Motors beyond a certain size are too heavy and bulky for a person to lift. In the typical industrial setting, there are many such motors. And because of their weight and bulk, they pose hazards beyond just the electrical ones — crushed fingers and strained backs, for example.
The most effective way to eliminate the electrical and physical hazards presented by replacing these motors is to prevent the need to replace them. To do that, address common causes of motor failure such as:
- Voltage imbalance. One reason this may occur is lighting circuits, which are a single-phase load, are supplied by the same phase at a panel. Solution: Rewire to balance out the loads.
- Excess vibration. Causes include improper loading and poor alignment. Solution: Install motor vibration sensors so such problems are readily detectable.
- Incorrect lubrication practices. Overgreasing and the use of incompatible greases are the most common mistakes. Train specific individuals on motor lubrication so that they are “qualified workers” for this task, and assign the task only to them.
So let’s say despite your best efforts, a motor fails anyhow. What happens if your team removes the existing motor, installs the new one, and only then discovers the replacement has a bent shaft? This is not nearly as rare as it should be. You can ensure it never happens by performing a quick runout check on the shaft in the receiving area. A similar problem arises with motors that are stored for years in a stockroom without regular maintenance being performed on them. Think about what steps you can take to ensure you replace one motor — not two — when an installed motor fails.
If all of the preceding concerns have been addressed, you’ve eliminated quite a bit of risk. But you still have to change the motor. Some preliminary steps:
- Make arrangements with the operators for the necessary downtime so there’s no “hurry up and finish” pressure during the change. Such pressure leads to mistakes the crew otherwise would not make.
- Prepare the area. Clear the installation site of anything (e.g., boxes) that is in the way. Plan out the extraction path all the way to the point where you will be taking the old motor to. Then plan out the path from where the new motor is to where it will be installed. Use yellow or red barrier tape as needed.
- Prepare the equipment. Ensure you have everything you need to avoid stopping mid-job to get a needed item (e.g., an extra sling, alignment tools, shims, etc.). If you do a dry run, you’ll identify such deficiencies. You’ll also observe vertical and horizontal clearances, either of which may have changed since the motor was first installed.
- Obtain replacement fasteners. Once a fastener is stretched to its elastic limit by applying the proper torque, it will not have the same clamping power if retorqued. It’s a one-shot deal. Have the replacement fasteners ready.
- Perform the lockout/tagout. It’s not enough to just lock the disconnect open. Look for any other energy sources. For example, if the motor is part of a punch press make sure the ram is either completely lowered or properly blocked.
- Assign specific tasks to each individual involved. This will keep people from working over other people. This should be covered in your job briefing [NFPA 70E, 110.3(I)(1)(3)(a)].
During removal:
- Discard old fasteners, connectors, tape, etc., into designated containers rather than tossing them on the floor for later clean-up. This eliminates a tripping hazard for people, and it also eliminates a potential wheel binding problem with your lifting device.
- Never let hands or feet be below the motor. If you need to nudge the motor, use a prybar or similar. If such a tool isn’t handy, you’ll have to go get it. There is no safe way to nudge the motor without an intervening tool.
- Lift the motor only slightly at first. Take a moment to ensure the load is balanced and the slings are secure. If there’s any problem, lower the motor and reattach. Do not attempt to make up for sling deficiencies with manual force.
- Stand clear of the area between the motor and the lifting device.
Setting the new one in place:
- Line up the motor as closely as possible before lowering it, instead of lowering it and then trying to make big moves to nudge it into place.
- Keep hands and feet clear of the motor. Assume the sling can break at any time, no matter how unlikely that seems.
- Leave the weight of the motor mostly supported by the sling until a bolt is inserted into each mounting hole.
You’ll need to snug the motor mounting bolts down to do the rotation testing and alignment. Once you’ve done the final torqueing, ensure your motor vibration sensors are installed, the load is properly connected, and the area is cleaned up. Then check with the operators before putting the motor back in service.
About the Author
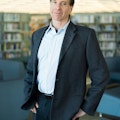
Mark Lamendola
Mark is an expert in maintenance management, having racked up an impressive track record during his time working in the field. He also has extensive knowledge of, and practical expertise with, the National Electrical Code (NEC). Through his consulting business, he provides articles and training materials on electrical topics, specializing in making difficult subjects easy to understand and focusing on the practical aspects of electrical work.
Prior to starting his own business, Mark served as the Technical Editor on EC&M for six years, worked three years in nuclear maintenance, six years as a contract project engineer/project manager, three years as a systems engineer, and three years in plant maintenance management.
Mark earned an AAS degree from Rock Valley College, a BSEET from Columbia Pacific University, and an MBA from Lake Erie College. He’s also completed several related certifications over the years and even was formerly licensed as a Master Electrician. He is a Senior Member of the IEEE and past Chairman of the Kansas City Chapters of both the IEEE and the IEEE Computer Society. Mark also served as the program director for, a board member of, and webmaster of, the Midwest Chapter of the 7x24 Exchange. He has also held memberships with the following organizations: NETA, NFPA, International Association of Webmasters, and Institute of Certified Professional Managers.