In its simplest (and perhaps least effective) form, lockout/tagout (LOTO) consists of three steps:
- Identify the breaker (or fuse) that supplies power to your equipment.
- Open the breaker.
- Hang your lock, and tag on that breaker.
This would make it seem that NFPA70E should have maybe three principles, not eight. What gives?
First of all, that three step process is a simplification. Your lockout/tagout process for a given job could easily involve four or five times as many steps. There is no “one sequence fits all” methodology for locking and tagging out the energy source(s) of a given piece of equipment. If you understand the eight principles, you will see why.
Principle 1. Employee involvement [120.2(A)]. This is first in the list of eight, and not by accident. One way lockout/tagout is sometimes done is one person in a crew performs the procedure, the other members of the crew may (or may not) also hang their locks, and the affected operations team may (or may not) also hang a lock. This is wrong.
The correct way:
- Determine who may be directly or indirectly exposed to the source of electrical energy.
- Involve each of those people in the lockout/tagout procedure.
That’s an additional two steps (per energy source) over the method we describe at the outset. Now, this is just from an electrical safety viewpoint. To fully comply with the intent of the OSHA regulations, expand “the source of electrical energy” to “energy sources that need to be locked out to prevent injury, including non-electrical sources such as kinetic energy and any lockout that involves automatic safety systems.”
An example that helps illustrate a problem with locking out automatic safety systems is a team went into a room that contained a locally venting pressure relief valve for a gas that could be toxic if it vents while they are working at a particular spot a few feet away. They can’t just lock out that valve; they have to take many additional steps (including coordinating with operations) to have an attendant monitor the pressure and manually vent as needed.
Principle 2. Lockout/tagout Procedure [120.2(B)]. You have to develop a custom procedure specific to the equipment to be worked on. You use up-to-date drawings, applicable codes, applicable standards, and other information sources to develop this.
Principle 3. Control all sources of electrical energy [120.2(C)]. Again, don’t limit this to electrical, and consider the job complete. Control all sources of energy, period. Doing this correctly goes back to Principle 2; you must identify those sources by using up-to-date drawings. It’s also a good idea to consult another trade as applicable. For example, you need to work on a 750-ton stamping press, and you have a sneaking suspicion that if the ram falls on you it might get ugly. Should you puzzle this out on your own, or ask the mechanical maintenance supervisor for help?
Principle 4. Render interlocks inert [120.2(D)]. This also goes back to Principle 2. Use up-to-date drawings and other sources of information to ensure that no electrical interlock operation can result in energizing the circuit to be worked on. In some cases, this could require “lock in” rather than lock out.
An example you can use to test this principle is your own automobile. If you want to monitor the parasitic current draw on your car battery you need all the electronics to go to sleep. If you open the hood or a door, the electronics will wake up because of the hood and door interlock switches. So, you use a clamp or other means to hold those switches in the depressed position. Whether the control logic is normally open or normally closed for operation doesn’t really matter for this purpose (though normally open is normal); what matters is the switch doesn’t trigger an energy source to come on.
Similarly, you may have a door switch on a control cabinet to consider. Often, these are used as interlocks to shut down thesystem in case of unauthorized access to the cabinet. Maybe the shutdown sequence includes an operation to clear “work in progress” from the system; that would involve energizing a motor or three. Or maybe there is an interlock that vents or purges process piping. Go through the ladder logic diagrams (or similar) to identify every interlock and what activates it.
Principle 5. Don’t rely on control devices to isolate [120.2(E)]. Apply locks and tags only on the circuit disconnecting means. Don’t try to isolate by locking out switches, selectors, and other control devices. You need to isolate from power, not from just activation.
Principle 6. Use a readily identifiable lockout/tagout device. Generally, this is standardized by each employer or site authority; they will have specific locks issued to specific people and they will have company-issued tags that don’t look like any other kind of tag. Don’t improvise if you run out of locks or tags.
Principle 7. Practice the three elements of coordination [120.2(F)].
- The electrical lockout/tagout procedure must be coordinated with all of the employer’s other procedures for controlling exposure to electrical energy souces.
- The procedures for control of exposure to electrical hazards must be coordinated with the procedures for control of other hazardous energy.
- Electrical lockout/tagout devices can be similar to lockout/tagout devices of other energy sources.
Principle 8. Determine who is in charge [120.2(G)]. For simple electrical lockout/tagout (involving one crew), the qualified person is in charge. For complex lockout/tagout (involving more than one crew), the person in charge of the operation or project has overall responsibility. With a simple lockout/tagout, you remove your locks and tags and re-energize the energy sources as you go.
With a complex lockout/tagout, you may remove your locks and tags but you don’t re-energize anything unless directed by the person in charge. For example, the shift supervisor removes the last remaining lock (hers) from the hasp and then authorizes you to close the breaker.
About the Author
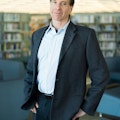
Mark Lamendola
Mark is an expert in maintenance management, having racked up an impressive track record during his time working in the field. He also has extensive knowledge of, and practical expertise with, the National Electrical Code (NEC). Through his consulting business, he provides articles and training materials on electrical topics, specializing in making difficult subjects easy to understand and focusing on the practical aspects of electrical work.
Prior to starting his own business, Mark served as the Technical Editor on EC&M for six years, worked three years in nuclear maintenance, six years as a contract project engineer/project manager, three years as a systems engineer, and three years in plant maintenance management.
Mark earned an AAS degree from Rock Valley College, a BSEET from Columbia Pacific University, and an MBA from Lake Erie College. He’s also completed several related certifications over the years and even was formerly licensed as a Master Electrician. He is a Senior Member of the IEEE and past Chairman of the Kansas City Chapters of both the IEEE and the IEEE Computer Society. Mark also served as the program director for, a board member of, and webmaster of, the Midwest Chapter of the 7x24 Exchange. He has also held memberships with the following organizations: NETA, NFPA, International Association of Webmasters, and Institute of Certified Professional Managers.