The first thing to understand is there is a difference between an unsafe condition and unsafe working conditions. You may encounter an unsafe condition such as the circuit you wish to work on is energized. You solve that through lockout/tagout. If your employer insists you “work it hot” without also insisting on and supporting going through the energized work permit process [NFPA 70E, Article 130], then you have unsafe working conditions.
In this particular instance, you would simply refuse to proceed with the work. Your employer cannot lawfully compel you to do otherwise. If your employer penalizes you or intimidates a coworker into proceeding with the work, that is a hostile work environment in addition to being unsafe working conditions.
Normally, it’s not the company per se doing this but a lower-level manager or supervisor. A visit to the plant engineer or the plant manager should quickly clear that up. But if not, report the incident to both your company’s EEOC representative (typically the HR Department) and your company’s safety manager.
Let’s look at some general types of unsafe working conditions and what you can do about each one:
- Inadequate working space around electrical equipment. The typical cause is the misconception among nonelectrical managers that you should try for 3 ft of space if you can get it. Correcting this is nearly always a matter of showing why the existing space is inadequate, showing the OSHA or NEC working space tables, and showing 110.26(A) from the NEC. 110.26(A) requires the space to be adequate for maintenance and other functions, rather than stating it just has to meet a mark on a ruler. OSHA has a similar language in 1926.403(j)(3).
- Your work space is congested. When there are too many people crammed into too little space, it’s usually not intentional. In construction, it sometimes happens that a scheduling mistake results in two trades working in the same space, perhaps drywallers and electricians. The solution there is for the crew foremen to work something out. Speak up about any such problem and follow through to ensure it’s fixed.
- Poor housekeeping. This should never occur. Parts boxes have been opened and just left there, a drive belt was replaced and the old one left on the floor, a motor was lubricated but the grease drop not cleaned from the floor, etc. Or maybe it’s a mess left by people outside your department.
An appliance plant in Tennessee got a new plant manager, and he made a point of picking up candy bar wrappers as he walked around the production floor. He would hand these to a randomly selected hourly employee and ask them to throw the wrappers in the trash. Set an example by cleaning up behind yourself (don’t strip wire and not pick up the scrap!) and reporting to the responsible manager any housekeeping messes you see.
- Fire hazards. These include such things as containers of flammables not being stored in the flammables locker. If there’s a fire hazard in your work area and you can easily fix it by putting a can of flammable solvent into the flammables locker, fix the problem. Same thing if cardboard boxes are piled up near electrical equipment, such as when an electrical closet is used as a file storage area. But always report the problem. If it’s not something you can easily fix, report the problem and explain why you can’t fix it and that work is stopped while the problem exists.
- You’re given a task you are not qualified to do. This is nearly always unintentional. Just tell your supervisor you are not qualified to perform that task. Make sure to distinguish between doing the task under qualified supervision for training purposes and simply being given the task.
- Your equipment is defective. For example, there’s only one 12 ft ladder available and it has a broken rung. Don’t use that ladder. Take it out of service and report it to your supervisor. See if there is another piece of equipment you can use in its place (e.g., a taller ladder or a scissor lift).
- A coworker operates equipment in a way that endangers you. Perhaps the most common example is an electrician holds one digital multimeter probe in each hand and brings them both toward energized terminals at the same time. There is not time to debate this or report it, you must immediately restrain one arm or push it to the side.
About the Author
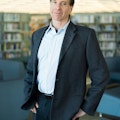
Mark Lamendola
Mark is an expert in maintenance management, having racked up an impressive track record during his time working in the field. He also has extensive knowledge of, and practical expertise with, the National Electrical Code (NEC). Through his consulting business, he provides articles and training materials on electrical topics, specializing in making difficult subjects easy to understand and focusing on the practical aspects of electrical work.
Prior to starting his own business, Mark served as the Technical Editor on EC&M for six years, worked three years in nuclear maintenance, six years as a contract project engineer/project manager, three years as a systems engineer, and three years in plant maintenance management.
Mark earned an AAS degree from Rock Valley College, a BSEET from Columbia Pacific University, and an MBA from Lake Erie College. He’s also completed several related certifications over the years and even was formerly licensed as a Master Electrician. He is a Senior Member of the IEEE and past Chairman of the Kansas City Chapters of both the IEEE and the IEEE Computer Society. Mark also served as the program director for, a board member of, and webmaster of, the Midwest Chapter of the 7x24 Exchange. He has also held memberships with the following organizations: NETA, NFPA, International Association of Webmasters, and Institute of Certified Professional Managers.