NFPA 70E: Electrical Safety — Employer’s Responsibilities for Lockout/Tagout Principles
NFPA 70E lists only four responsibilities that the employer must meet for lockout/tagout [120.1(B)(1) through (4)]. At first glance, it might seem that the responsible managers have an easy “check off the box” situation — but that is not at all the case. A closer look at these responsibilities reveals why.
Responsibility No. 1: Providing the equipment necessary to execute lockout/tagout procedures.
This doesn’t mean providing a communal box of locks. It starts with assessing what each individual employee will need for individual locks.
Save employee time and eliminate legibility issues by having preprinted tags specific to each employee. The tag should have the employee’s name and department at a minimum. Adding the employee’s photo to his or her tags will increase the cost, but many plant managers and service firm operations managers consider this a good investment. Such tags also improve plant security, because they are individually issued rather than ad hoc created from a box of blanks by just anybody. Another reason for having individual, pre-printed, photo-included tags is an employee’s locks and tags must be removed at the end of the shift and resolving problems is much easier this way.
Additionally, the employer needs to provide sufficient gang hasps to permit hanging multiple locks on one energy control device. A common example is Jennifer and John, the two electricians on the job, who each hang a lock. A lock for the production superintendent (which may be issued to the position, not the individual) may also be hung there. An individual operator may also have a lock.
The fact that hanging locks is a requirement also means the employer must provide a lockable means of isolating energy. Some people interpret this to mean “where possible” under the assumption if a circuit breaker doesn’t have this provision then it’s not possible. Adding a disconnect switch between the breaker and the equipment makes this possible. Don’t look for reasons to get away with non-compliance; look for ways to comply.
Responsibility No. 2: Providing employee training.
This doesn’t mean giving them a quick overview in a classroom and having them sign something stating they were trained. You’ll find detailed requirements for such training in 110.6(B). The goal of including these requirements in NFPA70E is to ensure the training produces an employee who understands and can demonstrate correct lockout/tagout procedure to a qualified person and thus is able to correctly perform it in the field.
It’s not about going through the motions to have some kind of defense against liability. It’s about making sure that each employee knows how to create an electrically safe environment through lockout/tagout.
Responsibility No. 3: Auditing the lockout/tagout program.
As with training, there are specific requirements for this also. Those are in 110.5(M)(3). The idea behind these is to identify and correct deficiencies in the procedures. Look not just at what’s said, but how it is said. A technically correct step that is conveyed in an unclear manner is likely to be executed incorrectly (if at all).
Responsibility No. 4: Auditing the execution of the lockout/tagout program.
The specific requirements for this are in the same place as those for auditing the program: 110.5(M)(3). This requirement helps managers see what more they need to do to ensure their subordinates are correctly executing the lockout/tagout procedures.
Make the audit tough, so that even potential weaknesses are exposed. Encourage employees to identify these. Ensure the audits are “safe harbor” events so that people don’t (intentionally or not) hide errors. You can’t correct what you can’t see.
About the Author
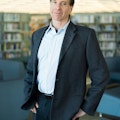
Mark Lamendola
Mark is an expert in maintenance management, having racked up an impressive track record during his time working in the field. He also has extensive knowledge of, and practical expertise with, the National Electrical Code (NEC). Through his consulting business, he provides articles and training materials on electrical topics, specializing in making difficult subjects easy to understand and focusing on the practical aspects of electrical work.
Prior to starting his own business, Mark served as the Technical Editor on EC&M for six years, worked three years in nuclear maintenance, six years as a contract project engineer/project manager, three years as a systems engineer, and three years in plant maintenance management.
Mark earned an AAS degree from Rock Valley College, a BSEET from Columbia Pacific University, and an MBA from Lake Erie College. He’s also completed several related certifications over the years and even was formerly licensed as a Master Electrician. He is a Senior Member of the IEEE and past Chairman of the Kansas City Chapters of both the IEEE and the IEEE Computer Society. Mark also served as the program director for, a board member of, and webmaster of, the Midwest Chapter of the 7x24 Exchange. He has also held memberships with the following organizations: NETA, NFPA, International Association of Webmasters, and Institute of Certified Professional Managers.