Troubleshooting Voltage Sags and Swells
A steady supply of voltage is important in industrial and commercial applications to maintain equipment performance, product quality, and safety, while also minimizing downtime. Voltage sags (where the expected voltage dips 10% below the expected range) or swells (where voltage jumps 10% above the expected range) can cause problems throughout facilities. In this article, we’ll discuss steps to effectively troubleshoot voltage sags and swells.
What are symptoms of voltage sags or swells?
Voltage sags and swells manifest in many ways. Lighting circuits can be impacted, which workers may notice as annoying flickering or even lighting levels dropping to unsafe levels. Equipment with electronic power supplies may reset, and processes requiring use of motors could fail or experience production errors due to loss in motor torque.
The impact of voltage sags and swells on processes and components
Sensitive electronics operate using electronic power supplies that require peak voltages to be within an optimal range to operate properly. Voltages that are either too low or too high can damage power supplies or cause equipment to shut down, restart, or operate at reduced performance levels. While events of short duration tend to have less impact on system performance, longer events can impact power supply performance and prevent equipment from operating.
If problems with sags and swells aren’t addressed, out of warranty repairs could become common, decreasing available capital for other products. Motors could also suffer reduced torque, decreasing energy efficiency and increasing utility costs.
What causes voltage sags and swells?
The most common causes of voltage sags are loads turning on. Voltage sags can also happen due to impedance problems, such as loose wiring or improper cable sizes for the load requirements.
Swells in voltage can be caused by loads on the system being turned off as well as by switches being activated or line to ground faults causing voltage swells.
How to identify voltage irregularities
- Interview all the stakeholders in the environment to document and understand the problems each individual is experiencing. This process helps avoid unnecessary investigation into the origin of the problem and helps determine if the problems are isolated to one particular area of the plant.
- Once the location or locations of possible electrical problems have been identified, inspect the electrical panel for loose connections — either by using a thermal imager, visually, or by de-energizing and securing the panel to check proper torque. Correct any loose connections found.
- Take simple meter measurements with an appropriately rated multimeter at panels and subpanels to confirm proper voltages.
- If supply voltages are normal — and dips and swells are still occurring even after loose wires have been corrected — connect a power analyzer with recording capabilities to better understand what is going on with the electrical systems at all times of the day. Ideally, record for at least a week.
Power analyzers capture the ongoing voltage and current to help determine the cause or source of the problem. If both the current and voltage drop at the same time during a voltage sag, the cause of the voltage sag was most likely internal. If the current remains constant, the most likely cause of the sag is external.
While voltage swells occur less frequently, the power analyzer can still help identify the source of the problem. Look for line-to-ground faults on single-phase lines, which can cause the voltage to suddenly swell on the two non-faulted phases.
How to resolve voltage irregularities
- Correct any loose connections and ensure proper grounding.
- If voltage irregularities are still occurring, other mitigation options include installing suppressors, filters, isolation transformers, voltage regulators, or power line conditioners. An uninterruptible power supply (UPS) system is another option that employs different technologies to improve power. However, it comes at a higher capital cost.
- After mitigation solutions are employed, ask operators and other stakeholders to keep a log to report any continuing problems. You can also continue using a power analyzer after fixes are in place to ensure power stability has been achieved.
Conclusion
Voltage sags and swells can cause problems in the short term as assets reset unexpectedly or production slows down. The long-term implications, including damage to assets and increased utility costs, can be even more costly.
Finding and correcting the root causes of voltage sags and swells is an important part of ensuring quality power supply in your facility. Addressing these issues reduces overall costs and increases uptime. Even if your plant isn’t currently experiencing symptoms of voltage sags or swells, performing power quality studies from time to time can help identify potential corrective actions that not only improve equipment performance but also reduce energy consumption.
About the Author
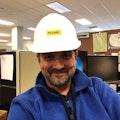
Jason Axelson
Jason Axelson is a product application specialist for Fluke. He has more than 15 years of experience helping customers and partners find solutions for power quality, scope meters, and battery testers. He also conducts application training to help diagnose and resolve both technical and product inquiries.