There really are no short cuts in maintenance, but there are ways to perform maintenance more efficiently without sacrificing reliability. Here are four maintenance hacks that could take your performance up a few notches.
Hack No. 1
Eliminate steps. This does not mean skip necessary steps; it means analyzing procedures and processes to identify steps that don’t meaningfully contribute to uptime. Often, equipment vendors write a recommended maintenance procedure and try to cover all the bases because they are on the hook for the warranty. So those steps get put into a plant maintenance procedure. How do you know which ones matter?
Start by listing all the possible failure modes, then assign two values to each one of these: likelihood of it happening and severity if it does happen. Where both likelihood and severity are low, it is probably not worth the use of limited maintenance resources to perform the preventive maintenance. You can eliminate the relevant steps or do them less frequently.
But now you need to go back to your failure history and identify failures that have occurred. What maintenance steps would prevent those? If those steps were done, were they done correctly or were shortcuts used to save time? Use the time saved by eliminating needless maintenance to address these.
Hack No. 2
Automate. Power monitoring is an example where automation was transformative. Prior to the advent of sophisticated power monitoring systems, identifying power anomalies was a labor-intensive endeavor that exposed maintenance technicians to energized equipment. Other automation examples include vibration monitoring on motors, temperature monitoring on motors, and the use of permanently installed, special purpose infrared cameras to monitor specific switchgear.
Automatic monitoring works best when it addresses emerging problems, rather than being a rear view mirror or forensic kind of thing. For example, it’s not nearly as helpful to get an alarm on excess motor vibration as it is to get an alarm that the vibration level has increased over time (trending toward bad). Scheduling intervention that prevents a failure is much less costly than addressing a failure that has occurred.
Hack No. 3
Reduce walking. Do you have any idea how much walking occurs with maintenance procedure X on a given day? How much time did Julia spend looking for a stepladder? If she spent a lot fo time looking for it, is that because ladders were hidden in the plant instead of being put in the shop’s ladder corral? How much walking did Robert do back and forth to the shop to perform a repair on line No. 6, which is responsible for 25% of your plant’s revenue? Why is there not a locker or gang box situated near it loaded with the things Robert kept walking back to the shop to get?
Your first step is to start with the most commonly performed procedures and list what tools, test equipment, and materials are needed to perform a given procedure. Then add that list to the procedure. This is especially valuable for repair procedures because when equipment is down its operators are usually idled and of course no revenue is being generated the whole time.
Hack No. 4
Digitize procedures. Procedures written on paper have many limitations that are overcome with digitized maintenance procedures. There are firms that specialize in digitizing procedures for the frontline worker. Many production machines have quirks and customizations known only to the most experienced technicians. When a critical machine goes down and one of those technicians isn’t available, what do you do? By embedding that expertise in digital checklists, you can identify those quirks and customizations in a way that the lesser experienced technicians can readily grasp.
You can also add “how to” videos and “what to look for” videos, especially if field techs are using tablets with these digitized procedures on them. To encourage adoption, roll out such a system gradually and take input from end-users as to what they need or would like to see.
One feature that saves a lot of time is having communication with the CMMS so that nobody has to rekey from paper (or a screen) into the CMMS. This features also solves the “missing data” problem that’s inherent in relying on paper forms as the source of maintenance data for inputting to the CMMS.
About the Author
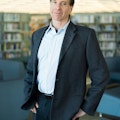
Mark Lamendola
Mark is an expert in maintenance management, having racked up an impressive track record during his time working in the field. He also has extensive knowledge of, and practical expertise with, the National Electrical Code (NEC). Through his consulting business, he provides articles and training materials on electrical topics, specializing in making difficult subjects easy to understand and focusing on the practical aspects of electrical work.
Prior to starting his own business, Mark served as the Technical Editor on EC&M for six years, worked three years in nuclear maintenance, six years as a contract project engineer/project manager, three years as a systems engineer, and three years in plant maintenance management.
Mark earned an AAS degree from Rock Valley College, a BSEET from Columbia Pacific University, and an MBA from Lake Erie College. He’s also completed several related certifications over the years and even was formerly licensed as a Master Electrician. He is a Senior Member of the IEEE and past Chairman of the Kansas City Chapters of both the IEEE and the IEEE Computer Society. Mark also served as the program director for, a board member of, and webmaster of, the Midwest Chapter of the 7x24 Exchange. He has also held memberships with the following organizations: NETA, NFPA, International Association of Webmasters, and Institute of Certified Professional Managers.