Surveys repeatedly show that electrical shock is the most commonly reported work safety issue, even among non-electrical workers. Many of the shock problems result from NEC violations. For example, the first fix on our list addresses what is the perhaps the most common NEC violation in commercial and industrial facilities. Make note of it and five other precautions to reduce this common source of injuries in workplaces.
- Ensure proper bonding of all metallic objects of any significant size. Things like metal placards on walls don’t have to be bonded, but motor cases, motor pedestals, transformer cases, cabinets, enclosures, piping, metallic raceway, panels, and other large metallic objects do. Are people “getting a tingle” at the water fountain? You have a bonding deficiency somewhere because that tingle is current flowing from a higher potential to a lower one. Grounding doesn’t put things at the same potential; only bonding can do that. Carefully read IEEE 142 and Art. 250, Part V. If you see ground rods driven by motors (or any other loads), suspect a bonding deficiency. If you see no grounding connection at a separately derived source (e.g., a transformer), you may have a grounding deficiency but not necessarily a bonding deficiency.
- Inspect bonding path integrity. Raceway is often used as the equipment grounding conductor (ECG). The EGC is actually a bonding system. Electrical metallic tubing (EMT) makes an excellent EGC because of its large diameter relative to the conductors that run inside it. But EMT is often only one type of raceway used in a typical facility. You may also have metallic conduit and metallic cable tray. These different types of raceway must be bonded together using an approved method, such as a bonding jumper. Don’t permit something like grounding them all to a water pipe or the building steel as a substitute for bonding them. When using metallic raceway, also ensure the whole raceway is metallic and mechanically sound or that you jumper around any nonmetallic parts (using a bonding jumper).
- Ensure the EGC does not serve as the return path for unbalanced current. The grounded conductor (which in most commercial, residential, and industrial installations is the neutral) is not the same as the grounding (or bonding) conductor. The grounded conductor carries return current. It does not put metallic objects at the same potential. Consider 277V lighting, which is very common for industrial facilities. It’s a single-phase load, and you run three wires to the ballast (or, in the case of LED, the power supply). There’s the black power wire and the white neutral wire. Bonding the neutral wire to the raceway doesn’t ground the luminaire; it simply energizes the raceway to a dangerous voltage (whatever imbalance the neutral is carrying, and it can be lethal). The green wire of the luminaire connects to a grounding (bonding) terminal to which the supply ground (green wire) is also connected. A properly connected metallic raceway secured by a locking nut to the metallic fixture will also ground (bond) the fixture to the EGC. But there is no connection between the white and green wires at any time (or there shouldn’t be). A facility with a high rate of electronics failure had only this connection (neutral terminated to the raceway, instead of being run inside it as an insulated conductor). So basically, they were feeding the imbalance of a 277V circuit to the ground connections of electronics power supply modules. Since the MOV that protects such supplies is connected across the neutral and hot, this rogue connection meant there was no protection against overvoltage either. How did the undesired current make its way back to the source? By flowing through all paths before it, including metallic panels operators touched. It wasn’t just circuit boards and power supplies getting shocked.
- Inspect test leads before and after each use. A large facility with a metrology lab typically has spools of test lead wire, so the lab can inexpensively replace your test leads. For most electrical firms and maintenance shops, an easy solution is to just stock spare test leads that are OEM. Typically, test leads fail at the probe connection (where all the stress is). But the jacket can also be compromised by such things as sharply bending the lead, walking on the lead, or using the leads as a suspension device.
- Don’t give bad test leads a path across your heart. The old school way of using test leads is to pick one hand to be your test lead hand and put the other in your back pocket. This way, if you have damaged leads or your hand makes contact with a bare probe connection (which is usually due to a boot not being properly secured), you might get a nasty shock, but the current won’t travel through your heart. Wearing the correct gloves for the voltage will also help.
- Check all enclosures for missing hardware and unused openings. An electrical services firm in Tennessee sent an electrician to troubleshoot a production line problem that, among other things, included random shocks to operators The electrician did a walkdown before touching anything and noticed that a large panel was missing every other bolt in its cover. He deemed the equipment to be unmaintained and thus unsafe for access without a hot work permit, which meant a lot of extra time and money. The electrician also documented over a dozen unused openings that were still open. He said this kind of situation is a big clue when you have equipment reliability problems. The problems included poorly made connections, and that poor workmanship inside the panel was not surprising considering the poor workmanship outside the panel.
About the Author
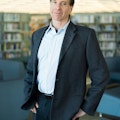
Mark Lamendola
Mark is an expert in maintenance management, having racked up an impressive track record during his time working in the field. He also has extensive knowledge of, and practical expertise with, the National Electrical Code (NEC). Through his consulting business, he provides articles and training materials on electrical topics, specializing in making difficult subjects easy to understand and focusing on the practical aspects of electrical work.
Prior to starting his own business, Mark served as the Technical Editor on EC&M for six years, worked three years in nuclear maintenance, six years as a contract project engineer/project manager, three years as a systems engineer, and three years in plant maintenance management.
Mark earned an AAS degree from Rock Valley College, a BSEET from Columbia Pacific University, and an MBA from Lake Erie College. He’s also completed several related certifications over the years and even was formerly licensed as a Master Electrician. He is a Senior Member of the IEEE and past Chairman of the Kansas City Chapters of both the IEEE and the IEEE Computer Society. Mark also served as the program director for, a board member of, and webmaster of, the Midwest Chapter of the 7x24 Exchange. He has also held memberships with the following organizations: NETA, NFPA, International Association of Webmasters, and Institute of Certified Professional Managers.