You have a job to do, and your employer has a lockout/tagout (LOTO) plan that is compliant with both OSHA 1926.417 and NFPA 70E, Art. 120. The problem is those standards don’t seem to have anticipated a particular obstacle you now face. You have some options, but what decision do you make? Let’s consider three obstacles that have cropped up at various facilities.
Obstacle 1: Full hasp
You want to hang your lock on a breaker, but it already has a hasp on it, and every hole on the hasp has someone else’s lock. Among those is a “master lock” assigned to the operations shift supervisor. The master lock means whoever is the shift supervisor can remove the lock; a record is kept in a book on the shift supervisor station.
Options:
- Ask the shift supervisor to remove the master lock so you can hang another hasp there, and they can master lock the new hasp. This does not work because neither lock is actually locking out the breaker.
- Remove someone else’s lock and hang yours. In most companies, doing this once will end your employment there for good reason.
- With that many locks on there, what can possibly go wrong? Hang your tag, and get on with the job. The flaw here is you have not protected yourself. What if everyone else removes their locks, and then someone closes the breaker?
Try one of these two solutions:
- Inform your supervisor of the situation and move on to a different job. Come back to this one later.
- Advise everyone with a lock of the situation, and ask them all to meet you at a predetermined time to remove all locks, hang a longer hasp, and replace all locks.
Obstacle 2: Outdated drawings
Any facility without a controlled drawing program will inevitably present this problem. Before starting the job, obtain the latest drawing from the master library. If the drawing doesn’t seem to match the installation (e.g., some detail is off, such as the last digit of the asset number is not the same), what should you do?
- Apply common sense, and choose what most seems to be right. The flaw here is things aren’t always what they seem.
- Go by the drawing, since it’s the official document. Doing this or going by the equipment gives you a 50-50 chance of being wrong. Those are terrible odds.
- Refuse to do the job, telling your supervisor that “they” need to “get their act together.” This shirks responsibility. Instead, ask your supervisor whether she wants you to figure out, solve the problem, or go on to something else for now. There’s no “they” to do this.
To figure out this problem, you’ll need to put all the clues together and verify each one. For example, you’re working on the scrap grinder for Line 6. The drawing shows Breaker 12 in Cabinet 3C, but a plate above the breaker says Mixer. In Cabinet 3B, the tag above Breaker 12 says Grinder. Maybe the cabinet tags have been swapped, or maybe the drawing simply shows the wrong cabinet. By checking other items in the drawing and in those cabinets, you can determine what’s wrong. If Operations gives the OK, you can also operate the breakers to see which equipment they supply power to.
This goes beyond your immediate need to lock out the supply to the grinder. But it’s a meta level safety problem, and there’s no “they” to solve it.
Obstacle 3: Not enough locks
You have five personal locks, but two are on another project while it awaits parts, and this project requires four locks. As with the other problems, you have options:
- Use your three locks, and just tag the fourth energy source. This ignores the fact it’s LOCKOUT/tagout. You must put a lock on each energy source after isolating it.
- Remove a lock from the other project, and use it on this one. This has the same flaw as the previous solution.
- Borrow a lock from a coworker. This seems like a viable option, but it means you do not have the key to that lock, so it’s not really your lock. It could be removed without your permission.
A situation like this must be escalated to the supervisor. The safest way is to just assign another electrician to the job. But an administrative solution (with sufficient safeguards in place) may also be acceptable under your company’s electrical safety policy.
For example you get a supervisor’s lock put on the other equipment, which allows you to use one of those two locks for your new project. Normally with this type of solution, there’s an extra layer added. Not only will the electrical supervisor hang a lock, but so will another supervisor (e.g., plant engineer or production supervisor), and there’s a log in a book. This prevents inadvertent removal of a lockout. But it also prevents you from removing the lock, so it may severely impede your ability to conduct any needed testing once repairs and adjustments are made. Your supervisor may just assign another electrician to the job and see to it you are provided with additional locks to prevent this from recurring.
In any case, don’t just wing it and hope for the best. Murphy’s Law does not pick convenient times to manifest itself. If there’s an obstacle to correctly hanging a lock, solve that obstacle.
About the Author
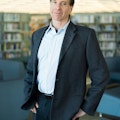
Mark Lamendola
Mark is an expert in maintenance management, having racked up an impressive track record during his time working in the field. He also has extensive knowledge of, and practical expertise with, the National Electrical Code (NEC). Through his consulting business, he provides articles and training materials on electrical topics, specializing in making difficult subjects easy to understand and focusing on the practical aspects of electrical work.
Prior to starting his own business, Mark served as the Technical Editor on EC&M for six years, worked three years in nuclear maintenance, six years as a contract project engineer/project manager, three years as a systems engineer, and three years in plant maintenance management.
Mark earned an AAS degree from Rock Valley College, a BSEET from Columbia Pacific University, and an MBA from Lake Erie College. He’s also completed several related certifications over the years and even was formerly licensed as a Master Electrician. He is a Senior Member of the IEEE and past Chairman of the Kansas City Chapters of both the IEEE and the IEEE Computer Society. Mark also served as the program director for, a board member of, and webmaster of, the Midwest Chapter of the 7x24 Exchange. He has also held memberships with the following organizations: NETA, NFPA, International Association of Webmasters, and Institute of Certified Professional Managers.