Monitor. Check your safety culture progress by asking key questions. How are employees responding? How are your teachers carrying out their duties? Do they need more training? What are the recurring types of unsafe behavior? When did you last observe people working? Are safety inspection reports precipitating action? Is it easy to report unsafe conditions or equipment? Are you replacing unsafe equipment? Are you rewarding your employees for safe or unsafe acts?
Everything boils down to two questions:
- Do your employees know how much you value safe behavior?
- Are you sure you want them to know?
Suggested Reading Electrical Safety for Construction Sites OSHA Electrical Work Rules. For ordering information, call 800-543-7771.
EC&M Books:
Other resources: Cadick, John, Electrical Safety Handbook, McGraw-Hill, 1994. Document # MS-02723, E.I. duPont de Nemours Company, 1992.
Sidebar: Warming Up to Safety
According to Sandy Miller, a personal trainer and former bodybuilder in Overland Park, Kans.: "You should warm your muscles up prior to any exercise, no matter how strong you are or how much you can lift. The body isn't a machine with an instant-on button. Even a 5-sec stretch can mean the difference between injury and safety." So if you're going to pull 500MCM cable or wrestle a 30kVA transformer, stretch your muscles (especially your back and shoulders) for a few seconds beforehand.
Miller also says, "Stretching alone is helpful, but you really should ensure your muscles are warm and you've got some blood flowing." You can warm up by practicing the lift, but with no weight. Some exercises for muscle-warming include 5 min of walking, 1 min of stair-climbing, or 3 min of sit-ups. Once you warm up, you are generally "good for the day" if you stay active. Warming up your body is similar to warming up your car engine; if you park too long, it won't be warm when you go to start it again.
Sidebar: A Team Effort
Mike Ellis, a veteran safety manager in Owensboro, Ky., says: "Anyone who says 'I can make a plant safe' doesn't know what he's talking about. If he says 'we can make this plant safe,' then he's got something."
Ellis trains managers to "put the personal touch" on safety. Supervisors look for unsafe acts when entering a work area. If they spot someone not practicing safety, they ask that person to stop working and analyze the situation. This requires personal attention, but Ellis explains, "so does notifying the next of kin."
However, sometimes this approach isn't enough. Ellis says, "It works at least 99% of the time. Most people have good sense. If you approach them with that in mind, they try hard to be safe. If you lecture them, they may incorrectly see unsafe acts as a way of asserting their independence. Unfortunately, there's no dignity in being electrocuted or losing an eye."
About the Author
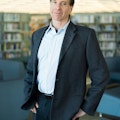
Mark Lamendola
Mark is an expert in maintenance management, having racked up an impressive track record during his time working in the field. He also has extensive knowledge of, and practical expertise with, the National Electrical Code (NEC). Through his consulting business, he provides articles and training materials on electrical topics, specializing in making difficult subjects easy to understand and focusing on the practical aspects of electrical work.
Prior to starting his own business, Mark served as the Technical Editor on EC&M for six years, worked three years in nuclear maintenance, six years as a contract project engineer/project manager, three years as a systems engineer, and three years in plant maintenance management.
Mark earned an AAS degree from Rock Valley College, a BSEET from Columbia Pacific University, and an MBA from Lake Erie College. He’s also completed several related certifications over the years and even was formerly licensed as a Master Electrician. He is a Senior Member of the IEEE and past Chairman of the Kansas City Chapters of both the IEEE and the IEEE Computer Society. Mark also served as the program director for, a board member of, and webmaster of, the Midwest Chapter of the 7x24 Exchange. He has also held memberships with the following organizations: NETA, NFPA, International Association of Webmasters, and Institute of Certified Professional Managers.