Understanding Hazard Communication and How to Implement a HAZCOM Program
Hazard communication is an OSHA requirement established in 1983. This standard pertains to a worker’s understanding of the safety hazards associated with any chemicals they will use during their employment with their associated company. This standard has many requirements that construction and general industry companies must follow to comply with OSHA regulations.
When starting to implement a hazard communication program, also known as a HAZCOM program, it is important to understand five key elements listed below.
The goal is to ensure that workers understand the risks associated with these substances and know how to handle them safely. Here’s a safety representative’s guide to implementing hazard communication program within a company:
1. Chemical inventory
- Maintain an inventory of all hazardous chemicals used, stored, or disposed of in the workplace. This list should be updated regularly to reflect any changes in chemicals or processes.
- Start a company chemical database. Begin with either a written or digital chemical database at your company. There are many online systems that will help track these chemicals and may also help with the next key piece as well.
2. Safety data sheets (SDSs)
- Obtain and maintain SDSs for each hazardous chemical. SDSs provides detailed information on the properties, hazards, handling, and emergency measures related to the chemicals.
- Ensure accessibility: SDSs should be readily available to all employees, often through a central location or digital system. Many contractors have moved to a digital platform to ensure that all workers can access these files within seconds. Online platforms have replaced old-school SDS binders due to their ease of use and time-saving capabilities. Binders need to be updated, and paper copies need to be kept on-site at any site locations where a company has workers. Logistically, this would be a nightmare for contractors that are spread across multiple sites.
3. Labeling
-
Label all containers of hazardous chemicals with the appropriate hazard warnings. Labels must include the product identifier, signal words (e.g., Danger, Warning), hazard statements, precautionary statements, and the manufacturer's name and contact information.
-
Ensure labels are legible and maintained in good condition.
4. Employee training
-
Conduct training programs for employees on hazard communication.Training should cover. OSHA has provided training information and materials companies can use to train their employees on the following topics:
-
-
Understanding the labels and SDS.
-
-
-
Proper handling and storage of hazardous chemicals.
-
-
-
Emergency procedures and first aid measures.
-
-
-
The company’s hazard communication program and how to access relevant information.
-
- Provide training for new employees. The best way to complete this training would be during an employee’s new hire orientation. Make this training a part of the onboarding process.
5. Written hazard communication program
-
Develop and implement a written hazard communication program. OSHA and other online resources can help provide templates that will make writing the program an easier task to take on. Use the templates as a guide and mold them to your own specific company’s
-
The HAZCOM Program needs to include the following:
-
-
The scope of the program.
-
-
-
Procedures for labeling and maintaining SDS.
-
-
-
Methods for informing and training employees.
-
-
-
Procedures for managing and updating the chemical inventory.
-
-
Review and update the program regularly to ensure its effectiveness and compliance with regulations.
About the Author
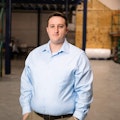
Kevin Kolhonen
Kevin Kolhonen is an experienced safety professional with a demonstrated history of working in the insurance/safety fields with specialization in the energy, construction, and transportation sectors. Currently, he is the health and safety manager at JM Electrical, a specialized electrical contractor in Greater Boston. As safety manager, Kolhonen is responsible for wide-ranging assignments, including the implementation, management, and maintenance of the company’s safety policies, procedures, compliance plans, and improvement initiatives. He also monitors industry regulations, visits construction sites to ensure the safety of the JME team, and establishes communications with field supervisors and field staff among other stakeholders. A graduate of Salem State University, Kolhonen brings significant experience in employee health and safety, loss prevention, and risk management to his role at JME. You can reach Kevin Kolhonen at [email protected] and learn more about JM Electrical at www.jmelectrical.com.