Avoiding Problems with Pneumatic Tools and Compressed Air
Pneumatic tools are commonly used on construction sites, usually with portable compressors. And it’s the rare manufacturing plant that doesn’t have a plant air system, and along with it a variety of equipment that runs on compressed air. That equipment includes not just pneumatic hand tools but also actuation cylinders, pneumatic motors, and other equipment upon which production relies.
A common misconception is that what comes out of a nozzle on a compressed air hose is only air. It is nearly always a mixture of air and oil, though oil-free systems do exist. If compressed air is routinely being released into an occupied space (e.g., an assembly line with human operators), then adequate ventilation must be provided.
You never blow this air on you to cool off, dry off, or clean up. Partly that’s because of the oil; not only will you be breathing the oil, you can inject it deep below your skin with painful and fatal results such as an embolism.
The standard pressure on these systems is traditionally 80 psi. But for safety reasons, that may be throttled down to 40 psi. Don’t be fooled; a blast from a 40-psi nozzle four inches from your ear drum will rupture it. And you can still drive material through your skin.
The solution would seem to be to lower the system pressure to a level where nobody can get hurt but the tools still operate. Where would that be, exactly? At 12 psi, the air from a nozzle can pop an eyeball out of its socket. Even at 4 psi, it can cause a fatal injury; an old shop prank consists of “goosing” someone with a shot of air. However, 4 psi can rupture the person’s bowels.
In short, there is danger at any pressure that is useful. Treat a pneumatic tool or nozzle like a loaded gun; never point it at anyone.
Some other safety practices:
- Wear safety glasses (with side shields) or safety goggles any time pneumatic tools are being used near you. It doesn’t matter if you are not personally using them; the compressed air won’t know that.
- Treat compressed air hoses like test leads; inspect them carefully for damage before you use them. Don’t try to repair the damage with tape. Either replace the entire hose or use an approved repair method such as cutting out the damaged part and joining the ends with approved fittings.
- Ensure fittings are tight; this includes quick connectors.
- Never pinch or kink (fold over) an air hose to regulate or stop the airflow. This can result in a hose rupture with horrible consequences.
Pneumatic tools have a long history of being widely used in manufacturing. They also are used on construction sites. They are sometimes the tool of choice over a battery-powered or line-powered tool, especially in hazardous locations. Just as compressed air isn’t “free” (it costs more per unit of work done than electricity does), it’s not inherently safe either.
About the Author
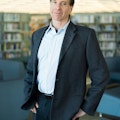
Mark Lamendola
Mark is an expert in maintenance management, having racked up an impressive track record during his time working in the field. He also has extensive knowledge of, and practical expertise with, the National Electrical Code (NEC). Through his consulting business, he provides articles and training materials on electrical topics, specializing in making difficult subjects easy to understand and focusing on the practical aspects of electrical work.
Prior to starting his own business, Mark served as the Technical Editor on EC&M for six years, worked three years in nuclear maintenance, six years as a contract project engineer/project manager, three years as a systems engineer, and three years in plant maintenance management.
Mark earned an AAS degree from Rock Valley College, a BSEET from Columbia Pacific University, and an MBA from Lake Erie College. He’s also completed several related certifications over the years and even was formerly licensed as a Master Electrician. He is a Senior Member of the IEEE and past Chairman of the Kansas City Chapters of both the IEEE and the IEEE Computer Society. Mark also served as the program director for, a board member of, and webmaster of, the Midwest Chapter of the 7x24 Exchange. He has also held memberships with the following organizations: NETA, NFPA, International Association of Webmasters, and Institute of Certified Professional Managers.