Nearly 100% of electrical workers believe a strong culture of safety is important to keep them safe. Yet, those same electrical workers believe that less than half of all companies actually have a strong safety culture, according to a survey (conducted by Fluke in February 2020 among 200 maintenance managers and electrical professionals in North America and Europe) on safety attitudes and perceptions. How do companies close that gap? Most realize making a culture change is not easy — that’s where building the right climate comes in.
“Culture is more of an ambiguous way that we describe what a company is doing,” says Chuck Pettinger, Ph.D., a safety expert at Predictive Solutions in Pittsburgh. “Culture is something that’s very hard to manipulate or impact. It’s something that can take three to five to 10 years to change, but if we influence the climate in a positive (or negative) way, over time it can influence the culture itself.”
Instead, Pettinger recommends starting the process by creating a positive climate of safety. This will lead to a culture of safety over time as the work toward a climate of safety is done on a daily basis. When a strong climate of safety is reached, the gap will close and help the culture of safety continue to develop over the years.
How to develop a climate of safety
Pettinger maintains communication is the key to a strong climate of safety. The way safety is communicated — from the top down — makes all the difference. Following are the three main aspects of communication that may need adjustment in order to start seeing a positive change in your safety climate.
1. Metrics
Injury tracking is a common barometer most companies use for evaluating the success of their safety campaigns. However, tracking injury rate or days since the last incident only erodes any other actions toward creating a climate of safety.
“If you have any [visual injury tracking mechanisms] in your companies, I would rip them out,” says Pettinger. “They’re sending the wrong message.”
Instead of influencing workers to take the time to be safe, injury trackers pressure workers to avoid reporting incidents. It drives any climate of safety underground and creates a culture of blame and shame should someone break the streak of days since an injury occurred. Pettinger recommends focusing on positive metrics, such as S.M.A.R.T. goals, which are short term and attainable. They are:
- Specific
- Motivational
- Achievable
- Recordable
- Trackable
This motivates employees to partake in the goals and helps push the climate of safety forward. Moving the dial on a culture of safety is a long-term process, so setting smaller, more achievable goals helps everyone feel like they can make a difference.
2. Incentives
Along with the short-term goals, creating incentives around them can help keep workers engaged in the process. Incentives can be a powerful way to influence behavior; however, they must be the right types of incentives. What incentives, if any, does your company currently have in place? What message do they send about safety?
Pettinger suggests planned, spontaneous recognition. Small rewards for reaching certain, positive goals — for example, bringing in coffee for finding and correcting 1,000 safety issues. Choose an incentive that will boost morale and celebrate the good work toward an improved climate of safety.
3. Training
A huge part of safety is centered around proper training, yet less than 30% of workers believe companies provide adequate safety training. Whether companies have outdated, inadequate, or a complete lack of safety training, one thing is certain: There is a huge opportunity to ensure electrical workers are getting the best training necessary so they can return home safe and sound every day.
Sitting through training classes is okay but not the best way to ensure workers are trained. The information they are given may not necessarily be applicable to their day-to-day work. According to Pettinger, safety training should be personalized to the student. “The best teachers are the ones that adapt their styles to their class. That definitely makes a more impactful learning experience. Everybody learns differently,” he says.
Training can continue outside of the classroom. For example, when a manager notices a worker has put himself or herself at risk for an injury, the manager should take a few minutes to have a conversation and coach the employee. Use these coaching observations as learning opportunities for employees — walk them through what the issue was and how to fix it. This will help individual employees see a positive climate of safety because it helps remove the “policing” aspect of inspections, allowing employees to remember what they’ve been taught.
Closing the Safety Training Gap
The survey identified a gap between the importance of a strong culture of safety and what companies are currently providing. By implementing the best practices discussed above and changing how managers/employees communicate about safety, companies can build a strong “climate” of safety that will turn into a long-term “culture” of safety over time.
Silvey is an application specialist with Fluke Corp., Everett, Wash. He can be reached at [email protected].
About the Author
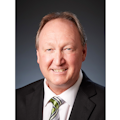
Sean Silvey
Application Specialist
Sean Silvey is an application specialist for Fluke, which manufactures electrical test and measurement tools, including multimeters, clamp meters and insulation, earth ground and installation testers. Sean Silvey has been an application specialist at Fluke for the past seven years. Prior to that, he was a residential/commercial HVAC technician, most recently a field service manager. Sean’s focus is on application awareness and product education; and most recently, he has been building expert knowledge in the Clean Tech fields of solar and eMobility, helping Fluke drive innovation of tools that help technicians in these fields get their work done safely and efficiently.